
Shining A Light – Dual Cured Adhesives
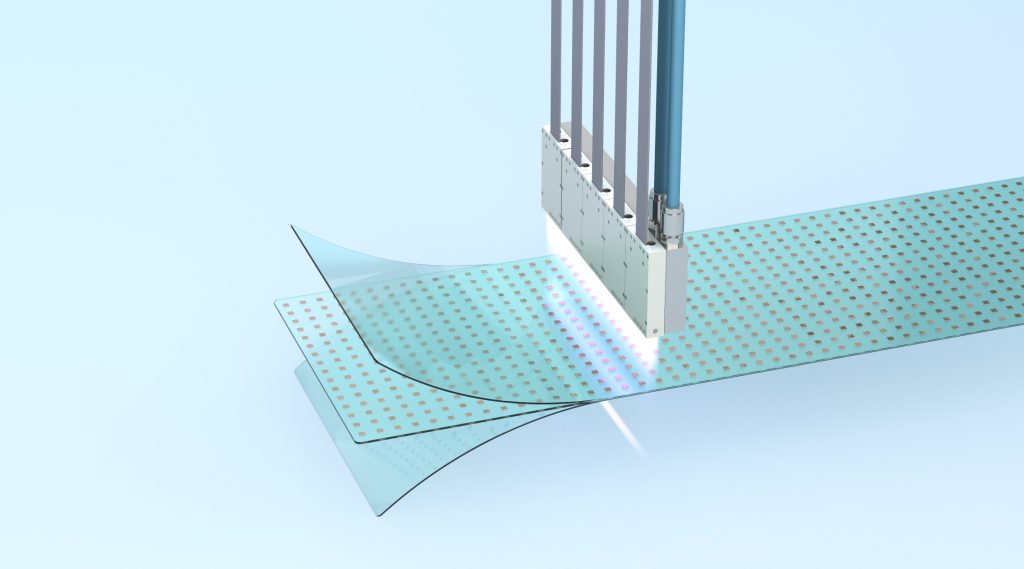
Andover, United Kingdom – First there were light-cured adhesives, then light-activated adhesives, and now we have dual-cured adhesives. Eamonn Redmond, Director of Inseto, provides an overview of all three.

First there were light-cured adhesives, then light-activated adhesives, and now we have dual-cure adhesives. Eamonn Redmond, Director of Inseto, provides an overview of all three.
Though what we’re about to discuss has been the subject of articles before, it’s always worth having a refresher. Also, while many of the overarching principles of bonding have not changed over the years, adhesive chemistries have – which means things like open times (see later) have increased.
‘UV adhesives’ is the generic term used when referring to an adhesive that requires high-intensity light for curing. A significant proportion of these adhesives actually uses light in the visible spectrum for curing. Indeed, it is typically the visible component of the photoinitiator that is used to achieve the cure. This is useful when bonding polycarbonate, for example, as most grades of this material block UV light.
Regardless of where on the spectrum the photoinitiator lies, the simple fact is that one of the parts being bonded must be transparent to allow for 100% cure of the adhesive (see figure 1). No one likes having uncured adhesive in their products on a long-term basis, especially as a number of these adhesives are based on acrylic acid, which is rendered harmless by curing but is hazardous in its liquid state.

