
Sign In
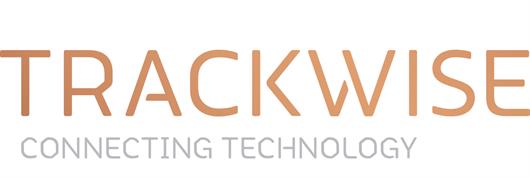
Flexible printed circuits (FPCs) have been around since the early 20th century and can be found in a wide range of industrial and consumer electronic products. Their multiple benefits, including weight, space and cost savings along with their ruggedness and electrical performance, make them a popular choice for designers grappling with the challenge of packing more functionality into ever-shrinking form factors. Until recently, most FPCs have been less than a metre long, due to restrictions in the manufacturing process, limiting their use to smaller applications such as instrument panels, control systems, consumer goods and medical instruments.
This situation has changed recently, however, thanks to Trackwise’s patented manufacturing process which enables the unique manufacture of FPCs of unlimited length. Marketed as Improved Harness Technology™ (IHT), a whole new range of applications are set to benefit from this development, particularly in the automotive, aerospace and telecommunications industries, where traditional, complex wiring harnesses are candidates for replacement by weight-saving FPCs. As many designers will be looking at FPCs with renewed interest, it is worthwhile reviewing exactly what they can be used for and the benefits that they bring.
The six types of FPC
There are actually six types of FPC to choose from, depending on the specific needs of the application, but all are based on the same construction method, best understood by looking at a single-sided FPC, one of the most common types. The FPC is a flexible laminate, formed from four layers of materials, as shown in figure 1.
The base substrate is a dielectric film, which gives the FPC its mechanical properties and also insulates the conductive tracks from one another.
The electrical conductors provide the connectivity and electrical characteristics required by the application.
The adhesives are used to either bind the conductive layer to the substrate to create a laminate or to bind layers of laminate together to form a multilayer FPC.
The cover coat or cover lay is a protective finish applied to the surface of the FPC to protect it against moisture, contamination and abrasion as well as to reduce stress during bending.
FPCs are also defined by whether their application requires a static flex or a dynamic flex solution. In the latter, the FPC may be required to flex many times during its operation, such as in a printer cable. In static flex applications, the FPC may only be required to flex during assembly, to get it to fit into a tight or aerodynamic space.
The different FPC layers and materials
The FPC designer must choose carefully from a range of materials for each layer, based on the electrical and mechanical performance requirements of the application. The base layer needs to provide properties such as mechanical stability, thermal resistance, tear resistance, good electrical characteristics and low cost. The options for base substrate materials have evolved considerably over the years, with polyester and polyimide being popular choices owing to their resistance to high temperatures, excellent tensile strength and flexibility, and their good dielectric strength.
The conductor layer is responsible for the electrical performance, but the choice of material for this layer will also impact the overall lifetime fatigue as well as the stability and mechanical performance of the FPC. While copper’s properties make it the material of choice for the majority of FPCs, aluminium foils and metal mixtures including stainless steel, beryllium-copper, phosphor-bronze, copper-nickel and nickel-chromium resistance alloys are also options. A range of polymer thick-film (FTP) ink-based processes and other printing techniques such as lithography ink deposition have also evolved for use in the conductor layer.
Factors such as cost, temperature resistance, chemical resistance and mechanical strength requirements also dictate the choice of adhesive and the cover lay material and, again, many options exist, depending on the needs of the application.
The benefits of IHT
Now that IHT has removed the length limitation, the field is open for FPC use in a wide range of applications. Among the first sectors to benefit from this new technology are the automotive and aerospace industries, with IHT capable of being long enough to span aircraft wings and flexible enough to be folded into the most inaccessible space within a modern car. Weight saving is a high priority in both industries and FPCs have been shown to reduce weight by up to 75% over traditional wire harnesses, a key benefit for both automobiles and aircraft, where weight is directly associated with operating costs and emissions.
To find out whether an FPC would be right for your application or for more information on them, see Trackwise’s white paper – ‘The engineer’s guide to multilayer flexible printed circuits (FPCs): technologies and applications’. This valuable resource covers all aspects of FPC design, including available materials and design steps.
For more information on IHT opens up FPC weight- and space-saving benefits in many new applications talk to Trackwise Ltd
Enquire Now
More News
List your company on FindTheNeedle.