
Key Features and Benefits of Huck® Fasteners
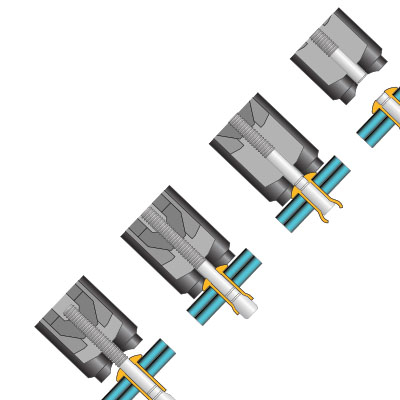
Huck® Lockbolt’s® and structural blind rivets are specialised high-strength fasteners designed for creating permanent and vibration-resistant joints. They are chosen for these applications due to their exceptional shear and tensile strength and ability to provide reliable and long-lasting connections. The versatility of Huck® fasteners allows them to be used in a diverse array of industries where structural integrity is critical and where a strong, permanent, and tamper-resistant joint is required.
Huck® fasteners key characteristics and benefits:
• High Strength: Huck® fasteners offer exceptional shear and tensile strength, making them suitable for heavy-duty and structural applications.
• Vibration Resistance: They are designed to maintain their integrity even in environments with high levels of vibration, ensuring long-term reliability.
• Quick Installation: While specialised tools are required for installation, the process is relatively fast and straightforward, enhancing productivity.
• Corrosion Resistance: Huck® fasteners are available in various materials and plating finishes offering added resistance to corrosion in harsh environments.
• Tamper Resistance: Once installed, Huck® fasteners are challenging to remove or tamper with, enhancing security in certain applications. They can be removed, if necessary, with the correct tooling.
• Accessibility: The structural blind fastener range are ideal when only one side of the workpiece can be accessed.
• Versatility: Lockbolts and structural blind fasteners can be installed in a wide variety of materials, including metals, plastics, and composites.
What are Huck® fasteners used for?
Here are some common industries and specific applications where Huck® fasteners are frequently used:
Construction: Huck® fasteners are commonly used in the construction industry for structural steel connections in buildings, bridges, and other infrastructure projects. From Building a warehouse to installing the door gear, Huck® fasteners have an application.
Transportation: Examples include, truck and bus chassis assembly, securing body panels, frames, and interior components. They are also widely used in the rail industry – track, carriage / locomotive construction and related infrastructure. In aerospace applications, Huck® fasteners are used in aircraft assembly and maintenance, where reliability and strength are paramount.
Infrastructure: Huck® fasteners play a significant role in infrastructure projects. An example of this is the fastening of highway and road infrastructure components, for example signage and (Armco) vehicle crash barriers.
Marine: In shipbuilding and ship repair, Huck® fasteners are used to create strong and corrosion-resistant connections for various marine structures and vessels.
Manufacturing: In general manufacturing applications, Huck® fasteners are used for machinery and equipment assembly, providing reliable and long-lasting connections – applications are endless!
Oil and Gas: For oil rig construction and maintenance, as well as in offshore platforms.
Utilities: Huck® fasteners are used for the installation of utility poles and transmission towers. They are also employed in water treatment and distribution infrastructure projects.
Renewable Energy: In the renewable energy sector, Huck® fasteners are used in wind turbine assembly and maintenance, ensuring the structural integrity of these tall and exposed structures. They are also used in the mounting systems of solar panels.
Agriculture: They find use in the assembly of agricultural heavy equipment, including tractors, farming machinery and silos.
Military and Defence: Huck® fasteners are employed in the defence industry for military vehicle assembly, maintenance, and equipment manufacturing.
What are Lockbolt’s and how are they installed? Click here to find out more
Lockbolt’s, also known as Huckbolts®, consist of a headed pin and a collar that when installed, is swaged into the locking grooves of the pin. The tip of the pin is made up of a series of annular pull grooves. The installation tool (driven by pneudraulic, or battery power), when activated, grips the grooves. The puller in the tools nose assembly draws the pin into the tool. The anvil in the nose assembly is forced down over the collar. Continued swaging elongates the collar and pin, progressively cold forming (swaging) the collar into the grooves of the harder pin developing precise clamp.
The combined pin and swaged collar form the installed fastener providing a permanent and vibration resistant joint.
Lockbolts are renowned for their strength, durability, ease of installation, and resistance to vibration. They are a preferred choice in industries where secure and long-lasting connections are essential, offering superior performance compared to many conventional fastening systems or welded joints.
Lockbolts are a cost-effective fastening solution for industries and applications where reducing labour and installation costs is essential. A combination of quick, straight forward installation and long-term reliability make them a preferred choice for many professionals looking to optimise both time and budget resources.
Huck® LockBolt brand names include, BobTail®, Magna-Grip® (Button head, Countersunk, Rivet head, Truss head, and Broad Truss), C6L® (Brasier head, Countersunk head and Truss head), C50L® (Countersunk head, Round head and Truss head), C120L® and Hucktainer® (also available encasulated); each differing in design, diameter, grip range material, plating and purpose.
What are Huck® structural blind rivets and how are they installed? Click here to find out more
A Huck® structural blind rivet retains the pin in the rivet body (sleeve) post-installation for extra strength.
A standard blind rivet is a single-piece fastener made of two components; the body (referred to as the sleeve) and a pin (referred to as a mandrel). When pulling pressure is applied to the pin, the pin-head applies pressure on the sleeve increasing its diameter on the blind side of the application fastening it in place. A simple yet effective mechanism.
Structural blind rivets are available in sizes ranging from 4.8 mm (3/16’’) up to 19.1 mm (3/4'’).
The primary benefit of blind rivets is that access is only required on one side of the application, meaning typically only one person is needed to install it. The process is fast, clean, and safe, delivering consistent results across the board without requiring skilled personnel.
Huck® structural blind fastener brand names include, Auto-Bulb®, BOM®, FloorTight®, HuckLok®, Magna-Bulb®, Magna-Lok®, Magna-Tite®, and Penta-Lok™.
Huck® Lockbolts and structural blind fasteners are available in a wide range of sizes, head styles, materials and plating’s, offering versatility to accommodate a wide range of applications. Their diversity allows users to choose the most suitable Huck® fastener for their specific needs.
Technical support that will add value to your project
Star Fasteners engineering support services enhances customers experience – we can assist with design, development and testing right through to choosing installation tooling, as well as offering advice on correct fastener installation and process optimisation. Working closely with our customers, we can suggest new products that may not have initially been considered for an application.
For further information, please call +44(0)1159324939 or email sales@starfasteners.co.uk
For more information on Key Features and Benefits of Huck® Fasteners talk to Star Fasteners (UK) Ltd