
Sign In
How to Check you Have Enough Vibro Media..
02-08-2015
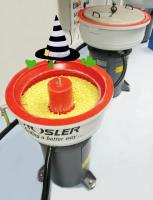
We often find going in to companies the most frequent issue with vibratory bowls is the amount of media being run. It is more often than not too low.
As most media (ceramic and/or plastic) wear, the level in your machine can drop by quite a considerable amount over time.
Mass finishing works by covering the part with the media and the media moving over the edges to perform the deburring, radiusing, etc. it is important than an effective ratio of media : parts is maintained.How much media?
Should the level of media decrease, then your finish could be negatively affected, your process time extended and unloading machines with separation screens you may find that the parts won’t evacuate correctly or that it takes longer to unload the last 1/4 of the parts than it does to get the 3/4 bulk out.
When a process is first implemented an ideal loading of parts will be determined and a full load (parts and media) should fill the process bowl as follows:
Rotary vibratory bowl with separation screen = 70% full to the top allowing media and parts to pass under the separation screen without touching the underside of the screen
Rotary vibratory bowl without screen = 70 to 80% full to the top
Trough vibratory bowl = 80 to 90% full to the top
The next thing to consider..
Water and compound are added into the machine to facilitate the cutting process and remove
any debris coming from the media, parts and any additives so the process stays clean, the media
can keep cutting and doing its work as it should do and to protect the parts being processed (i.e.
with a rust inhibitor if corrosive). Variants of compound can also be introduced to speed up
degreasing, cleaning, removal of heat treatment scale and discolouration, etc… as well as just
helping make the parts look clean and shiny.
rosler water
It is important though that the water and compound mix are kept at the correct ratio as determined during your process trials. Too much water and the bowl is likely to flood, slowing the process movement and affecting process times and the quality of the finish produced. Too little water and the bowl may not clean well enough, parts and media will become dirty (and stained) and the media surface will be ‘closed’ by debris and contaminants in the process bowl.
Too much compound and the likelihood is you’re going to have lots of foam, and lots of mess!
Again this can result in staining and will cushion the movement of the media affecting your finish
and process time. Too little compound and it may not be able to do its job (carrying particles in
the bowl to be evacuated from the process chamber) and as a result the media, lining and parts
will be dirty, the media is likely to ‘clog’ and process times and finish produced will be affected.
For more information on How to Check you Have Enough Vibro Media.. talk to Polishing Jewellery
Enquire Now
List your company on FindTheNeedle.