
Sign In
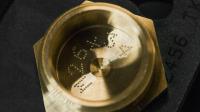
Traceability procedure for manufacturing, at its most basic, is ensuring that products produced can be easily traced back to their source. Products should be tracked from procurement of raw materials, through to production, consumption and disposal.
What is traceability?
The International Standards Organisation (ISO) [1] has defined traceability in ISO 9001 as: ‘the ability to trace the history, application, use and location of an item or its characteristics through recorded identification data.’
To achieve this standard, you must meet certain criteria. You must:
• Establish the identity and status of products.
• Maintain the identity and status of products.
• Maintain records of serial or batch numbers.
Traceability procedures are vital for not just internal purposes, but also benefit end retailers, customers and recyclers. The ability to track a product back to the source provides peace of mind and vital information.
It also ensures companies can respond quickly should things go awry. With a simple, comprehensive traceability procedure, the impact of product recalls can be minimised as all shipped stock can be easily traced to determine if it has been affected. With more laws to protect consumers coming into force internationally, product recalls are becoming more common.
There are various common traceability procedures, but the two main methods are chain traceability and internal traceability. While similar, both methods provide comprehensive traceability in different areas.
Chain traceability
This is the general term used when referring to external traceability, and is generally what people mean when they refer to the process of traceability. Essentially, this means that the entire history of the product can be traced from the procurement of raw materials to the end of its life. Manufacturers can trace forward to where their products have been delivered, and consumers and those downstream can trace backwards.
The manufacturing of a product can be made up of several parts, with the item moving through many different manufacturers. As such, it is vital that it is clearly identifiable and traceable through each part of the process.
Internal traceability
As the name suggests, this procedure allows the monitoring and tracking of parts and products within a specific section of the total supply chain. This is usually defined as a single company or processing department.
For example, an internal traceability procedure would track the item from arrival as raw materials, through the manufacturing or machining of the parts, to shipment. This is usually achieved with the assignment of an identification number, with relevant information linked to this number accessible to those who need it.
Why do we need traceability procedures?
In the complex world of manufacturing, it is not just beneficial for everyone involved to know the history of a product, but vital.
Should the worst happen and a company is forced to issue a product recall, an easily identifiable traceability procedure will allow for swift action. This is important for maintaining consumer trust in your brand. Theoretically, a faulty product could even be traced back to a faulty machine allowing it to be removed from service quickly.
What’s more, traceability can vastly improve the speed and quality of your processes. In the competitive world of modern manufacturing, the ability to cut cost and reduce waste can be the key to survival.
What’s more, consumers can have peace of mind knowing their product has followed a comprehensive, structured and observable production process.
How do companies implement traceability?
An effective traceability procedure for manufacturing will consist of a clear identification system, with information recorded and accessible. Many industries will have a standard identification number format that can be followed to ensure uniformity.
Alternatively, for internal traceability, you might implement your own specific identification method. Either way, it is vital that identifying markers such as numbers are clear and visible throughout the entire process.
Common methods of identifying products for traceability include:
• Marking crates and delivery containers using branding irons or stencils.
• RFID (radio frequency identification tags).
• Standard 2D or 3D barcodes. These can be printed directly onto packaging or attached via labels.
These methods all come with pros and cons, with the main issue being lack of permanence. One of the most reliable methods of ensuring identification numbers are visible to everyone in the process is by permanently marking them on the part or product itself. The most common methods for achieving this are laser marking or physical indentation.
There are various types of laser marking which will depend on a variety of factors such as manufacturing type. Laser marking is usually preferred when working with very thin metal or plastic, as the laser will not cut deeper than 0.001”.
Physical indentation, such as with the dot peen method, is considered more permanent as the cut is usually deeper. The dot peen method creates small, permanent indents in the surface of the product, and is one of the oldest and most reliable forms of permanent marking in the manufacturing industry.
Reliable traceability procedures are a vital part of modern day manufacturing that should not be overlooked.
NCB Marking offers a range of marking machines to suit almost any type of manufacturing set up, allowing you to implement a comprehensive traceability procedure. For more information about any of our marking products, or to discuss a bespoke solution for your marking needs, call us on 01531 640400 or visit our contact page.
For more information on What are manufacturing traceability procedures? talk to NCB Marking Equipment Ltd
Enquire Now
List your company on FindTheNeedle.