
Sign In
Cleaning up with Spooner Industries
05-08-2015
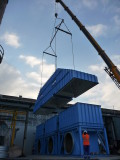
The term “carbon footprint” has been much banded about with today’s increasingly eco-aware population. Arguments still rage about global warming but what we do know is that carbon dioxide, (CO2) is a contributing factor and that humans are responsible for a large proportion of these emissions. Furthermore, the manufacturing industry is often criticised as a key source of harmful VOCs which, in addition to adverse health and environmental effects often have a far greater greenhouse gas effect than carbon dioxide. In fact the total carbon footprint is not something that can be calculated due to the infinite amount of data which would be required, whilst CO2 is produced by natural occurrences. Leaving the latter aside, it is therefore accepted that when we talk about industry sources of emissions, we are referring to indirect or secondary CO2 emissions associated with the whole lifecycle of products we use – in other words the higher the demand, the more emissions will be produced.
These challenges faced by industrial manufacturers are nothing new to Spooner, where problem solving and continuous innovation have been the norm for over 80 years. Initially in the textile industry, Spooner revolutionised the industrial drying techniques of the time in terms of both speed and efficiency and eventually doubled the output of what had previously been achieved.
Fast forward to today and as a leading innovator in the principles of forced air convection technology, the company continues to push the boundaries. A partnership forged with Anguil Environmental Systems in 2008 combined Anguil’s extensive experience of industrial air pollution control and energy recovery systems with Spooner engineering and manufacturing expertise across a full range of plant equipment. This combination now provides a single source solution for industrial facilities to their dryer, oven and air pollution control needs worldwide, with Spooner as the European licensee for the provision of VOC Abatement Systems in Europe.
One of the first sustainable energy solutions that Spooner produced was for a long standing customer Corus (now Tata Steel). Having worked together for over 30 years, the enduring business relationship ensured Spooner had invaluable in-depth knowledge of the plant equipment and layout, operating processes and systems. Corus sort to re-evaluate their entire system as part of on-going manufacturing improvements and wider CSR for energy usage reduction. The initial objective was to reduce gas consumption by at least 45%, whilst increasing the processing speeds on certain products. This would also result in significantly reducing their carbon footprint.
Oven upgrades included: retrofitting each zone with a special low NOX burner to reduce emissions; incorporation of variable frequency drives on every oven fan into the control system for efficiency and reduction of electrical consumption. This upgraded the production line from the least to the most efficient in the Corus group. However, the increased throughput compromised environmental responsibilities overall. Large amounts of natural gas were required for the destruction of VOC and HAP emissions through two inefficient Oxidisers for the Prime and Finish ovens. The Spooner Anguil single source solution provided one RTO to replace multiple air pollution control systems which then delivered the desired efficiency.
The overall reduction in carbon emissions and energy consumption from this facility was dramatic. Gas usage dropped by 60% – saving over £1m a year – and preventing 8,000 tonnes of carbon per year reaching the atmosphere. When Spooner installed a further RTO during the exceptional harsh winter of 2011-12 on a second line, the reduction in gas consumption also meant that production to the plant was not interrupted. In previous years Tata’s power supply could be cut to ensure heating fuel for housing was maintained during cold weather.
Spooner’s unique forced convection technologies incorporate high performance airflow and control technologies together with energy efficient measures throughout. Cleaning emissions and making effective use of excess heat to feed back into the process without disturbance to the process, is a delicate balance, and is where Spooner’s design and engineering expertise also comes in. On production lines the critical factors in terms of oven and dryer air flow include distribution, temperature and heat recovery. Whilst the drive for energy efficiency remains key, this becomes secondary to the maintenance of product and process consistency.
Such was the task when aluminium can stock line customer wished to increase line speed whilst also saving energy. Following the original installation of Spooner ovens at this site many years prior, Spooner had subsequently extended the line and then 12 years later, were called back for further line extension work. Spooner’s long standing installation knowledge and business relationship with the customer assisted the design process and mechanics.
With an extended oven section, an RTO replaced the existing oxidiser and the indirect heating method refined by the addition of a booster burner. A combination of air to air for pre heating reduced reliance on the burner whilst air to water heating provided hot water for pre-treatment of the aluminium strip recovering energy from the RTO. Increased speed was achieved together with substantial energy savings. Today the site remains cost effective and is still maintained by Spooner.
Innovative design and proven technology remains at the heart of Spooner engineering. Selling a concept and delivering a tailored product will continue to be the way the business delivers high quality equipment as a single source solution for the environmental industry.
For more information on Cleaning up with Spooner Industries talk to Spooner Industries Ltd
Enquire Now
List your company on FindTheNeedle.