
The Benefits of Magnetic Workholding
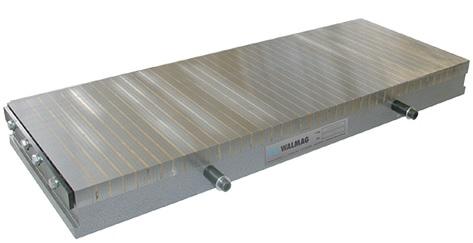
What do you prioritise when it comes to machine workholding?
- Clamping speed?
- Holding power?
- Price?
- Low vibration?
- Availability?
- Ease of comprehension and use?
- Simple servicing and maintenance?
For many, traditional manual clamps are a cost-effective and entirely suitable solution for their workholding needs. They’re cheap, mostly effective and simple to understand.
But, have you considered the benefits of magnetic workholding?
In this blog, we’re going to outline the advantages magnetic workholding offers manufacturers and machinists compared to traditional methods.
How do manual and magnetic clamping compare?
A quick comparison of manual and magnetic clamping shows that magnetic clamping eliminates the pitfalls associated with manual clamping, but the initial time and money investment is higher.
The benefits of magnetic workholding
Faster
Magnetic workholding is often faster than other clamping technologies.
As long as the magnetic clamps are installed on the machine, it’s quick and easy to change between different-sized workpieces. There’s no need to move clamps.
“A key advantage is not having much to set up.” – Clive Leonard, 1st MTA
This reduces downtime, increases throughput and boosts profitability in the long run. Initial investments for magnetic workholding are often paid off very quickly.
Prevents unwanted vibrations
With magnetic workholding, clamping force is applied consistently across the entire surface of the component, which means massive reductions in vibration.
Chatter reductions, simplified programming and five-sided access to a component mean faster and more accurate machining.
Overall cost reductions
Because there are no moving parts, threads or oil, magnetic workholding kits need minimal to no maintenance. They’re also incredibly energy efficient.
Both of these factors help make up for the potential higher initial investment costs associated with magnetic workholding.
Magnetic workholding is also great for future-proofing, especially in regards to automation and unmanned running.
Consistent clamping force
Because magnets offer full surface clamping (reducing deformation) and are either on or off, they offer safe and secure clamping force. By comparison, mechanical vices, even if maintained impeccably are reliant on operator experience and have no built-in safety feature.
If you’re looking for a consistent and easily adjustable grip force, check out our range of Walmag Electromagnets.
Where components are small, thin or fragile, magnetic workholding might actually be superior to traditional clamps. The lack of clamps and easily adjustable clamping force prevent potential damage to components.
Flexibility
Walmag Permanent Magnets, for example, are lever operated, easy to operate and easy to remove/move to another machine.
Plus, because any ferromagnetic component can be used with magnetic workholding, size and shape are less of a factor. This provides flexibility to machinists and engineers, allowing them to work with a huge range of workpieces without frequent setup changes.
Key takeaway
If you’re willing to invest the time in understanding them and the initial investment costs, magnetic workholding offers a huge range of benefits to a variety of machining applications.
For more information on The Benefits of Magnetic Workholding talk to 1st Machine Tool Accessories