
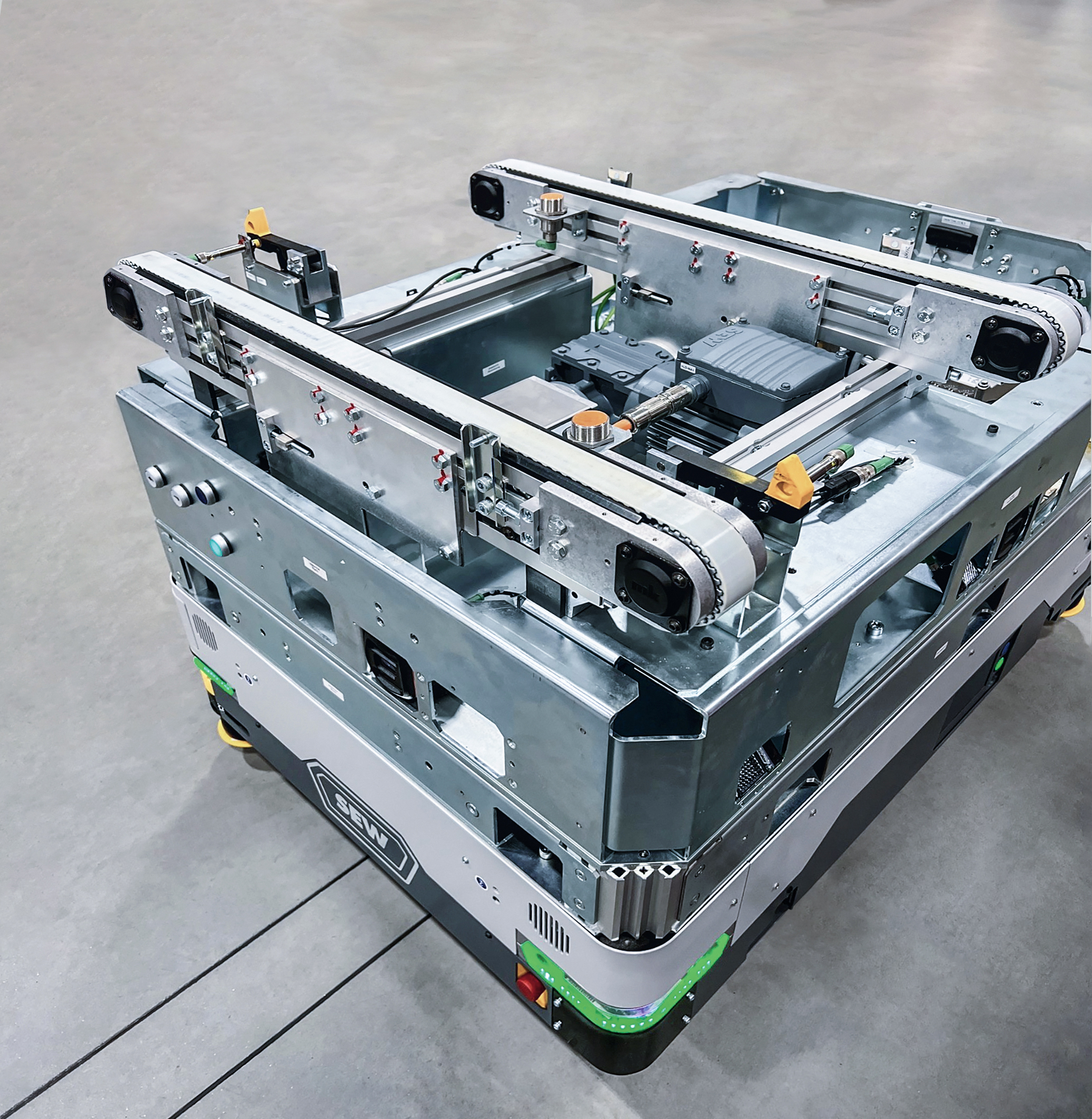
SEW-EURODRIVE has established efficient and flexible processes to achieve its vision for Industry 4.0. SEW’s new design for automated guided vehicles at its main U.S. location includes integrated timing belt conveyors from mk. These vehicles serve as mobile workbenches for mounting individual gearboxes.
Classic interlinked conveyor technology is the most efficient way to automate processes in mass production. In customised production, however, the requirements are ever-changing – with “lot size one” being the key word. This is where the flexibility of automated guided vehicles can be put to good use.
At its American headquarters in Lyman, South Carolina, SEW-EURODRIVE has built a flexible production facility that is optimised for precisely such custom production – where classic conveyor technology is combined with flexible workstations. The autonomous vehicles drive through the hall independently, picking up pre-assembled gearboxes from a belt conveyor and taking them to the workers, who can then continue mounting them on the vehicle itself as if they were at a mobile workbench. The vehicle then travels to the next station and transfers the gearbox back to a belt conveyor. It is thus possible to mount individual gearboxes, with efficient and flexible processes.
Through its “MAXOLUTION System Solutions” business segment, SEW offers scalable and future-proof system solutions in the field of mobile and rail-guided conveyor technology. As an overall solution supplier for automated guided vehicle systems, it focuses not only on the vehicles themselves but also on all the services associated with them, from system planning to commissioning and servicing. The vehicles and system components are produced at SEW-EURODRIVE’s headquarters in Bruchsal, Germany. Alongside SEW’s world-renowned modular system for gearmotors and electronic products, it also engineers autonomous vehicles based on an innovative modular technology and software system. This system makes it possible to configure individual vehicles while keeping complexity low.
Timing belt conveyor from mk makes the ideal load handling device
To autonomously pick up and then set down the gearmotors with a belt conveyor, the vehicles need an appropriately powered load handling device. “We had initially considered a chain conveyor that we could integrate into our vehicles,” says Aaron Bronner. However, working with the conveyor technology experts at the mk Technology Group (mk), the team found a better solution. “We decided on a dual-line
timing belt conveyor instead of a chain conveyor,” says Ulrich Klein, one of the field representatives at mk who assisted with the project. A timing belt conveyor is more economical and requires less maintenance than the chain conveyor in the original plan. Furthermore, the timing belt has a higher contact area than the chain. That also provides greater stability for the product on the vehicle, even when navigating sharp corners or making abrupt (emergency) stops. The ZRF-P 2010 timing belt conveyor from mk was the ideal solution for the project: it can safely carry the maximum load of 160 kg, and the drive variants available also allow for reverse operation (in both directions).
Because mk uses SEW drive technology as standard, integrating the drive was not a problem. The experts at MAXOLUTION programmed the controller and coordinated it with the overall system.
To find more contact mk Profile Systems on (01949) 823751, email info@mkprofiles.co.uk or visit www.mkprofiles.co.uk
For more information on Timing Belt Conveyor From mk serves as Load Handling Device talk to mk Profile Systems Ltd