
Sign In
MHDE Driven by Precision
03-02-2022
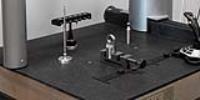
MH Development Engineering (MHDE) was formed in 2014 by Matt Hill and Amy Taylor (two former Formula 1 race team employees), with the intention of offering superior R&D design services, whilst outsourcing the manufacturing process.
This soon became a sticking point as suppliers began to miss deadlines, prompting a decision to offer in-house manufacturing - the goal to not promote themselves as a manufacturer, but as a full-service provider, one specialising in the precision engineering of high-quality bespoke systems.
MHDE began to invest in cutting-edge CNC machining and turning centres, enabling the company to take on projects with requirements for design, manufacture, assembly, and installation - complete turnkey solutions. Additionally, the investment in equipment meant the company could also adapt to handle reverse engineering projects. Such is the company's unique and dynamic approach to R&D, that in late 2019, MHDE were the recipients of an Innovation award at the Cherwell Business awards.
Years of continued growth have found MHDE relocate to bigger premises more than once, recently moving into a purpose-built factory which now houses the company's modern, fully equipped workshop and offices.
MHDE work on a range of diverse, one-off low volume projects, including electric vehicle technologies and systems, military equipment, and super yacht hardware. However, the projects that continually allow the company to excel are R&D systems; assisting F1 teams to develop a specific area, this could be suspension components or aerodynamic features. Starting from concept through to testing - the forte is very much solutions to increase performance or reliability of the car.
Matt explains how the company got started: "When we stepped away from F1, we still had connections within the sport and so making them aware of our newly established service meant that we had projects to work on from day one."
For anyone working within motorsport, perhaps the biggest challenge is the deadline. Typically, race days do not move so deadlines must be adhered to, no matter what.
Matt continues: "It is an interesting dynamic, having worked in a team and now as a supplier, it affords us insight into exactly what they need us to make happen. We might get called up in the afternoon and be asked if we can supply a component the next day. We work long hours and long weeks, but we will never miss a deadline. The very reason we get so much repeat work is because we do deliver quality on time. This does mean that we must be very reactive, so much so, that we've never bought machinery to fill capacity because if we did, we wouldn't be able react to a new project straight away."
With the move into their first factory, MHDE very quickly realised that investment was needed in measuring equipment. Customers began approaching the company to undertake reverse engineering and manufacturing of other parts, not just complete assembled systems, and they were unable to prove that the parts were made exactly to drawing.
Matt explains: "We began to look at the CMMs that were available on the market and had demos with three manufacturers. Having never used a CMM before, it was hard to evaluate exactly how you might live with a CMM day-to-day. We needed to be able to just get up and running with our inspection without the need for lengthy training courses. The deciding factor was the software. Following a demo at Aberlink's Gloucestershire-based head office it became very apparent how easy to use the Aberlink 3D measurement software was it just seemed more straight-forward. The capabilities on offer were also hugely price-competitive – so it just gave us the complete package."
Helped by an SEMLEP investment grant, MHDE purchased Aberlink's best-selling, complete inspection system, the Axiom too CNC CMM with a 640x600x500mm measurement volume and automatic indexing RTP20 probe.
Now located on the companies modern, temperature-controlled workshop amongst the machine tools on the shop floor, all MHDE's multiskilled team are now using the machine to inspect all parts and are seeing the benefits of the Axiom too CMM.
"Most of our projects require 100% inspection so the Axiom too's CNC capability is brilliant for that. We work in very low volume but once we have programmed one part, if we do need to produce a batch of 10, we can place the parts on the machines granite table and quickly run the inspection. We also carry out in-process checks too, particularly with some of the suspension component work, which has very tight tolerances. Now, there are projects we simply couldn't do without the Axiom too; an advanced CNC CMM has given us so much more capability
"When you're considering investing in a CMM, as a business, it's actually quite a difficult purchase – you can't make anything with it, but it does make you money indirectly. Without it, you can produce a part, but how do you know that it conforms to the customer’s drawing. It’s a huge benefit to our business as it gives the customer a feeling of reassurance."
Designed and manufactured by Aberlink, the largest UK owned Coordinate Measuring Machine manufacturer, the Axiom too is the complete inspection system, which is provided as a turnkey solution to meet the most demanding measurement requirements.
The Axiom too range of CMMs offers measuring volumes from 640 x 600 x 500mm up to 640 x 1500 x 500mm and is available either with manual or full CNC control. Aberlink are proud to be the only major metrology manufacturer to supply machines with zero annual software maintenance contracts and free software updates for the life of the machine. This means that the cost of ownership is very low providing a fast return on investment.
Aberlink are now able to offer remote online demonstrations for the entire range of CMMs, measurement software and accessories to customers who are unable to travel to a regional demo facility.
For more information on MHDE Driven by Precision talk to Aberlink Innovative Metrology
Enquire Now
List your company on FindTheNeedle.