
Sign In
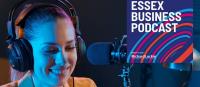
Andy King, Group Technical Director discussed Wernick’s sustainability goals on an episode of the Essex Business Podcast. Episode 19, entitled ‘Sustainability – Why businesses must be at the forefront of the battle’, features key businesses based in Essex and the ways that they are reducing their environmental impact.
Wernick’s Carbon Management Plan and the inherent carbon savings associated with modular construction are discussed from 30 minutes into the podcast. See below for a transcription or click to listen.
ESSEX BUSINESS PODCAST EPISODE 19:
SUSTAINABILITY – WHY BUSINESSES MUST BE AT THE FOREFRONT OF THE BATTLE
ANDY KING – WERNICK GROUP TECHNICAL DIRECTOR
Wernick Group has its head office based in Wickford, and we are a modular building provider, in fact the UK’s oldest modular building provider. We have been established since 1934 and what we do is we design, manufacture, sell and hire modular buildings: these are either temporary or permanent buildings which are used for office, health, education, site accommodation and other infrastructure projects.
WHAT ARE YOU DOING TO IMPROVE YOUR SUSTAINABILITY?
Modular buildings are an inherently sustainable form of construction because they are manufactured off-site, and therefore you have much more control of producing them within a factory as opposed to out on a construction site. But as a company we are now, following the launch of our carbon management plan earlier this year, taking all the ad-hoc projects we have done, and we are focusing them into our goal of achieving a Net-Zero solution for us as a business by 2040.
We are also working with our clients to produce Net-Zero operational buildings, but at the same time we are looking to reduce and remove the embodied energy and embodied carbon contained in our buildings and the emissions coming from our three factories and our 34 other depot locations.
CAN YOU GIVE AN EXAMPLE OF HOW YOU HAVE BEEN DOING THIS IN A FACTORY?
One example is our factory in South Wales which manufactures new modular buildings predominantly for hospitals and schools. We have taken an active decision to remove gas from that facility so on the main factory unit we have installed 50kw of PV panel and we have changed all the internal plant to electric plant and therefore we can use the PV to charge the plant. Externally, we have removed diesel from our fork lift trucks and they now run on HVO fuel.
We have built a separate facility for our composite panel production which has been built as an insulated shed: we have not put gas in here but have put electric panel processes in there instead. We have also installed 30kw of PV panels on the roof to service that. At the same time, we have installed six electric car charging points for those with full-electric or PHEV vehicles.
We are also undergoing the same process at our factory in York where again we are removing gas and changing that over to self-generated electricity.
WHAT ABOUT WITHIN BUILDING THE MODULES ITSELF? WHAT ARE YOU DOING THERE?
We are working closely with a number of our clients to look at generating buildings that are operationally net-zero so that they can sit off-grid or effectively have no bills. The first building as a company that we built to be like this was in 2018 when we built a two-storey office block at Swansea University which was called the Active Office – that was an energy-positive building which annually generated excess energy to charge up vehicles as well as run the building.
So, we have moved on from that and we have looked at not only the technology that goes in the building, but we have also focused on the product design of the actual modular structure, and in a recent development we have redesigned one of our modular systems to our new Swiftplan system with a focus on DFMA where we have looked at design for manufacturing assembly.
The main focus we have had is the elimination of waste and also component reduction, so in the previous system a 12m by 3.6m module used 506 components: in the new Swiftplan system that same 12m by 3.6m module uses only 66 components, so there has been a phenomenal reduction in the amount of components as it’s moved to large format materials.
What it has also allowed us to do is completely eliminate, where possible, single use packaging and allow us to move to reusable stillages. We have also tried to use local suppliers where possible to reduce emissions to site. So when we rolled that new modular system out with the component reduction and the packaging removal, the first building we built was a 28-bay modular building.
Each module weighs in the region of 10 tons, so that building had an over all weight of about 280 tons. During the manufacture of those modules, we generated only 264kg of actual waste, which is the equivalent of 0.1% of the weight of the building which is a phenomenal reduction – it is often mooted that the traditional construction of buildings the waste of materials is in the region of 10% so that is a phenomenal reduction.
Also, with a modular building, you generally have a lighter weight structure and therefore that structure has less of an impact on the ground. With a modular build you don’t tend to dig a big hole and put a concrete raft in, you use much smaller concrete pads or no-excavation foundations so the amount of digging into the ground and waste generated from the site, and also the embodied energy through the concrete is reduced as well.
So, we’re looking at all these aspects to eventually reduce and remove the embodied energy within the building as well as providing an operational Net-Zero building as well.
YOU’RE QUITE EARLY ON IN YOUR JOURNEY TOWARDS NET-ZERO AND YOU HAVE ACHIEVED THIS ALREADY. WHAT HAVE YOU GOT PLANNED TO DO NEXT?
I think we can achieve this with buildings where sold buildings are achieving a net-zero where a client so wishes. At the moment changes in Part L in England are coming in June which are asking for a 27% reduction in emissions; they will change again in 2025.
We are comfortable with working to achieve operationally Net-Zero projects, the key focuses on us are to effectively remove our emissions within the factory so if we look at across our scope 1, 2 and 3 emissions we are actively looking to remove all our sites from fossil fuels as soon as possible, so gas will be the key target to eliminate the use of gas on our sites, and then we will start to look at other aspects of fossil fuel use from them in terms of lighting, heating and other items on the process side.
At the same time we are also looking at the types of products we produce and where the raw materials are procured from in order to ensure that the travelling and the movement of materials to site is minimized where possible to reduce the emissions from them.
Read more about Wernick’s sustainability goals.
For more information on SUSTAINABILITY FEATURE ON ESSEX BUSINESS PODCAST FEATURES WERNICK talk to Wernick Buildings Ltd
Enquire Now
List your company on FindTheNeedle.