
Sign In
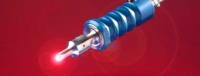
Ultrasonic welding is a relatively new bonding technique that is evolving all the time. Originally discovered in the 1940's, ultrasonic welding uses ultra-high frequency sound waves to bond materials. The fundamental principle is extremely simple; when an ultra-fast frequency soundwave is introduced to some materials, they melt.
This form of bonding technology is unique because of the control that it offers, and its ability to join dissimilar materials. It is used extensively in the aerospace, automotive, medical and plastic manufacturing industries, but in recent years ultrasonic welding has also been utilised in the manufacture of electronics as well. Because all of the heat is localised in the weld area, this method can be used to bond very fragile materials together.
When ultrasonic welding is employed, the throughput times are very short and it lends itself to automated processes. Almost every part of the bonding process is controllable to a level that sometimes isn't possible in other forms of welding. Many industries are looking into ways to take advantage of ultrasonic welding, especially with the rise of nearly fully automated production facilities.
The Ultrasonic Welding Process
At its most basic level, ultrasonic welding is very simple:
Two materials are held together with mechanical force in an ultrasonic press.
On contact a metal tool called a sonotrode (specifically designed for the application) introduces ultra-high frequency sound waves into the materials.
The press is made to direct that energy into the materials at a predetermined weld point.
The materials melt when the high frequency sound is applied, usually in a fraction of a second.
Once bonded, the materials are left to rest under the pressure, and the bond hardens.
The entire process is usually very fast and offers some specific advantages over other welding techniques. Ultrasonic welding creates very reliable bonds, with the energy discharge controlled by a microprocessor. The only heat that occurs is at the point of bonding, and this minimises the risk of unwanted deformation.
When ultrasonic welding is employed there is generally design work needed, with the apparatus being designed to fit the customers’ needs to some degree. Once put into production, ultrasonic welding will create bonds that don't require any other feed material. There is no solder or adhesive necessary, as it takes advantage of the material's ability to deform and create bonds.
Because ultrasonic welding doesn't introduce any more heat than is necessary into the materials, the cooling time is very fast. Usually within a second the bond will achieve its maximum hardness, and will be ready to move on. Manufacturing processes that can take advantage of a fast, reliable bond are ideal for ultrasonic welding.
Current Applications
The use of ultrasonic welding has been growing constantly and is employed by various industries today. Because ultrasonic welding can be used to bond delicate materials reliably and quickly, the electronics industry uses it extensively. It was originally employed commercially to fabricate plastic parts for the automotive industry, and it is still used in that field today.
The bond that ultrasonic welding creates is solid and can be used in sterile environments. For this reason it is frequently employed in the food packaging industry. This capability has also become popular in the medical field, because many medical devices need to be manufactured in clean rooms. In addition to being very fast, the accuracy that ultrasonic welding offers is very useful to the medical field.
Ultrasonic welding offers textile manufacturers the ability to bond synthetic fabrics easily, without having to pay for adhesives or cotton thread. This presents an economic advantage for commercial textile operations that need to do bonding work. It also offers them a consistent product that doesn't pollute or require special materials and can offer watertight seals wear traditional sewing methods cannot.
While the industry has taken advantage of what we currently know about ultrasonic welding, new developments are happening all the time in this exciting field.
Advantages
The advantages that ultrasonic welding offers over other bonding methods are significant in many applications. Because it offers you the ability to bond materials quickly and with little risk, it can be employed in many commercial applications.
Here are the key capabilities that ultrasonic welding can offer your business:
Equipment can be set up for varied applications
Reliable bonds with easy repetition
Inexpensive process, especially if standard machines are used
Various forms will fit with many industrial requirements
Fast cycle times
Easy to monitor
Variety of weld joints can accommodate different designs
Ability to bond non-similar materials
If you have any questions about how to integrate ultrasonic welding into your business, Xfurth can help. We have more than 30 years of experience when it comes to cutting edge bonding technology, and we can walk you through your options. In addition to ultrasonic welding, we supply a range of other joining technologies.
If you have questions about how to implement an ultrasonic welding system in your facility, please let us help you. We are available for consultations via phone or email, or if you would prefer to make an appointment we would be happy to meet you.
For more information on Understanding The Ultrasonic Welding Basics - Where To Begin talk to Xfurth Ltd
Enquire Now
More News
List your company on FindTheNeedle.