
What Is Thermoforming?
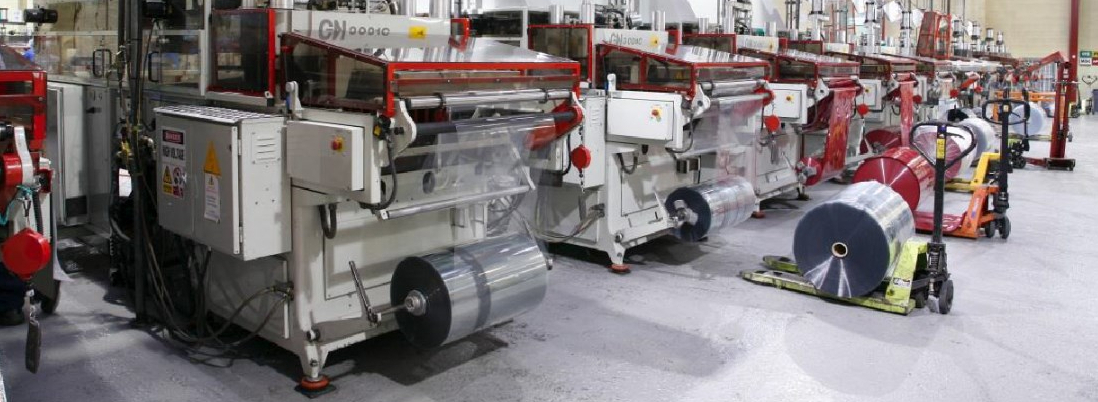
In this article, we delve into the realm of thermoforming, a remarkable manufacturing process that has become a staple in many industries. We'll explore what thermoforming entails, its myriad advantages, and much more.
What Is Thermoforming?
Thermoforming is a versatile manufacturing process used to create plastic parts and products across a myriad of industries. At its core, thermoforming involves heating a plastic sheet to a pliable state and then moulding it into a desired shape using a mould and pressure or vacuum.
Once the plastic cools and solidifies, it retains the moulded form. This process is favoured for its cost-effectiveness, speed, and the ability to produce large or intricate parts with a high degree of precision.
Thermoforming's ability to use a wide range of plastic materials, including PET, PVC, and ABS, among others, adds to its appeal for manufacturers. Its applications are vast, spanning from packaging and automotive components to medical devices and consumer products.
Through innovations and advancements in technology, thermoforming continues to evolve, offering a reliable and efficient method for meeting diverse manufacturing needs.
Advantages of Thermoforming
Cost-Efficiency
One of the predominant advantages of thermoforming is its cost-efficiency, especially when compared to other moulding processes like injection moulding.
Thermoforming requires lower tooling costs as the moulds used are less complex and cheaper to produce.
Additionally, the setup and production processes are quicker, which further reduces manufacturing costs. This makes thermoforming an attractive option for businesses looking to maintain high quality while minimising expenses.
Moreover, the efficiency of thermoforming extends to shorter lead times, making it possible for manufacturers to respond swiftly to market demands and thereby, maintain a competitive edge in the marketplace.

Rapid Prototyping
Thermoforming shines in scenarios where rapid prototyping is essential. Due to its simpler tooling and setup, prototypes can be produced and adjusted swiftly, allowing for faster design iterations and quicker movement from concept to production. This is particularly beneficial in industries where market responsiveness and being first to market are crucial for success.
The expediency of prototyping not only accelerates the product development cycle but also facilitates a more iterative and innovative design process. The feedback loop between design, prototyping, and testing is tightened, ensuring that the final product is refined and market-ready in a shorter timeframe.

