
ATEX Antifoam Transfer Pump
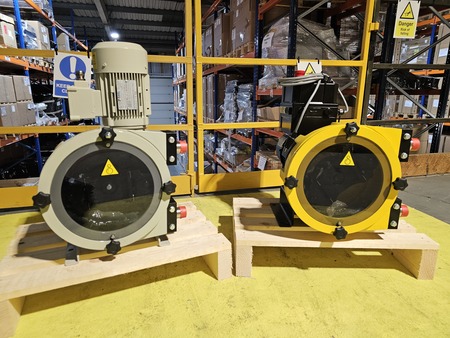
One of our latest clients specialises in wellhead automation and design, and they required a defoaming pump for the transfer of anti-foam which is crucial to the success of their transfer process.
They specified a unit to transfer from an intermediate bulk container, or truck, to a skid-mounted tank to inject the anti-foam which contains traces of kerosene. It had to be ATEX rated and, as space was an issue in the processing facility, the pump had to have a slim footprint.
Wellhead automation is becoming increasingly popular in both onshore and offshore production facilities. It enables cost-effective production, monitoring and safety. The ATEX metering pump we were tasked with supplying would therefore need to be a proven, reliable unit that would operate effectively in this automated environment. It was essential that the pump maintained accuracy and performed as designed over long periods, with minimal maintenance or inspection.
What is anti-foam?
Defoaming is used in various stages in many applications including drilling, well cementing, oil-gas-water separations, refining, storage and transportation.
In the petroleum industry, crude oil foam plays an important role during oil production and processing - drilling, fracturing, acidising, profile control, oil displacement, transportation and refining.
But it can also be a problem in the oilfield industry - from the wellhead all the way to the refining process, storage and transportation. In fact in the gathering station, foam generated in the separator is harmful to crude oil production and the operation of equipment.
If it is not dealt with and removed, foam can cause a variety of problems in the processing process; from production slowdowns and shutdowns, to process fouling and equipment cavitation, all of which lead to loss of production and revenue.
How is foam formed?
During oil and gas production, when pressures are reduced, foam or gas entrainment can form within hydrocarbons adversely affecting production and resulting in increased processing to obtain effective separation. Foam can also be generated within separators should the oil become depressurised, which can effectively reduce separator capacity. Defoamers are used to control foaming within acceptable levels and ensure large separators, which can take up vast amounts of space, are not required.
As part of the specification, the client highlighted that due to the site location, they required an antifoam injection pump which could handle temperatures of up to 65°C while still being fully ATEX compliant.
What is an anti-foam or defoamer?
Foaming can be controlled or eliminated by defoamers. A defoamer, also referred to as an anti-foaming agent is a chemical additive that reduces and prevents the formation of foam in industrial process liquids. The terms defoamer and anti-foam are both used, but to be exact, defoamers eliminate existing foam while anti-foamers prevent the formation of more foam.
Defoamers are very cost-effective, working at injection rates of just a few parts per million. Silicones are the most commonly used defoamers in crude oil and water injection systems. Non-silicone products are available for amine gas treatment units, glycol units for dehydration and water injection systems.
For this client, the anti-foam injection would be transferred by our ATEX peristaltic metering pump. The pump facilitated the transfer of the defoamer which was metered from an intermediate bulk container, or via truck to a skid-mounted tank.
Why we specified a peristaltic pump
Peristaltic pumps are an excellent choice for any number of applications involving the transfer of either small metered or bulk amounts of clean, solid laden or corrosive liquids.
In addition, they perform well when handling liquids which are viscous, abrasive, gaseous and volatile. They are usually specified for use with a variety of fluids from pastes, glues, sludge, food and ink to cement, chemicals and slurries ranging in viscosity from 1 to 50,000cst.
There were seven key factors which lead to us selecting an ATEX peristaltic metering pump for this project:
1. Low shear
One of the main benefits of this pump technology is that they are low shear. This means that they transfer fluids gently without creating foam. In this case the peristaltic pump maintained the separation of the kerosene and anti-foam.
2. Self priming
Thanks to their positive displacement design, peristaltic pumps can self-prime up to 8m vertically, with the inlet and outlet rotated to match the installation specification. This means that they offer the flexibility of fitting in a range of locations outside of the fluid, and not just at the bottom of a tank in a hard-to-reach position.
In addition, motors can be mounted vertically reducing the unit’s footprint and opening up even more spaces for installation.
3. Variable flow, reversible or intelligently controlled
Peristaltic pumps are also known as volumetric pumps. This means that the flow rate is proportional to speed, but pressure remains constant. Their rotation can be reversed, so they can be used in a range of different situations including container filling or emptying. This can also ensure that any equipment connected to the unit, like a hose for instance, can be drained if necessary.
4. Temperature tolerant
Peristaltic pumps can handle temperatures up to 100°C, and operate within large temperature ranges. Compare this with other positive displacement pump types such as progressing cavity pumps which only work within narrow bands of temperatures, and air-operated diaphragm pumps which have an operating limit of 80°C.
5. Low maintenance and easy clean
Peristaltic pumps have just one wearing part – a heavy duty textile inlay hose. When this begins to show wear, it can be swapped out and then recycled or disposed of. All in all, peristaltic pumps are up to four times quicker to clean and maintain than other types of positive displacement pumps.
6. Non-clog, hardwearing and able to run dry
Peristaltic pumps can accommodate solids as wide as the internal diameter of the hose, and because of their gentle pumping action they don’t clog. This design feature makes them well suited to processing food, cement, pastes, sludge, slurries, sewage, and other fluids which can contain large solids, stones or unexpected objects.
In fact, thanks to the tough, hardwearing hose, slow speed and gentle action, peristaltic metering pumps can handle the most abrasive of slurries – anything from mining and biogas, to dewatering and other flows which may contain sharp particles or debris.
Moreover, because there are no valves, mechanical seals or O rings there’s less chance of clogging taking place. That’s because damaging fluids like glues, latex or other abrasive liquids can’t cause seal failure which would allow air to get in, reducing pump efficiency and leading to loss of valuable product.
Finally, the pump’s construction and the absence of valves and seals means it can run dry without suffering any damage. This makes a peristaltic pump ideal for dry, abrasive or viscous sticky liquids which would cause serious issues for other types of pump.
7. Accessories not needed
Unlike other pump designs, peristaltic pumps do not require ancillaries like pressure-loading valves, check valves, filters, dip tubes or level controls to operate effectively.
All of these factors made it an easy decision to select the peristaltic anti-foam injection pump for this application. As the pump was also being mounted on a skid, so we knew space was of great importance. We also incorporated a herringbone gearbox into the design which enabled the motor to be mounted vertically – saving more space.
If you have a chemical transfer application requiring the transfer of hazardous or flammable liquids and aren’t sure which pump to specify, speak to North Ridge Pumps to see how we can help.
For more information on ATEX Antifoam Transfer Pump talk to North Ridge Pumps Ltd