
Sign In
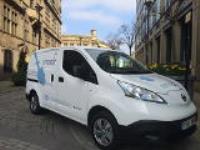
Sheffield-based Airmaster was established in 1992 to supply air conditioning systems for commercial premises. Founder Richard Pogson, an experienced air conditioning engineer, was determined to offer first-class service based on honesty, quality and value for money.
Airmaster soon grew into an established and reputable business, Tony England joined the company in 2000 to share the business and it continued to go from strength to strength. The maintenance division was launched in 2003 and, significantly, progression to a full mechanical services provider with the addition of computer aided design, building simulation software and in-house gas safe fitters. This enabled a full design – installation – commissioning – support service from one supplier. Today, guided by Lisa Pogson and Mark Staniland, joint managing directors, Airmaster’s workforce has expanded to over 40 fully-trained and qualified designers, project engineers, installers and technicians, operates nationally, and still embraces the values on which Richard started the business over 25 years earlier.
Airmaster has achieved certification to ISO 9001:2015 and ISO 14001:2015, with both audits carried out by SGS United Kingdom Ltd.
WHY AIRMASTER SOUGHT CERTIFICATION
High quality and excellent service are in Airmaster’s DNA, as is a professionalism and passion to please its customers that pervades every area of the business from the top down. Long before certification was considered, the company was proactively engaging with customers to set and measure its KPIs, and was also being consistently highlighted as an example of good practice at supplier forums. All feedback, positive or negative, was cascaded back to the entire workforce as a matter of course. Having Investors in People accreditation, Airmaster has a strong development focus, including the management team undergoing the same training as engineers.
Ian Chapman who has worked with Airmaster since 2004 as QSHE Advisor said:
“Airmaster already knew that the company was operating to high standards and that gaining the certification would confirm this to our customers”.
“But there was also more to it than that: we also anticipated that working towards certification would bring further improvements within our internal systems allowing greater control over business growth and helping to provide an even higher quality experience for our customers.”
Ian adds: “Gaining these certifications proves that we are what we say we are.”
The company has also always recognised its obligations to the environment, not least because of its work with fluorinated gases and the replacement and disposal of defunct equipment. Certification to ISO 14001:2015 would endorse this commitment and ensure that formal processes were in place.
WHY SGS?
Ian’s recommendation was based on experience of many auditing organisations, including SGS, who he has been working with on behalf of other clients since 2004. According to Ian, SGS makes the process as easy as it could be, in what can be a stressful time for a company’s quality lead and indeed, the whole team.
He comments: “Having worked with a lot of auditing companies, I have a lot of confidence in SGS. They’re calm, confident and upfront, strike a good balance and give me the confidence that the way they’re doing things is the right way for our business. I’m currently working with two of the best auditors I’ve ever worked with.”
IMPLEMENTING ISO 9001 AND ISO 14001: THE PROCESS
Airmaster set out to achieve ISO 9001:2015, working to the environmental certification only when the quality standard had been granted. These days, there is a high degree of commonality between the two standards, but it was thought that a stepped approach would be preferable in terms of reduced workload and unnecessary pressure.
The quality audit itself was relatively straightforward owing to already robust standards and processes being in place and the enthusiasm of the entire workforce, to the degree that several employees wanted to undertake the auditor training.
Lisa Pogson recalls: “Because none of the team apart from Ian had been through this before, we didn’t know what to expect, so there was understandably a little nervousness. But all we had to do was educate on the process and what was expected, so nobody felt threatened and everyone was included.”
The company’s projected certification date was December 2015, but remarkably – despite one issue which had to be re-visited – it was achieved in August, four months ahead of schedule.
ISO 14001:2015 was achieved one year later. The process proved to be even easier for Airmaster, as the team was now equipped with more confidence and the realisation that the standards work with their systems and not vice-versa.
“SGS was very impressed that the process had the buy-in of the whole team, led by the directors,” says Ian.
HOW THE CERTIFICATIONS HAVE BENEFITTED THE BUSINESS
As mentioned previously, Airmaster wanted to be able to demonstrate that quality is a given and that customers can depend on its sustainability credentials, both of which have been achieved.
Having new processes resulting from working to the standards in place, however, has proved a pivotal step in the company’s development. All processes, procedures, workflows and projects are documented so that they can be referred to by all, act as an audit trail, and remove the reliance on individuals. This even extends to new processes which enable more accurate costing, and oversight into profitability on individual projects in real time.
Certification has also resulted in an even stronger proactive drive for improvement across the whole workforce, which is supporting a new growth accelerator programme. This is accompanied by a company-wide pride in the business and the work it delivers.
At the time of writing, Airmaster is also working towards the new ISO 45001 health and safety standard and expects to be fully ready in time for its introduction.
Ian Chapman concludes: “If you’re going to go for certification, don’t do it because it’s onerous and you have to, do it to improve your business.”
ABOUT SGS
SGS is the world’s leading inspection, verification, testing and certification company with more than 85,000 employees operating in a network of 1,800 offices and laboratories around the world.
For more information on Certification for aircon company proves credentials and improves business talk to SGS United Kingdom Ltd
Enquire Now
More News
List your company on FindTheNeedle.