
Unleashing the Power of Flowdrilling
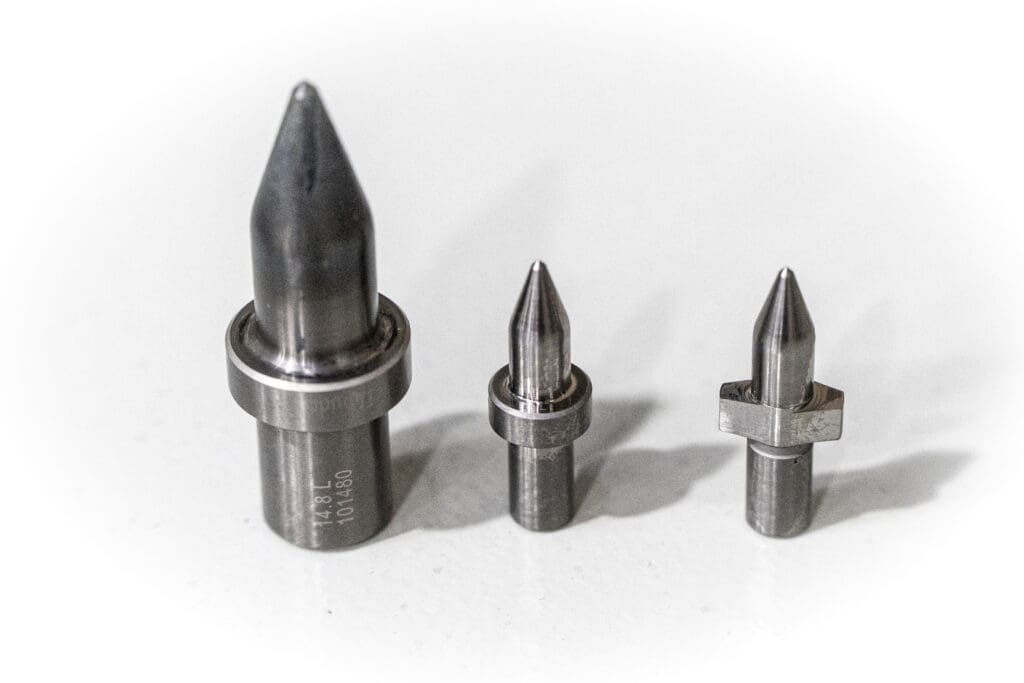
In the dynamic world of metalworking, precision and efficiency are paramount. One revolutionary technique that has been making waves is Flowdrilling, a process that introduces us to a world of possibilities in metal drilling. We’re delving into the intricacies of Flowdrilling, highlighting the game-changing Meyer Pillar Drills that stand as ideal companions in this metalworking journey.
What is Flowdrill? At the heart of this innovation lies the Flowdrill – a solid carbide drilling tool designed to locally displace material, creating increased material thickness. The result? A stronger fastening connection achieved through tapping and brazing. Flowdrill caters to a spectrum of needs, available in sizes ranging from 1.8mm to 40mm, suitable for materials like steel, stainless steel, aluminium, copper, and select brass alloys.
The Flowdrill Difference:
- Increased Material Thickness: A standout feature of Flowdrill, enhancing the strength of connections.
- Suitable for High Loaded Threads: Meeting the demands of robust applications.
- High Process Reliability: Ensuring precision and consistency.
- Fast Production Cycle Time: Speeding up metalworking processes.
- Long Tool Lifetime: A durable solution for prolonged use.
- No Waste, Recyclable: Environmentally friendly with no material wastage.
Typical Applications:
- Threaded connections
- O-ring/sealing surfaces
- Bearing sleeve/hinge
- Brazing joint
Meyer Pillar Drills: Your Gateway to Flowdrilling Excellence When it comes to unleashing the full potential of Flowdrilling, the choice of equipment matters. Meyer Pillar Drills emerge as the preferred companion for this cutting-edge technique. Our range, detailed in this blog post, offers a diverse set of solutions. Notably, the SR32AE and SR50VAE models stand out for their increased motor power and auto-tapping abilities, making them perfectly suited for the demands of Flowdrilling.
