
What is Blow Moulding?
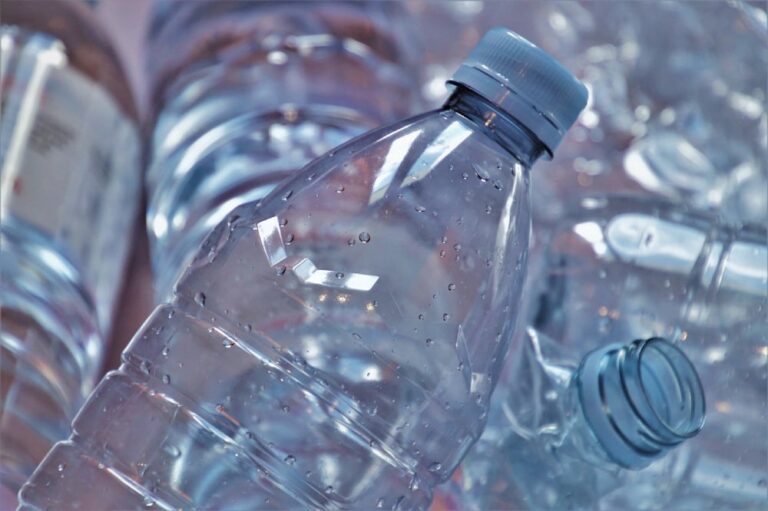
Overview
Blow moulding is a method of producing hollow plastic parts such as bottles and containers. The process starts with melting raw plastic material and creating a parison, a tube-like piece of plastic with a hole on one end. The parison is then placed in a mould, and air is blown into the hole with a rod, causing the parison to expand and take the shape of the mould. The plastic is then cooled and solidified before being removed from the mould.
Blow moulding is a low-cost, high-efficiency manufacturing process used in many industries, including packaging, automotive, and consumer goods. It enables manufacturers to create hollow plastic parts with high accuracy and repeatability and can be used to create parts in numerous sizes and shapes.
What are the Different Types of Blow Moulding?
Extrusion Blow Moulding
Extrusion blow moulding is the most common and simplest production method. It is a continuous process that allows manufacturers to produce large quantities of hollow plastic parts quickly and efficiently. It is commonly used to make containers for applications like food packaging, personal care products, and automotive fluids. The process is highly versatile and can produce parts in various materials, including polypropylene and polyvinyl chloride (PVC).
Injection Blow Moulding
Injection Blow moulding begins with a small amount of molten plastic being injected into a mould to form a preform, a tube-like piece of plastic with a hole on one end. The preform is then moved to a blow mould, heated and blown with high-pressure air to expand and shape it. The plastic is then cooled and solidified before being removed from the mould.
A variety of shapes, sizes, and features can be achieved by manufacturers using the flexible process of injection blow moulding. It is frequently used to produce small, precise parts, like pharmaceutical bottles.
Stretch Injection Blow Moulding
Stretch injection blow moulding is a process that is similar to the others. On the other hand, the stretch step in this process is an essential part of the injection stretch blow moulding process because it enables manufacturers to produce parts with complex shapes and features. It also improves the strength and clarity of the finished product by aligning the plastic molecules in a uniform orientation. Although it has a much higher production rate than the other two types of blow moulding, it is significantly more expensive to set up.
What Materials are used for Blow Moulding?
The materials commonly used in blow moulding include:
- Polyethylene Terephthalate (PET): a thermoplastic polymer commonly used in the production of beverage bottles.
- High-Density Polyethylene (HDPE): a tough, durable and lightweight plastic commonly used in the production of milk jugs and detergent bottles.
- Polypropylene (PP): a strong and stiff plastic commonly used in the production of containers, toys and automotive parts.
- Polyvinyl Chloride (PVC): a flexible plastic commonly used in the production of pipes, hoses and inflatable products.
- Acrylonitrile Butadiene Styrene (ABS): a strong and lightweight plastic commonly used in the production of toys, appliances, and automotive parts.
What Products are made using Blow Moulding?
Some common products made using blow moulding include:
- Beverage bottles for water, soft drinks, juices, and milk
- Containers for household and industrial chemicals, such as detergents and cleaning solutions
- Fuel tanks for automobiles and boats
- Toys, such as balls and inflatable products
- Lawn and garden products, such as watering cans and planters
- Large storage containers, such as drums and barrels
What are the Advantages of Blow Moulding?
- High production rates: Blow moulding machines can produce a large number of parts in a short period of time, making it suitable for high-volume production runs.
- Low labour costs: Once the machine is set up, the blow moulding process requires minimal human intervention, reducing labour costs.
- Low scrap rates: The process is highly efficient, resulting in minimal waste and scrap material, reducing costs.
- High tolerance for dimensions: The process allows for tight tolerances and precise dimensions, ensuring consistency in the final product.
- High strength and durability of products: Blow-moulded products are known for their strength and durability, making them suitable for a wide range of applications.
What are the Disadvantages of Blow Moulding?
- Limited to producing hollow parts: Blow moulding is only suitable for producing hollow parts and cannot be used for solid parts.
- A higher initial investment in equipment and machinery: The cost of equipment and machinery for blow moulding is relatively high compared to other moulding methods.
- Limited to specific types and sizes of products: Blow moulding is not suitable for producing small, intricate parts or parts with thin walls.
- Can be sensitive to changes in temperature and humidity: Blow moulding can be affected by changes in temperature and humidity, which can affect the quality of the final product.
- May require additional post-processing steps: Some blow-moulded parts may require additional post-processing steps, such as trimming or painting, which can add to the cost and complexity of the process.
How Can I Contact the Leading Blow Moulding Companies in the UK & Ireland?
Click here to visit the PlastikCity website, where you can contact the leading blow moulding manufacturers in the UK and Ireland for advice, assistance or a quote for your blow moulding project, free of charge.
For more information on What is Blow Moulding? talk to PlastikCity Ltd