
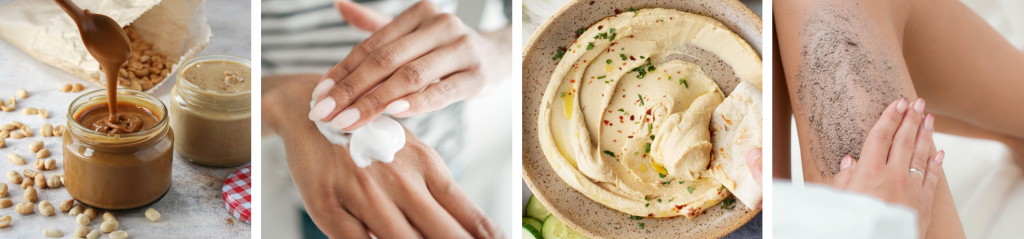
Whether you’re producing adhesives, pastes, or sauces, ensuring quality and consistency is paramount. To provide you with the best guidance, we’ve enlisted the expertise of Dean Willis, Production Expert & Sales Director at Adelphi, who has amassed over 30 years of industry experience. In this article, Dean shares his 5 Top Tips for optimising your manufacturing process for thick, high viscosity products, using insights gained from valued customers.
Ask us about recommendations for mixing or filling thick products today >>>
High Viscosity Products Include…
Nut Butters, Dermatological Creams, Chutneys and Relishes, Body Butters, Hummus, Thick Sauces, Body Scrubs, and more.
1. Invest in High-Quality Equipment Which is Fit for Purpose:
When dealing with high-viscosity materials, selecting the right equipment first time is crucial. Dean recommends investing in robust mixers, pumps and filling equipment which has been proven to work with thick substances. Cheaper options are likely to be a false economy in the long run.
When looking to buy new equipment, ask potential suppliers to provide case studies of their equipment working with similar products to yours. Even better would be conducting a demonstration on their equipment, using your product. Some suppliers will even be able to take you to see the equipment in-action at another customers’ site.
Quality equipment not only ensures smooth production, but also minimises wear and tear, reducing downtime and maintenance costs.
Ask us about recommendations for mixing or filling thick products today >>>
2. Optimise Your Mixing Techniques:
Proper mixing is the key to achieving uniform viscosity and product quality. This means that your customers will always have a great experience of your product. Inconsistent mixing could mean that some batches are different thicknesses or lumpy, which could stop your customers from repeat purchasing.
Consider using techniques like shear mixing, which applies force to break down particle agglomerations, and high-shear mixing, which involves high-speed rotation to disperse materials evenly. Your mixing equipment supplier will be able to recommend the ideal type of mixing to best suit your product.
Experiment with mixing speeds and durations to find the optimal parameters for your specific product.
3. Maintain Consistent Temperatures:
Viscosity is highly temperature-dependent, and thicker products often mix or fill better when heated. Maintaining consistent temperatures throughout the stages of your manufacturing process is crucial for controlling the flow properties of your product. For example, water-jacketed mixing vessels use hot water flowing around the vessel ‘jacket’ to regulate temperatures during mixing. Ideally, finding one single supplier who can offer both mixing and filling equipment can ensure a smoother production process. For example, Adelphi’s Response Benchtop Filler can be supplied with a water jacketed hopper where the product waits to be filled.
Real-time temperature monitoring and control mechanisms can prevent overheating or cooling, ensuring the product maintains its desired viscosity.
4. Implement Quality Control Measures:
Establish rigorous quality control protocols to monitor viscosity, texture, and other relevant parameters at various stages of production. Utilise viscometers and rheometers to measure viscosity accurately. Implement in-process testing to detect inconsistencies early, allowing for immediate adjustments. Regularly calibrate your measurement instruments to maintain accuracy. Document and analyse quality data to identify patterns and optimise the manufacturing process continuously.
5. Focus on Safety and Cleanliness:
Thick, high-viscosity materials can be challenging to handle and clean. Prioritise safety by providing employees with proper training and personal protective equipment (PPE). Implement safety protocols to prevent accidents and spills. Additionally, design your equipment and production layout with easy cleaning in mind. Use materials that resist sticking and are easy to clean, such as stainless steel.
Regularly schedule equipment cleaning and maintenance to prevent product contamination and ensure the longevity of your machinery. Ask potential filling machinery suppliers how long it takes to strip and clean their equipment, as any time spent not filling represents lost revenue potential for your business. For example, purchasing a machine which has a longer strip and clean time would be less cost-effective in the long run.
For more in-depth information and real-world examples, you can read about the experience of a UK nut butter manufacturer here.
Alternatively, to see examples of successful thick product filling in-action, please use the links below:
➤Watch a Peanut Butter filling video here >>>
➤Watch a Body Scrub filling video here >>>
By following these tips, you can streamline your manufacturing process, enhance product quality, and ensure the efficient production of thick, high-viscosity products. Remember, continuous monitoring, employee training, and process optimisation are keys to success in the manufacturing industry. Count on Dean’s extensive experience and Adelphi’s range of solutions to support your manufacturing endeavours.
Adelphi – By your side for over 75 years
For any questions or enquiries about this article,
Please contact:
Dean Willis – International Sales Manager
+44 (0) 7384 892641
For more information on 5 Top Tips for Manufacturing THICK High Viscosity Products talk to Adelphi Group of Companies