
Sign In
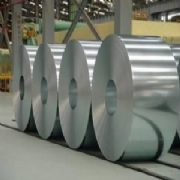
Galvanising
Galvanised steel can be found in many places, it is commonly produced by the “hot dip” process where the steel strip is dipped in a bath of molten zinc (or aluminium or aluminium /zinc mix)
Improving strip quality, increasing production and reducing running costs are important factors for owners and operators of hot dip galvanisinggalvanishgalvalume/zincalume plants around the world. Spooner Industries developments on the critical after pot cooling (upleg) help to provide all of these benefits.
Spooner Industries Ltd has considerable experience in cooling, stabilising and heat retention/soak zones for continuous HDG lines (including exposed automotive). The cooling rates Spooner have achieved on installations within the galvanising industry are far above the industry norm for air cooling and involved Spooner Industries carrying out extensive R&D work, in conjunction with a number of customers, to establish heat transfer rates with high strip temperatures. The joint development work was also aimed at effectively controlling high air velocities and volumes in the most efficient manner possible. We feel this development work provides Spooner with a unique ability to model and design high air velocity cooling equipment for the metal hot dip coating industry.
Spooner have introduced a range of air coolers utilising combinations of precision slot coolers, hole array coolers and Air float / stabilising coolers. The use of Air Float stabilising coolers, which improves strip stability and provides higher heat transfer rates (meaning shorter coolers or increased throughput) improves the coat weight control, can reduce zinc consumption and can allow lower strip tensions on thinner strips, thus giving operating cost savings and reduced maintenance requirements.
For more information on Galvanising Equipment talk to Spooner Industries Ltd
Enquire Now
List your company on FindTheNeedle.