
Sign In
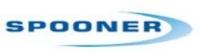
Process Validation– The ability to test your process temperatures, line speeds and limitations before designing your dryer is invaluable. Spooner Industries offers an extensive in-house test and development centre boasts a comprehensive range of pilot equipment to evaluate and develop your new equipment before you make the investment.
The reel to reel high speed coating line to process 500mm wide substrates including paper, film, board, tissue and thin foils. The pilot line is capable of running at speeds up to 1000m/min and has a non-contact flotation dryer. A highly versatile 3-roll coater allows the set-up of most of our customers’ coating methods including a number of gravure techniques, 3-roll reverse, ‘size-press’ and our workshop and manufacturing capability allow us to modify and develop these for specific applications. The newly installed 8-metre dryer incorporates the Spooner HPC Supa-float system arranged in four air temperature and velocity zones. Other equipment includes a Spooner Air Turn to enable coated material to be transported into the dryer without contact with rollers on the back surface and a Corona-treater to enable water-based coating to be applied to packaging films.
Bespoke Design – Your process is unique so your dryer should be customised to the specific demands of your application. Spooner custom design all process equipment to meet with the specifications of their customers. A range of highly efficient dryers from air impingement to air flotation are designed bespoke to exact process requirements.
Spooner dryers combine web handling and the mass transfer capabilities of a conventional flotation system to achieve the heat transfer capabilities and compactness of a typical IR system. The web is supported throughout on a dynamic air pressure pad with high clearance, achieving non-contact web handling. This makes the system effective over a wide range of processes and substrates. The Spooner air float nozzles are located above and below the web path and supplemented by an equal amount of air impingement nozzles. This configuration creates twice the heat transfer of conventional air flotation dryers.
Ease of operation - Making sure you have clear access to within the dryer for cleaning and maintenance is essential for the upkeep of your process machinery. Spooner dryers are designed with a variety of lifting systems eg clamshell, parallel or camel. PLC controls give ease of this operation and can adjust temperature and speed in each zone.
Efficiency- Energy efficiency is a vital consideration before the purchase of any new process machinery. The design of the nozzles for your impingement or floatation dryer can promote more efficient and effective use of what otherwise would be ‘wasted’ air. Additional ways to improve operating efficiency is through energy saving and heat recovery systems designed, manufactured and installed by Spooner. These energy recovery systems offer a typical payback period of circa 2 years and can reduce energy consumption by approximately 20%.
Quality – Quality equipment is developed with the experience and knowledge of the engineers you work with. Spooner was established in 1932 and prides itself on the can-do attitudes of its 150+ employees to provide customers with bespoke, engineered solutions to meet their process and performance requirements on time and on budget. ISO 9001 accredited, Spooner constantly invest in state of the art engineering and business systems in order to ensure that they provide value for money and efficient processing of customer orders. The design team use AutoCad Inventor 3D CAD, and drawings can be transferred directly to the laser machine in the factory. With in-house manufacture, assembly and testing to high quality standards, Spooner can ensure that factory acceptance tests can be carried out in a comprehensive manner prior to delivery to the customer’s site.
Performance – Spooner dryers contain air float nozzles which are located above and below the web path and supplemented by an equal amount of air impingement nozzles. This configuration creates twice the heat transfer of conventional air flotation dryers.
Spooner HPCTM technology provides drying of both low and high tension webs, evaporation rates of up to 200kg/m2/h, unlimited operating widths, operating temperatures of up to 450oC, operation nozzle velocities up to 70 m/s, unlimited machine speeds and variable re-circulation.
Size – Some applications will require longer drying or curing times which would ordinarily result in a greater machine length. Spooner can design their dryers to simultaneously dry and turn with horizontal or vertical configuration depending on the space available. Spooner systems can be particularly effective in maximising drying and cooling length within a limited machine footprint.
Safety – Operation safety is of paramount importance to both your process and your staff. Spooner’s systems are designed to comply with all current safety legislation; mechanical, electrical, gas. In addition Spooner is experienced in the design and supply of systems processing solvents, meeting the very latest ATEX regulations.
Return on Investment – From the outset Spooner aims to provide maximum return on investment by offering high throughput at minimum capital cost whilst ensuring the lowest operating costs.
Aftersales Support – Having a dedicated Technical Service Division, Spooner are with you for the life of your equipment from the training of operators during installation to ensuring the machine runs to its optimum efficiency at all times. The Technical Services Division provides refurbishments and repairs for all makes and models of process equipment as well as original Spooner machines.
Spare parts are readily available and can be made to order for any make or model of process machinery. Spooner’s team of dedicated engineers will quickly source the parts required or even manufacture them in-house to your exact requirements.
Advanced features can be added to your equipment during refurbishment to upgrade to the latest Spooner technology with spare parts manufactured bespoke to requirements in house.
Spooner's Turnkey project management ensures that all activities are coordinated and that all technical, financial, safety and planning targets are met.
For more information on Top Ten Tips for Selecting the Right Dryer for your Converting Application talk to Spooner Industries Ltd
Enquire Now
List your company on FindTheNeedle.