
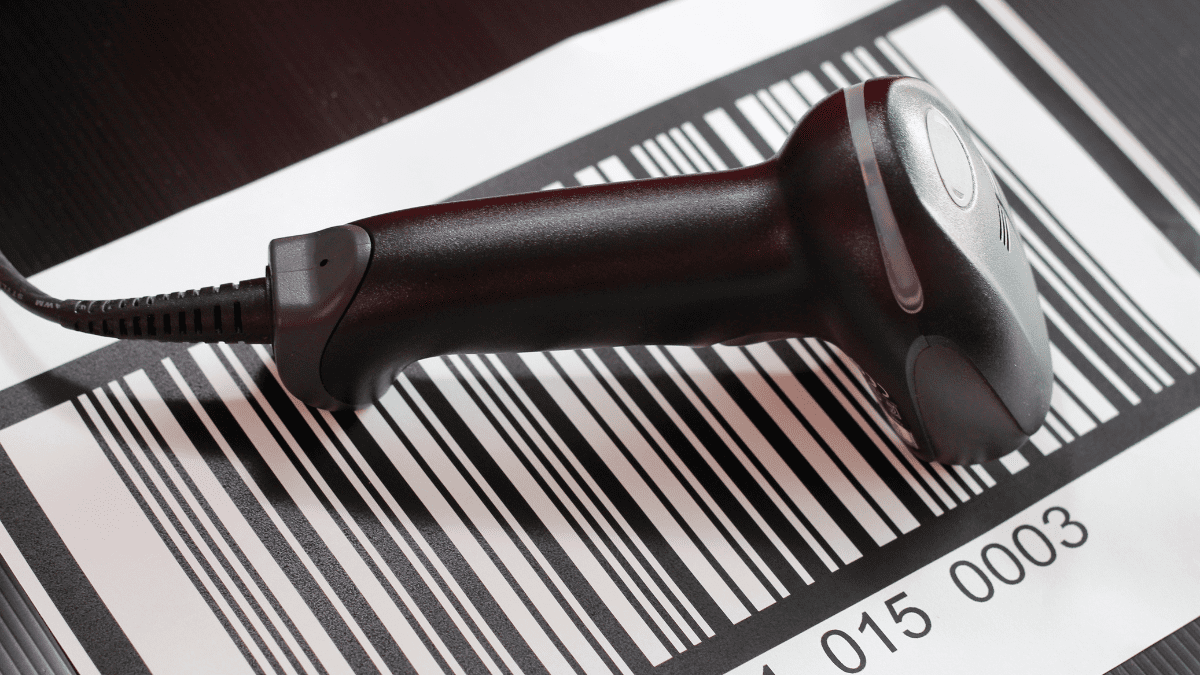
Do you know, in detail, your supply chain process?
The process a product or component product has been through, part of, or supported at any stage in the supply chain?
Are you confident you have met all supply chain compliance regulations to the highest standards? How can you check?
How confident are you that you’re using the correct parts at the final stages of production?
Today, global supply chains are not uncommon. Offering manufacturers numerous options and opportunities, technology and the introduction of automation has enabled the manufacturing industry to grow and diversify like never before.
This, matched with increased customer demand and robust requirements for stringent health and safety procedures, has led to a sharp rise and more regulation surrounding the need for manufacturers to have full traceability leading to accountability across all areas.
Ultimately, you must be able to have traceability of parts for batch manufacture to ensure that the correct parts are brought together for final assembly.
This is where automation and barcoding come into effect – ensuring flawless production and increased productivity, as well as an uninterrupted supply chain.
Ensuring supply chain compliance….
…Just what is traceability?
Traceability enables manufacturers to track and trace the movement of parts throughout the supply chain.
Tracking every stage of the production process, good traceability systems will allow you to track every element of your product, from the raw material to the finished goods – vital for ensuring quality, consistency, and compliance.
To meet traceability compliance:
- Look to include serial numbers
- Include track and trace in production procedures
- Request verification of product movement, quality checks, etc.
- Provide robust reporting to regulatory bodies when required.
Barcodes, much loved and underused
An efficient and effective way to manage your supply chain is to ensure data is always available, understandable, and, most importantly, accurate.
Barcoding helps to provide all of this while also reducing risk.
Providing you with full tracking and monitoring information of individual parts, barcodes allow you to track location and provide information on what tools and machines the process uses, what quality checks are being carried out, and more.
Tracking every single phase of the production process, every batch of product components can have barcodes assigned to them, which, when scanned, can provide detailed information, including production dates, expiration dates, warehouse location, supplier details, etc.
Helping to maintain uniformity, barcoding also helps to ensure consistency, identifying issues of non-conformity or defects in products early on in the process and throughout the entire supply chain.
Yet, due to the pressures placed on manufacturing processes and the need for speed, barcodes are very much an underused commodity.
Importance of barcoding in manufacturing
Batch tracing helps to reduce risk, avoid defects and problems with products, and keep your supply chain moving.
Barcoding in manufacturing:
Can provide critical data and an audit trail of products and product components. This means when an issue arises or you suspect something, the information provided by the barcode itself can help you to determine which action in the production line is the root cause.
Allows you to meet traceability standards, preventing you from receiving hefty legal penalties resulting in fines. These standards are also a basic requirement in contracts highlighting the requirement to meet industry regulations.
Stops defective products entering the market. This is extremely important in manufacturing, allowing for easier product recalls when a defect is detected within a batch, avoiding damage to your reputation and other products.
Offers robust inventory management, increasing efficiency, minimising waste, and providing further opportunities for growth as you have an increased line of visibility within your production processes.
With the right automation systems, you can efficiently manage your supply chain and avoid the most common manufacturing issues while maintaining full compliance.
Benefits of barcoding
- Keeps you compliant
- Allows you to retrieve information quickly
- Increases security, making products remain safe for use
- It lets you track products during specific time frames
- Protects your brand and reputation
- You can respond quickly to problems as you identify `lots` in real-time
- Ability to find and analyse the root cause
- Facilitates continuous improvement – can identify issues in the production line and identify where parts can be automated to reduce these errors
- It improves quality, reduces waste, and saves money.
Contain and control
At Innomech, we know that you must be able to account for the movement of materials throughout the entire manufacturing process, and we understand that you don’t want anything to affect these processes resulting in faulty end products.
That’s why we analyse, design, and implement small- and large-scale automation solutions you can trust.
Designing, developing, and producing innovative special-purpose automation machines for the manufacturing industry to improve productivity, profitability, and supply chain compliance.
We ensure full component traceability by providing complete build documentation that complies with our quality systems.
Call +44 1353 667394 or contact us via info@innomechgroup.co.uk today to find out more.
For more information on How to Avoid Manufacturing Issues by Ensuring Supply Chain Compliance talk to GB Innomech Ltd