
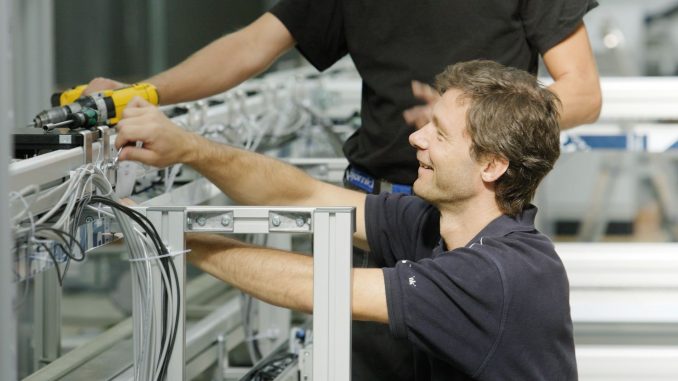
When was the most recent occasion you had your production line assessed to ensure its safety, functionality, and environmental compliance? By consistently conducting preventive maintenance, you can enjoy many advantages, from improving production efficiency to reducing downtime. With the summer season upon us, it’s the perfect time to guarantee a smooth production process. This blog article will explain the importance of maintaining your production lines proactively. Keep reading to discover valuable tips and tricks for preventing unexpected breakdowns using a helpful checklist for preventive maintenance.
Elevating efficiency and reliability: the significance of preventive maintenance
To begin with, let’s clarify the concept of preventive maintenance. Preventive maintenance refers to a carefully scheduled and systematic approach to inspecting and maintaining existing equipment to prevent errors or breakdowns. In the context of production lines, this typically includes machinery, conveyors, robots, and automation systems. By proactively addressing potential issues, businesses can ensure smoother operations and minimize unexpected disruptions.
Proactive care for optimal performance
You might believe that the need for maintenance decreases as the level of robotics and automation increases in production. While this notion holds some truth, preventive maintenance remains essential for the early detection of misalignments. Ideally, issues can be identified and addressed before defects or deviations occur in your production lines. Keeping your equipment in optimal condition increases the likelihood of avoiding unexpected breakdowns and subsequent consequences.
Ignoring preventive maintenance can lead to negative consequences
An unexpected breakdown can cause significant economic losses and damages to your entire production. When equipment is not aligned correctly, the quality of the handling of products is lowered, putting them at risk of damage during transportation on the production line. Product damage is both time-consuming and impacts production efficiency and profitability. Failure to meet production targets due to product damage may result in rescheduled batches, late deliveries, and unmet customer demands. In the worst case, it can lead to unhappy customers, brand damage, and lost sales. Moreover, discarded scrap can have adverse environmental impacts.

The advantages of preventive maintenance for production lines
To sum it up, as a production manager you have a lot to win by carrying out preventive maintenance:
- Optimized production flows
- Minimized risk for unplanned stops
- Improved line availability
- Increased likelihood of reaching a higher Overall Equipment Effectiveness (OEE) / throughput
- Less wearing of equipment
- Reduced cost, product damage, and noise levels
- Minimized risk of negative impact on the environment due to discarded scrap
- Safer production
- Safer working environment for staff – the list goes on!
Checklist for carrying out preventive maintenance correctly
As a production manager, you are responsible for running your production as smoothly and efficiently as possible. Of course, the more experience with mechanical and project-related issues you and your operators have, the more likely you are to conduct inspections correctly and address potential problems. To help you further and ease the multiple steps of preventive maintenance, we have compiled a checklist with a few tips and tricks that might be helpful when inspecting your conveyor systems.
- Start off by examining visible surfaces and components. Are the conveyor belts and chains intact? Can you see any damage to slide rails, guides, shafts, bearings, sprockets, brackets, or side guards? Changing slide rails in time prevents damage on profiles and chains, reduces friction, minimizes tensile force and stick-slip, and reduces noise levels. Furthermore, changing chains in time prevents the chains from breaking, lowers friction, and minimizes tensile force and running noise. Changing guides in time protects the hooks in the return chains and reduces rattle. Make sure to address potential damages and replace worn-out components wherever necessary.
- Do the conveyor belts maintain their desired paths? Conveyor belts that are not correctly cut and joined, sometimes when delivered from the factory, may result in miss-tracking. Conveyor belts should always be centered on the conveyor bed in the middle of the rollers. Make sure conveyor beds are not out of level or square. Also, check and adjust rollers so that they are parallel to each other and perpendicular to the belt.
- Are the conveyor belts running properly with products? A conveyor belt can run perfectly fine without products, but once the products, especially heavy-weight ones, are placed on the conveyor belt, it can move sideways. If the conveyor belt skids against a fixed point, heat from friction may occur and, worst case, the conveyor belt starts melting (if made of plastic materials). Therefore, constantly adjust the conveyor belts both with and without products.
- Are the conveyor belts and chains clean? Cleanliness is always crucial, but some conveyor belts are more sensitive to hygiene than others, especially belts transporting food. It is essential to sanitize the chains and belts and all components that regularly get in contact with the products. This will prevent bacteria from accumulating in possible irregularities and cracks. Dirt and pollutants entering belts can lead to contamination of the products. By cleaning belts, chains, and components in time, it is possible to avoid contamination and minimize undesired friction and stick-slip. Hence, check for any damages and make sure your conveyor is flawless and clean.
How often should I inspect of my production lines?
The optimum time intervals of line inspections depend on several factors, such as application, production environment, the type of products being transported on the conveyors, the stress on the conveyors, repeatability of machines and components, and how often your production lines are running. Some products require extreme production environments (such as extremely high or low temperatures), are extremely heavy (such as automotive products), or contain hazardous chemicals. Consequently, these put particular demands on the production lines and the frequency of inspections.
Technology providing info about conveyor status and wear indications
As concluded, in a flow-based production facility, any downtime of any step in the process will disrupt the entire fulfillment engine of your production flow. Therefore, your conveyor lines need to be geared for preventive maintenance. Technology that provides information about conveyor status and wear indications can help you reduce unplanned downtime. The ability to monitor the overall flow of a facility in real-time is a powerful tool for efficiency and uptime.
Click below to download the checklist:
—
Make life easy
Of course, FlexLink can help you optimize your production flows. Materials, design, wear and operator convenience are key factors in our product development, maximizing the uptime of our systems. We are also developing new features for predictive maintenance that will reduce unexpected downtime even further.
We carry out preventive maintenance as well as service inspections. Or do you have your own maintenance personnel? We offer training programs that are both practical as well as theoretical. We can visit your production site and hold the training close to your installations, or we can offer training at your local FlexLink office – you decide!
Would you like to perform preventive maintenance in the summer months? Get in contact with our experts now! We look forward to hearing from you. For more info, visit our website or follow us on LinkedIn to get regular insights on industrial automation and production efficiency.
For more information on Boost efficiency and reduce downtime: the power of preventive maintenance talk to FlexLink Systems Ltd