When bonding components together, it is essential that the whole volume of the adhesive is fully cured, as uncured adhesive in the finished assembly may cause corrosion or, in the case of optical products, interfere with the light path. However, achieving full cure can be a problem due to shadow areas that light cannot reach.
In this respect, dual cure adhesives can help and there are many on the market that offer significant advantages over more traditional adhesives without sacrificing reliability, bond strength or ease-of-use. Uses include industrial displays, automotive camera modules, electric motors and even simple applications such as thread-locking. Let’s take a look at the two most popular dual cure methods.
Dual Cure: Light & Humidity
These adhesives are used when temperature-sensitive materials are being joined, but they are limited by the fact that the majority of the adhesive in the bond area must be cured by light and by the fact that the humidity-responsive portion of the adhesive cures at a slow rate (typically about 2mm every 24 hours), which is similar to the rate at which silicone adhesives cure.
They are single-part adhesives and are free of isocyanates (so present no health and safety issues) and are free of silicones too (so no impediment to subsequent adhesive bonding), unlike some acrylates. They are highly flexible, optically clear and offer excellent climatic resistance, whilst also providing excellent bond strength on surfaces such as glass, PMMA, metal pins and most plastics.
Dual Cure: Light & Heat
These are based on two diverse chemistries, epoxies and acrylates.
- Epoxies tend to be hard once cured, offering increased resistance to chemical and temperature stresses due to the tight cross-linking of the polymer that occurs during cure.
- Acrylates are usually softer adhesives, enabling quicker curing and greater flexibility of the cured adhesive.
Using a combination of heat and light to cure these adhesives offers a very fast fixation by snap-curing the photoinitiator in the adhesive. Subsequent heat curing ensures that there is no uncured adhesive in any shadow zones that might exist in the assembly. This fast fixation also allows increased accuracy, which is especially useful for companies that have invested heavily in high-accuracy placement machines only to see movement of the parts being bonded during the heat-cure stage.
The heat-cured stage generally involves heating the parts up to around 100°C after the light cure process. However, for temperature-sensitive materials such as some plastics, modified epoxy adhesives are available that will cure at 60°C, combining defined processes and short cycle times, despite the low curing temperature of the adhesive.
These are especially useful in applications such as automotive camera modules, or where the end product is subjected to chemical influences that would otherwise harm an acrylate adhesive. These dual-cured epoxies also exhibit very low outgassing and low yellowing, making them ideal for applications with demanding optical requirements, such as LED assembly.
Dual-cured acrylates offer similar advantages to dual-cured epoxies, namely very fast fixing and full cure after subsequent heat curing, but they also exhibit excellent impact resistance and tension-equalising properties due to their flexible nature. These are suitable for applications such as the assembly of rotary encoders, where optional fluorescing and colouring can be added to aid visual inspection.
Light and heat cured adhesives also offer increased flexibility in the manufacturing process. While heat-curing is mandatory for a small number of these adhesives, the majority offer independent curing mechanisms, allowing curing by light, by heat or a combination of the two.
They do not suffer from the same limitations as light and humidity cured adhesives, however, a downside is the minimum cure temperature is a strict 80°C, which means heating the oven to at least 83°C to avoid any potential cold spots. This is strongly recommended because if the adhesive does not reach 80°C its heat-cured portion will never cure, regardless of how long the parts to be bonded remain in the oven. The time to cure at elevated temperatures can also be a factor. For example, curing at an oven temperature of 83°C might take up to one hour, but at 150°C the cure time might be as short as 10 minutes.
Unfortunately, many modern low-cost plastics are heat sensitive and even 80°C might be a problem. Two-part cold-cured adhesives, such as epoxies and polyurethanes, can overcome this issue but the penalty is long curing times.
Light Activation
For applications where the cycle time needs to be short – i.e., to avoid lengthy humidity or heat cure times – this is where light-activated adhesives come into their own.
The process is simple. Dispense the adhesive onto substrate A, illuminate it with high intensity light for a short period of time, and place substrate B onto the adhesive. Both A and B can be non-transparent.
Illuminating the adhesive provides enough energy to trigger the curing process. However, if too much energy is provided, there will not be enough time to place the second substrate before a skin forms on the surface of the adhesive. Once this happens, it is impossible to bond the substrates.
The time it takes for the skin to form on the adhesive is called the open time. It is measured from when the illumination ceases to when the skin forms. Increasing the energy provided to the adhesive, whether by increasing the intensity of the light or by illuminating for longer, reduces the open time.
Unfortunately, the relationship between the activation energy and open time is not linear. Factors such as substrate material, colour, smoothness and reflectivity all have an impact on the open time. The technical datasheet of the adhesive will indicate a range of open times. For example, the technical data sheet for DELO KATIOBOND 4594 states that an open time of 15 to 20 seconds results from an illumination time of 3 seconds when using a DELOLUX LED lamp with a light intensity of 200 mW/cm2, measured at the adhesive.
Changing the lamp, the illumination time or materials will affect the open time, which should be measured. Also, it’s worth noting that if one the materials being bonded is metal, then it will be necessary to heat it up slightly, to say 35°C. This is because the heat generated within the adhesive during the activation process will be conducted away and slow down the reaction significantly. It may even prevent the reaction completely.
Once the substrates have been joined, full cure will take place over time, typically 24 hours. However, we did say above that light-activated adhesives are ideal for shortening the cure time, and they are because the cure process can be accelerated by:
- Depending on the geometry of the parts being bonded, additional light curing is possible. For example, if there is a fillet of say 0.5mm of adhesive around the joint, a second light cure process can be carried out immediately after bonding (see figure 2). This increases the bond strength, allowing the assembly to be moved on to the next process.
- Alternatively, the assembled parts can be heated (also shown in figure 2). This can seem contradictory as light-activated adhesives are used for the very purpose of eliminating heat from the process. But even the addition of low levels of heat can have a significant effect on the cure speed. As a general rule, for every 10°C increase in cure temperature, the cure time is halved. So, increasing the temperature of the bonded parts to even 45°C (i.e., safe enough even for the modern temperature sensitive materials I mentioned earlier), can reduce the cure time to 6 hours, while ensuring that there is sufficient handling strength in the adhesive to safely carry out the next (assembly) process step.

A recent development on the light-activated adhesives front is ‘activation on the flow’, announced by DELO in 2022. The technology combines adhesive dispensing and pre-activation in a single process step and is considered particularly suitable for bonding and encapsulating temperature-sensitive electronic components.
Another benefit of adding irradiating to the dispensing step is that the exposed adhesive areas can be additionally irradiated (as discussed above) and fixed after joining. This provides immediate initial strength, preventing the adhesive from flowing out and the components from slipping, which allows them to be further processed immediately. Whether with or without additional light fixation, the adhesive cures reliably to final strength without any additional process step, even in undercuts and shadowed areas. For further information on this see FAST magazine news from 25th July 2022.
Summary
So, what has this refresher taught us? Traditional light (only) cured adhesives need one of the substrates to be transparent. Light and humidity dual-cure adhesives overcome the problem but take time to cure. Light and temperature dual-cure adhesives take less time to cure but cannot be used with many heat-sensitive materials.
Light activation, the new kid on the block, initiates the curing process (and marks the start of the ‘open time’). Full cure takes time, but the process can be accelerated using light (subject to it being able to penetrate) or heat (subject to the substrates not being heat-sensitive, though lower temperatures can be used compared to light and temperature dual-cure adhesives).

MAIN ENDS
This article is featured in Issue 3, 2023 of Fast Magazine and is re-produced here with the kind permission of the publisher.
Inseto is exclusive distributor for DELO‘s range of adhesives throughout the UK and Ireland.
Download a PDF copy of this article HERE.
For more information on Shining A Light – Dual Cured Adhesives talk to Inseto (UK) Ltd