
Sign In
Advantages Of Pressure Forming
05-05-2022
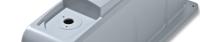
What are the advantages of pressure forming? This article looks at pressure thermoforming and typical applications for pressure forming.
What is Pressure Thermoforming?
The pressure thermoforming process is a fantastic plastic manufacturing technique under the umbrella of plastic thermoforming methods available in the industry.
The manufacturing process of pressure-forming involves a 2-dimensional thermoplastic sheet heated to its optimal in a pressure box. Its heated sheet is positioned over a custom mould or tool.
Professional engineers will then apply positive air pressure above said sheet to bear its weight; its material is pressed into the moulded surface to create a 3-dimensional shape. The moulded part will eventually cool and harden so that engineers can move it onto the next processing stage for further specification.
Advantages of Pressure Forming
Pressure forming has a wide range of advantages and capabilities as it enables professional engineers to create sufficient thermoformed components with immense detail compared to vacuum forming or others.
Customers can get the moulded side of a pressure-formed part identical to an injection-moulded part with a similar airflow. Yet, you may be able to do so at far lower tooling costs than alternative two processes like foam moulding or RIM moulding. Plastic parts that are pressure-formed tend to be a fantastic alternative to fibreglass, wood and sheet metal.
The female mould allows for the pressure forming process to be far more advantageous as the mould can be pre-textured much like an injection mould; however, the textured surface will transfer into the finished product.
You can have embossed wording, style lines, ribbing, moulded-in different textures, tight corners and logo incorporated into the final part.
Its advantages include the following:
It has an immensely high level of precise detail and can conform to various stringent tolerances of the specific industries you require the products for
They are a fraction of the original or a lower tooling cost (approximately 1/3 or less) than you may be expected to pay for injection moulding processes
It is highly cost-effective, especially regarding low-moderate quantities of 300 up to 5,000.It can curate and form parts with functional sharper details and fine cosmetics, for example, undercuts, logos, lettering, louvres and vents
Pressure forming has rapid prototyping properties, and it is relatively quick to market
It can form substantial parts.
Typical Applications for Pressure Forming
Fascias And Enclosures For Kiosks, ATM, And POS Applications
Railcar Interior Parts (Trim, Panelling, Window Masks, Seating, Tray Tables, Luggage Racks, And More)
Enclosures For Medical Device Equipment
Exterior And Interior Covers And Panelling For Industrial
Handling And Construction Vehicles
Pick Up Truck Bed Liners.
Large Equipment Enclosures
Agricultural Related Equipment And Vehicle Components
Common materials used with Pressure Forming
There is a wide range of materials that professionals use for pressure-forming methods, such as:
Acrylonitrile Butadiene Styrene (ABS): Such material includes an extensive array of adaptable resins that strive to meet the UL flammability ratings
Polymethyl Methacrylate (PMMA): This includes a popular plexiglass material with incredible scratch resistance
Polycarbonate is a high-impact plastic capable of resisting immensely high temperatures
Polyethylene Terephthalate Glycol (PETG): This material is known for its formability and durability
Acrylic/PVC: Such material is known for meeting the very highest ranks of UL flammability. High-Impact Polystyrene (HIPS): It is an incredibly low-cost resin
High-Density Polyethylene (HDPE): It is a material perfect for the next projects that require plenty of high-impact strength to complete and is cost-effective
Thermoplastic Polyolefin (TPO): It provides excellent outdoor performance
ABS/PC: You can achieve a stunning high gloss finish whilst attempting to meet the same ratings that one might receive using Acrylics and PVC materials.
Are you looking for Pressure Forming or Vacuum Forming services in the UK? Follow the link below to find out more about our bespoke services.
For more information on Advantages Of Pressure Forming talk to Plastics By Design Ltd
Enquire Now
List your company on FindTheNeedle.