
Sign In
DIE CASTING VS MACHINING
13-03-2017
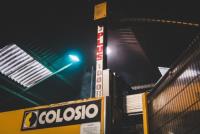
For the average person on the street, die casting is how Matchbox cars and most toys from the 1980’s were made. Very few realise just how many components, tools and objects in our everyday lives are made from some form of casting process.
Cast your eye over your home and you’ll see taps, door handles, light fittings, computer components, car components, furniture components. Even components in sewing machines and cameras are all produced using die casting.
However, why is casting chosen over machining?
Quite simply, it comes down to cost.
If you are machining a complex geometry from a solid billet of aluminium then you have to remove a lot of material, and that takes time, and creates a lot of wasted material.
Diecasting is a near-net-shape process, so if you are diecasting rather than machining, then you only use the material needed, the process is fast and repeatable, and any post-casting machining will be only to add in tightly toleranced features or other finishing details so will take a fraction of the time of machining from solid.
The result? Lower unit cost.
There are other positive benefits too. The faster cycle time significantly reduces the lead time for large batch production.
And because the modern diecasting process is so controlled and repeatable, it has great quality benefits. Even the most demanding industries such as medical devices, aerospace, and precision instrumentation now trust diecasting to produce critical components.
Our diecastings can be found in life-support machines, motion capture equipment, armoured fighting vehicles and airline interiors.
With an ever growing trend in all industries to light-weight products, casting is even more relevant today.
Where lightening a machined component involves additional machining cost to remove material, for example creating pockets and recesses in heavy sections, the same design feature on a casting usually removes cost, as there is less material consumed, and the geometry of the lightening features are created within the standard casting cycle.
It’s a win-win.
There is still a valuable role for machining for low volume production, as diecasting tooling is expensive, so the unit cost savings don’t justify that investment until you get up to reasonable volumes, but with advances in tooling manufacturing, that breakeven threshold is coming down all the time. So if you are designing a new component and you’re not sure whether to follow a casting or a machining route, then get in touch with MRT’s technical team for some no-strings advice.
If you are currently sourcing machined components and you think that your volumes may justify investing in diecasting tooling and you want to know how quickly it will pay back, then we would be happy to provide you a quotation.
MRT Castings has 70 years of experience in gravity and pressure die casting working in the aerospace, defence, energy, health, infrastructure and media industries.
As the recipient of the Queens Award for Innovation: International Trade, 2016, we are ideally suited to support clients around the world with projects requiring highly technical cast components.
Contact us today to discuss your needs.
For more information on DIE CASTING VS MACHINING talk to MRT Castings Ltd
Enquire Now
List your company on FindTheNeedle.