Material Versatility
The thermoforming process is compatible with a broad range of plastic materials, offering manufacturers a high degree of flexibility in material selection.
Whether the requirement is for a sturdy, rigid product or a lightweight, flexible one, thermoforming can accommodate various materials including PET, PVC, ABS, and polystyrene among others.
This material versatility also allows for a wide spectrum of finishings and textures, enabling the creation of products that are not only functional but aesthetically appealing as well.
Furthermore, the ability to use recycled materials in the thermoforming process underscores an environmentally friendly aspect, aiding companies in reducing their carbon footprint while still achieving high-quality product output.
Thermoforming VS Injection Moulding
Thermoforming and injection moulding are two prominent plastic forming processes, each with its unique set of advantages and considerations. Thermoforming is generally more cost-effective, especially for short to medium runs, due to its lower tooling costs and quicker setup times. It's an excellent choice for larger, less complex parts and allows for a high degree of aesthetic finish and material choice.
On the other hand, injection moulding, with its higher tooling and setup costs, is often reserved for high-volume production where its initial expenses can be amortised over many units. Injection moulding is capable of producing highly complex parts with tighter tolerances and is known for its consistency and high repeatability across large production runs.
Diagram of Thermoforming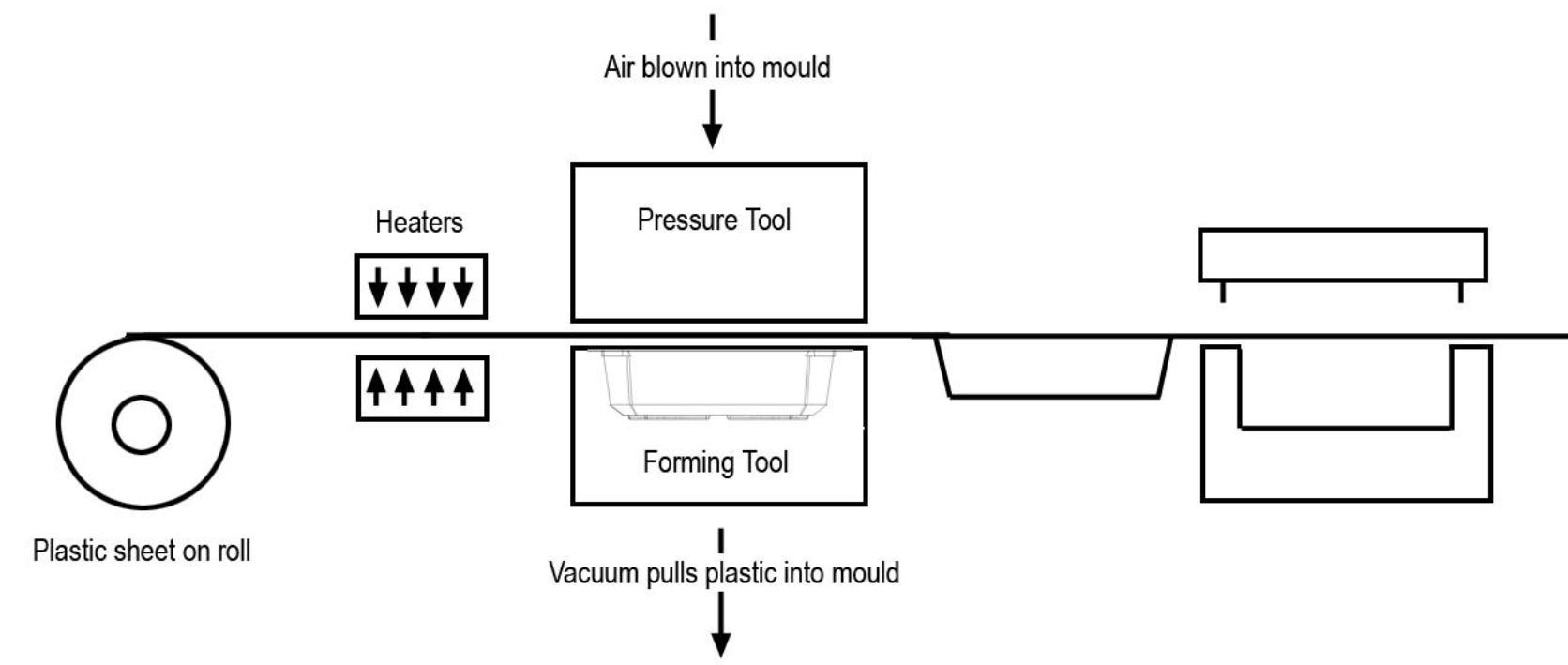
While thermoforming might offer a faster turnaround especially in the prototyping stage, injection moulding is unmatched in its ability to handle intricate designs and deliver precise, repeatable results in high-volume scenarios.
The choice between thermoforming and injection moulding essentially boils down to the specific requirements of a project including budget constraints, design complexity, production volume, and the desired material characteristics of the final product.
Industry Uses For Thermoforming
Thermoforming finds its application across a vast array of industries due to its versatility, cost-effectiveness, and the ability to produce customised parts with a high degree of precision. In the packaging industry, thermoforming is indispensable for creating blister packs, clamshell packaging, and other forms of plastic packaging that protect and display products.
The automotive industry leverages thermoforming for manufacturing various components like dashboards, interior panels, and liners with a perfect fit and finish. In the medical sector, thermoforming is employed for creating surgical trays, device enclosures, and other healthcare-related products that require a sterile and precision-made environment.

The aerospace industry values thermoforming for its ability to create lightweight yet durable components, aiding in the overall reduction of aircraft weight. Additionally, thermoforming is used in the consumer goods sector for creating a myriad of products ranging from disposable cups to sporting goods.
Its ability to mould large and complex parts makes it a preferred choice in industries like construction and agriculture for producing panels, enclosures, and other heavy-duty components. The adaptability of thermoforming to different materials and its capability to meet the diverse design and functional requirements make it a go-to manufacturing process in an extensive range of industrial applications.
For more information on What Is Thermoforming? talk to Plastics By Design Ltd