
Sign In
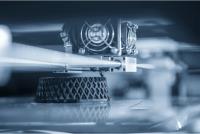
As additive manufacturing methods start to utilise more metallic materials, how will this impact the future of the aerospace industry?
The aerospace industry is known for its innovation. It often leads the way with future tech, and 3D printing is certainly no exception. Additive manufacturing has been part of the aerospace sector for a little while now, and it’s a trend that‘s expected to continue.
A 2018 report predicted the 3D printing market for the aerospace and defence sector would be worth $4.76 billion by 2023. And in the more recent 3D Printing in Aerospace and Defense Market report, the industry is estimated to register a CAGR (Compound Annual Growth Rate) of over 20% during the forecast period (2019-2024).
In Jabil’s Aerospace and Defense Manufacturing Trends survey, 70% of respondents think that 3D printing has already changed the way the industry thinks and operates.
The same survey also identified the main uses of additive manufacturing technologies within aerospace. Prototyping is the main end use, used by around three quarters of respondents. This is followed by repair and maintenance, research and development, and production parts.
One of the biggest changes in 3D printing in recent times comes in a renewed focus on the materials being used. Until now, most additive manufacturing procedures have used plastics. However, the industry is seeing a huge growth in the use of metallic materials.
Move to metals
The uses of metal 3D printing in aerospace could be a game changer. In the Jabil survey referenced above, almost nine in ten respondents said they expect their 3D printing use to double over the next few years.
A global forecast into the 3D printing filament market identified the metals segment as the projected fastest growing type between 2020 and 2025. Metallic materials can be used for printing complex structures for prototyping and manufacturing components.
The report also showed the aerospace and defence sector is leading consumption in the 3D filament printing market. This is mainly down to the need to produce intricate but lightweight components. Existing and potential end-use applications include jet wings, engine parts and rocket parts. NASA intents to metal 3D print over 80% of its future rocket engines (source).
Rapid prototyping is another area in which the aerospace industry is already, and is projected to continue, using metal 3D printing.
The benefits of metal 3D printing in aerospace manufacturing
The aerospace industry will hugely benefit from the continuing uptake of additive manufacturing, particularly with the growing use of metals in the process. The key benefits of 3D printing are well suited to the industry.
For a start, previously complex parts can be simplified into one precisely printed component, rather than put together from multiple individual components. Not only does this save on time and material costs, there are also less possible points at which something can go wrong. It also means parts can be made to demand, as and when they are needed. On-demand marketing speeds up production cycles for overall increased productivity.
Here at Corrotherm we’ll be watching the development of 3D printing in the coming months and years, especially when it comes to the use of metallic materials. Keep an eye on our blog for the latest stories.
For more information on The future of metal 3D printing for aerospace manufacturing talk to Corrotherm International Ltd
Enquire Now
List your company on FindTheNeedle.