
Sign In
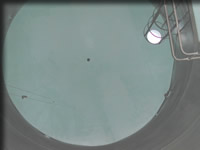
Powergen – Steam Condensate Return Tank Lining.
PowerGen had a steam condensate return tank that had been previously lined some years ago and the lining had failed. The surface of the original internal lining was completely covered in blisters. The tank was quite large, measuring approximately 10m high by 6m diameter and our client was looking for a long term solution. The work was successfully carried out during November and December last year
The system we chose for this project was a vinyl ester based system with glass flake reinforcement. The materials have a proven track record for elevated temperature tolerance, chemical resistance and suitable for use in aggressive tank lining environments.
A complete birdcage scaffolding installed within the tank to give us access to all areas to be treated including the underside of the roof and all accessible flanges and nozzles.
The work was carried out with the use of dehumidifiers to maintain as dry as possible conditions within the tank whilst we were working. Please see notes regarding the use of dehumidifiers.
We used a medium grade grit blast abrasive to remove the old lining, to clean the steel to the required standard and to give us the correct mechanical key on to which we would apply the new lining system.
Following the abrasive cleaning of the surface and a thorough cleaning by an industrial strength vacuum cleaner the application of the lining system then began. The new lining was applied in three coating applications - a primer coat, an intermediate coat and a topcoat. Each coat was applied in different colours to aid identification, to ensure correct wet film coverage and to make spraying easier.
On completion of the work the new lining was tested for micro porosity and dry film thickness. The average dry film thickness of the new lining was 1,500 microns.
The new lining should now have an expected working life in excess of 20 years.
Notes on use of Dehumidifiers when cleaning and lining large tanks.
As this work was carried out during cold and wet weather conditions we used dehumidifiers to ensure the prepared surface was kept from secondary corrosion until the new lining was applied. The use of dehumidifiers greatly extends the working life of new linings inside large tanks. A problem frequently encountered when working in large tanks is how to keep the new blast cleaned surface fresh until the coating can be applied.
The old fashioned method was to blast clean an area during the day and then last thing at night vacuum the area and apply a primer coat. This is all well and good except when blasting recommences the next day there is a strong risk of fine dust particles adhering to the primer. This introduces a third element to the new lining which is very difficult to remove. We have also heard that some companies perform a solvent wash within the tank, which at best would push the foreign matter further into the pores of the surface. This is the complete opposite of what is required or, even worse, creates a highly dangerous situation with risk from explosion due to the high vapour content.
Although it does add to the cost of a project the use of dehumidifiers is the safest method of working.
For more information on Powergen – Steam Condensate Return Tank Lining talk to Specialist Coatings (GB) Ltd
Enquire Now
List your company on FindTheNeedle.