
Sign In
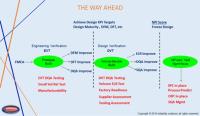
Holistic ‘ is a belief that the parts of something are intimately interconnected and explicable only by reference to the whole’
The meaning of the term ‘Holistic’ is very appropriate in today’s complex Electronic and Electro Mechanical products as we cannot assume performing simple controls and testing samples of product will highlight all the major latent defects which will lead to failure at some point in the products lifetime.
There are many different methods to be employed to fully understand and predict the Quality and Reliability of a New Product, these are often interconnected and all have a part to play in planning how we can best understand and predict the product performance.
Quality engineers have for many years applied PFMEA techniques to try to minimise possible issues, then perform some form of product test to attempt to predict the expected failure level. These techniques are sound, but often produce very little meaningful output unless the design/ process s fundamentally poor.
In fast moving consumer product manufacture there are a wide range of sources that contribute to defects which are not directly related to the original design such as;
- Supply Chain Quality
- Assembly Process capability
- Design Quality issues
- Engineering Changes after Design exit
- Poor Testing / Repeatability
- Low level Accelerated Life Testing
- Etc
The key to achieving High Quality & Reliability is therefore a multi factor solution with focus on measurement wherever possible. Individual measurements alone may not provide the direct correlation to failure rate in the field, but the Holistic combination of the correct measurements certainly will. The key factors and measurements that contribute to minimising failures are highlighted below;
The Key Factors and measurements where appropriate include;
- Design Quality measured as % Design Maturity from Design Quality Assurance (DQA testing)
- Design for Manufacturing (DFM) scoring to measure ease of repetitive manufacture
- Design for Test Scoring (DFT) to measure Design focus on Testability and Test Coverage
- Factory Readiness Review scoring
- Supplier Quality Rating and scoring
- Transparent Supplier Process Reporting
- Supplier Quality monitoring with Early Life escape predictions from Yield measurement
- Early Life Reliability Testing
- Accelerated Life Test failure rate prediction
Only if all are driven to achieve highest possible level can we then expect world class reliability with a new product which can be maintained throughout its production life cycle.
The final step is how then combining the measurements into a simple format that clearly highlights the performance outputs with an NPI matrix, Each element of the NPI matrix will have targets set and depending on the measurements made or defects found, the result of each measurement or test can be easily rated.
This is totally different from a quite normal approach where engineering groups argue over issues and commit to getting everything right before mass production in a hasty and often uncontrolled manner.
Such an approach is always doomed to fail, hence the NPI model brings all the key measurements together for a professional and organised approach to monitoring a products performance from beginning to end in an HOLISTIC manner.
The training on ‘Managing New Product Introduction Quality with an Holistic model’ will guide attendees through a very structured approach using multiple data sources to make NPI measurable and ensure ‘Manage by Measurement’ techniques are used throughout to drive World Class Quality at earliest possible stage
This model has worked very successfully with many of Reliability Solutions clients, if you would like to find out more contact us;
Martin Shaw MD Reliability Solutions
www.reliabilitysolutions.co.uk
email : reliabilitysolutions@yahoo.co.uk
mob : ++44-7967-144097
For more information on Holistic New Product Introduction Quality Management – The Modern Day Solution talk to Reliability Solutions
Enquire Now
More related to Holistic New Product Introduction Quality Management – The Modern Day Solution
List your company on FindTheNeedle.