
Sign In
DEEP DRAWING METAL: THE BENEFITS
16-10-2021
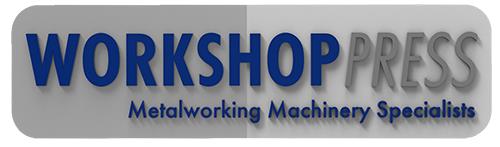
Deep drawing metal is one of the key metal forming processes. It can form metal sheets into almost any shape and is perfect for high-volume manufacturing. With a deep drawing press machine, companies can achieve exceptional accuracy. As well as, consistency, at a fraction of the cost compared to other processes such as turned and machined parts. As a deep drawing hydraulic press manufacturer, we wanted to shed some light on the benefits and the process of deep drawing metal.
The deep drawing process can be applied to a wide range of substrates including:
Aluminium
Stainless steel
Nickel-Silver
Carbon Steel
Brass
HOW DOES DEEP DRAWING WORK?
The metal drawing process starts with a single blank and a metal die. A tool (called a plug) is used to punch sheet metal into a die. The sheet metal will become the same shape as the tools, which is often a round shape with a significant radius and depth to it. Drinking cans are often made using this process. But, deep drawing can be used to create irregular shapes too, such as sinks. The sheet metal is punched into the die. Therefore, the material that is going to be used, must be highly resistant to stress and tension damage. So, failure to use a strong sheet metal can result in a weak product that is subject to breaking easily.
The amount of pressure you apply depends on the type of product you are trying to achieve. Although deep drawing seems similar to metal stamping, the process is different. This is because deep drawing offers the ability to create deeper components. Therefore, components which have been manufactured with a deep drawing machine are usually high in strength, despite their minimal weight.
LIMITATIONS
Deep metal drawing can have some limitations, such as radial drawing stress and tangential compressive stress. As a result, the component can become fractured or wrinkled and crack. However, over the years many new processes have been introduced when it comes to deep drawing such as hydroforming, aquadrawing and hydraulic deep drawing. All of which can help to remove some of the risks and limitations.
THE BENEFITS OF A DEEP DRAWING PRESS
The deep-drawing process is perfect for high-volume requirements. As well as, the need for batch to batch repeatability. Additionally, it is perfect for creating cylindrical 3D components, for example, aluminium cans. Deep drawing is one of the most cost-effective metal forming processes, especially when it is in use for manufacturing high volumes of components. After the tooling and dies have been locked down, the process continues with very little downtime. In addition, with tool construction costs being low too, a deep drawing press is ideal for manufacturers working with tighter budgets.
Other benefits of investing in a deep drawing machine include:
Flawless components
Fast turnaround times
Minimal technical labour
The ability to produce axi-symmetric geometries
Deep drawing is a process that is in use to create many different products including cookware, kitchen sinks, and assembly housings.
CONTACT US TODAY | DEEP DRAWING HYDRAULIC PRESS MANUFACTURER
If you are looking to invest in deep drawing hydraulic presses and looking for a press manufacturer? Or would you like to find out more about metal fabrication machinery? Then head to our website today. Alternatively, you can call +44 (0)800 999 1090 to speak to a member of our team.
If you have found this blog helpful, then you may wish to read our previous blog: The Uses And Benefits Of A Hydraulic C-frame Press
For more information on DEEP DRAWING METAL: THE BENEFITS talk to WorkshopPress.co.uk
Enquire Now
More News
List your company on FindTheNeedle.