
Sign In
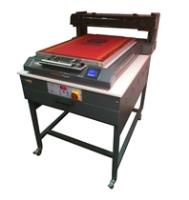
William Shorter, Product Manager of CPS – Chemical Products and Services, reflects back to Printwear and Promotion Live held in February of this year, where an unprecedented increase was reported in sales of digital stencil making equipment. Here William shares his tips and facts on managing this shift change from conventional to digital stencil making.
Digital stencil making systems have been around since the 1980’s and are not necessarily a new phenomenon. However, it was clear that there was a definite shift in buying choices at this year’s show, with particular interest in Direct to Screen (DTS) and Computer to Screen (CTS) systems.
So what exactly are DTS and CTS systems? In a nutshell, DTS utilises direct imaging of a positive mask onto a coated emulsion or capillary film. The mask is created using either water based inks or wax and in some cases they can also use integrated exposure systems with LED light sources. CTS systems on the other hand utilise LED focused lights to directly image the stencil without the need of a mask positive.
Conventional screen making is widespread and well understood but how relevant are current screen making methods and products for digital stencil making? Let’s take a look.
Stencil Systems:
In 99% of cases, you can continue to use your trusted stencil system (Diazo, Dual Cure or Photopolymer Emulsion) that you are using today. These will work on all DTS and CTS systems and should continue to offer you the print durability that you have today.
Exposure:
There is a lot of speculation and marketing around stencil systems that are “optimised” to LED and CTS exposure systems. However, if you ask the equipment manufacturers, you will actually find that they have been developed for functional performance with nearly all stencil systems. They may even be able to set up the CTS equipment to match the UV absorption peak of the stencil system that you are using today. Of course, there are advantages in using photopolymer emulsions that are related to speed of processing, but this is equally applicable for conventional exposure and not unique to DTS/CTS.
#ScreenprintingTopTip for exposure:
- The use of white mesh with CTS equipment can improve the through-cure of the emulsion and the durability of the stencil system on-press.
- Photopolymer emulsions benefit from post exposure hardening to improve durability on-press.
Coating:
Did you know that the principles for coating your emulsions will stay the same? Just remember to keep the build of your emulsion on the print side and follow the emulsion manufacturers’ recommended guidelines. Lower Rz stencil systems with a smooth, flat surface will image better on DTS than those with high Rz values, therefore you might want to avoid 1+1 coatings with low solid emulsions.
Drying:
If you’re already experiencing problems related to breakdown on-press and you’re not using dedicated drying equipment then investment in a good dryer along with your DTS and CTS equipment would be worthwhile. Good drying is particularly important when you are looking to achieve long print runs with water based or aggressive ink types.
#ScreenprintingTopTip for drying:
- Avoid drying coated screens along with wet screens from the washout or reclaim process. This will stop a build-up of moisture in the drying cabinet and improve the printing and durability properties of your emulsion.
- If your exposed screen has residual moisture in the system, the diazo will react preferentially with the water molecules rather than with polymer. This means that even if you have given the screen a full exposure (that is you have used up all the Diazo sensitiser) a large proportion of the Diazo will have reacted with water.
The result is a softer stencil which will break down. This is why in the summer months when the humidity increases in certain areas of the world, screen printers experience more screens breaking down during printing. If the screen is not dried thoroughly before it is exposed, then it will not be as tough as it should be.
- Screens with residual moisture will readily absorb water based inks used in DTS and this will impact on the fine detail that can be achieved.
In conclusion, the move to digital screen making can, in most cases, be made using current emulsions and techniques. As with any new piece of equipment you must make sure that it will meet production needs in terms of quality, throughput and reliability. There will be training needs for staff so you need to ensure that software is easy to use and with good support. If you have questions about suitability of current stencil emulsions ask the manufacturer or supplier. They are the experts and can guide you to make the right choices.
This 'How To Screen Print' guide was originally printed on page 78 of the September 2016 edition of Printwear & Promotion.
Images courtesy of Exile Technologies and Natgraph
Please feel free to share this 'How To Screen Print' guide with your friends, on blogs and via social media.
If you have any excellent screen printing hints and tips, please share them in the 'Screen Printers Of The World Unite Community' on Google+ or contact us via technical@cps.eu and maybe we can feature them in a new guide.
For more information on The step change from conventional to digital stencil making doesn’t have to be that big. talk to CPS - Chemical Products and Services
Enquire Now
More related to The step change from conventional to digital stencil making doesn’t have to be that big.
List your company on FindTheNeedle.