
Sign In
How to get started with robots and cobots
08-06-2022
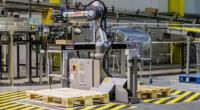
Robots and cobots are now becoming our new work colleagues and a valuable source of production innovation – the continual shift from expensive machinery to something that we see more and more highlights this point.
Often these robots work outside of the production environment and are a strategic asset when staying competitive. They have multiple uses such as handling, welding, assembly, packaging, and palletization, to name a few. Robots can also be valuable helpers when dealing with dangerous and highly repetitive tasks. One thing is for sure; they are a strategic asset that can help improve production line efficiency and reliability and help you stay competitive in the future. For this reason, 2021 saw a record number of three million industrial robots being used in factories around the world (Source: The rise of robots).
The operational stock of industrial robots has tripled over the past decade, a trend dominated by progressive market developments in China and is continually pushing the boundaries further. Unsurprisingly, Asia leads the way in automated processes (according to the IFR). China’s level of automation is almost double that of the global average, with plans to double the number of industrial robots by 2025 (Source: thetimeshub.in).
Robotics and the future of production and work
Robots are essential tools for increasing productivity today. Today, most robots are used in production, performing tasks more efficiently and reliably than humans. However, with continued innovation, robots are being used in other sectors, from agriculture to logistics to hospitality. Robots are getting cheaper, becoming more flexible, and more autonomous. Some robots substitute human workers; others – collaborative robots, or ‘cobots,’ which work alongside workers complement them. As this trend continues, robot use will likely be a key factor in productivity growth and will potentially reshape global supply chains.
The adoption of robots across various industries, including manufacturing, healthcare, defense and security, logistics, inspection and maintenance, automotive, electronics, and food and beverage, has accelerated the market. With advantages such as cost reduction, improved quality, increased production, and improved workplace health and safety, the demand for robotics is anticipated to grow exponentially. Robots deliver better quality products and services more efficiently, with less wastage, and without causing physical injury to humans due to their autonomous nature.
High-tech solutions are in constant demand in all industries, especially where there is a need to achieve better performance and reliability. In 2020, handling, welding, and assembling were the most common application uses for robotics, signaling their use in many businesses, both large and small.
Finding the right business case is key
Industrial Robots can integrate with standard conveyor systems that are easy to use, compact, and mobile. This type of integration allows the smaller industrial players to profit from the benefits of automation without such significant outlay costs. Companies utilize robots as a complete turn-key solution that integrates supplier partners’ robots with world-leading conveyor systems.
Looking for where to start with replacing your labor-intensive production processes? Here are some examples to begin with straight away:
Material feeding at the beginning of a line – Used at the beginning of the production line, the material feeder picks products out of their stationary position and places them directly onto the conveyor or in the packaging machine. This eliminates the need to manually unload products at the beginning of the production process.
Case packing in the middle of a line – The case packer takes finished products from the middle of the production line and places them into a box to continue on the same line, divert onto a different line or move to palletizing. The option to integrate the case packer directly into the production line increases production line capacity by creating space within the facility. Where operators traditionally stand next to a line to pack cases manually, the combined robot integrates with the line, reducing the amount of space used while achieving results.
Palletizing at the end of a line – Designed to palletize with consistent quality and precision, FlexLink offers two options suitable for palletizing closed boxes within fast-moving consumer goods industries: we offer palletizers with industrial robots, such as the RI20, and the RC10 collaborative robot that deliver fast return on investments.
FlexLink has extensive experience in advanced production logistics and tailor-made systems for line automation.
To understand more about our Industrial Robotic solutions and our innovative, automated solutions to produce goods smarter, safer, and at lower operating costs, visit our website or contact us if you would like to discuss more regarding your future robotic needs.
For more information on How to get started with robots and cobots talk to FlexLink Systems Ltd
Enquire Now
List your company on FindTheNeedle.