Meet the Machines: The Meyer Pillar Drill Range Pillar drills might seem unassuming in a workshop, but Meyer geared-head pillar drills have earned a reputation for quality, robustness, and reliability. Our range boasts machines designed for heavy-duty construction, ensuring a long service life and daily reliability.
The Meyer SR32AE – The Meyer SR32AE builds on the SR32 model, incorporating additional features for enhanced functionality. With automatic downfeed, electro-magnetic clutch, a digital readout for spindle speeds (ranging from 125-3030rpm), and a dedicated tapping mode, it offers precision and efficiency in every operation.
The Meyer SR50VAE – As the largest and most heavy-duty pillar drill in our range, the Meyer SR50VAE weighs in at 655kg and features a drilling capacity of 50mm. Its expansive work table (580 x 460mm) ensures no job is too big. With digital readouts for spindle speeds and spindle strokes, combined with the geared head, powered feed, and an impressive 52-1400rpm speed, precision meets power in this heavy-duty package.
Each Meyer pillar drill is crafted with high-quality components and assembled with the utmost accuracy. Consistently sold worldwide, these machines are a testament to Meyer’s commitment to quality and reliability.
Cost Savings with Friction Drilling: Flowdrilling isn’t just about innovation; it’s about smart solutions that bring cost savings to the table.
- Lighter/Thinner Profiles: No need for material thickening, saving costs.
- Process Improvements: Enhanced efficiency in metalworking processes.
- Reduction of Production Errors: Precision in friction drilling translates to fewer errors.
- Shortened Setup Time: Significant reduction in preparation time.
- Material Savings: Less material waste, contributing to cost-effectiveness.
- No Loose Purchase Parts: Flowdrill offers a complete solution, eliminating the need for additional purchase parts.
Suitable Machines for Friction Drilling: Wondering if your CNC, tube laser, or pillar drill machine is compatible with Friction Drilling? The answer is yes. Our recommendation is a Pillar Drill, they’re cost effective, and quick to change the tooling on. Explore more about your existing machine’s capabilities by contacting us.
What is a Friction Drill Made of? A Friction Drill is crafted from composite Tungsten Carbide powder. The intricate process involves shaping the drill and sintering it into a semi-finished product, which is then processed into the final product at the Flowdrill factory in the Netherlands.
Tapping After Friction Drilling: Post Friction Drilling, Flowdrill recommend using a cold forming tap for several reasons. Cold forming tapping deforms the material instead of cutting it, leading to chipless operation, improved productivity, and high thread strength.
Strength of Friction Drill Connection: The strength of a Flowdrill connection is exceptional, surpassing alternatives like clinch nuts or flange nuts. For example, a friction drill connection effortlessly withstands a force of 2.7 tons in 2.0-millimeter-thick steel – stronger than an 8.8-grade bolt connection.
Up to What Thickness Can I Perform Friction Drilling? Depending on the diameter, friction drilling can be performed up to a thickness of 10 millimetres, based on ST235 mild steel.
Where is Flowdrill Used? Flowdrill finds its application across various industries, serving as a robust and reliable alternative to rivet nuts, weld nuts, and clinch nuts. From automotive to furniture manufacturing, heating and ventilation to bicycle production – the versatility of Flowdrill is evident in its diverse applications.
Is Friction Drilling Proven to be Effective? Absolutely. Friction drilling is a tried-and-true technology with roots tracing back to post-World War II. Flowdrill has continuously refined and improved this technology, making it a daily choice for thousands of customers worldwide. Our Meyer Pillar Drills ensure the quality and performance of friction drillings, with constant RPMs, providing a reliable alternative to traditional connections.
In conclusion, Flowdrilling is more than a process; it’s a gateway to efficiency, strength, and cost savings in metalworking. Meyer Pillar Drills, particularly the SR32AE and SR50VAE models, serve as the perfect companions for this journey, offering enhanced power and capabilities for optimal Flowdrilling results. As you venture into the world of metal drilling, let Flowdrill and Meyer Pillar Drills be your guiding lights.
For more information on Unleashing the Power of Flowdrilling talk to Selmach Machinery Ltd