
Sign In
SAFETY MATTERS October 2014 Newsletter
08-10-2014
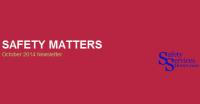
European Week for Safety and Health at Work from Monday 20th October 2014
With hundreds of awareness-raising events taking place across Europe and beyond, the European Safety & Health Weeks in 2014 and 2015 have the theme of managing stress at work at the core of the campaign.
Activities held before, during and after the Week will focus on raising awareness of managing stress and psychosocial risks at work.
Work-related stress is not an individual fault, but an organisational issue. It is one of the most important outcomes of a poor psychosocial work environment.
Psychosocial risks arise from poor work design, organisation and management, as well as a poor social context of work. They may result in negative psychological, physical and social outcomes.
Working conditions such as the following may lead to psychosocial risks:
excessive workloads or time constraints;
conflicting demands;
lack of clarity over the worker’s role;
ineffective communication;
badly managed organisational change.
An unhealthy social context is characterised by situations where there is/are
lack of support from management or colleagues;
poor interpersonal relationships;
harassment, aggression and violence;
difficulties in combining commitments at work and at home.
Psychosocial risks should not be confused with a healthy, stimulating but supportive work environment in which workers are highly motivated and encouraged to perform to the best of their ability.
To find out more about how Healthy Workplaces Manage Stress CLICK HERE
For our Training Course designed for employees to work positively CLICK HERE
Violence at work: keeping your employees safe
Employers owe a duty to their employees to provide a safe working environment and this includes taking steps to protect them from acts of criminal violence in the workplace perpetrated by members of the public. What does that mean, who is at risk and how far must employers go to ensure that they have complied with that duty?
Who is at risk?
Basically, anyone who has contact with members of the public is at risk of violent attack during the course of their employment. Employees at increased risk include those who handle money, those who work alone, especially during night shifts, and those whose work takes them out of the workplace
What should you do?
You have a duty to provide a safe working environment, weighing up the risks in terms of likelihood of injury occurring, and potential consequences if it does; and balance these against the probable effectiveness of precautions that can be taken to meet those risks and the expense and inconvenience involved in doing so. If the employer is found to have fallen below the standard of a reasonable and prudent employer then they are negligent. The extent of the security measures can only be determined by undertaking a risk assessment of the premises and the likelihood of it being targeted.
For a free 'Violence at Work' Brochure CLICK HERE
Knock Knock the HSE are coming!
‘Health as well as safety’ is the message during this year’s Construction Initiative as poor standards and unsafe practices on Britain’s building sites are targeted during a nationwide drive aimed at reducing ill health, death and injury in the industry.
Until 17 October, HSE Construction Inspectors will carry out unannounced visits to sites where refurbishment projects or repair works are underway.
This is the ninth annual Initiative and building on previous campaigns, HSE Inspectors will ensure high-risk activities particularly those affecting the health of workers, are being properly managed.
What the initiative does
The main aims of the initiative are:
to achieve an improvement in industry standards, in particular at small sites
to increase awareness of HSE’s expectations of the industry
to demonstrate that HSE will use the enforcement tools at its disposal to prevent immediate risk and bring about sustained improvements
What inspectors look for
During inspections, HSE inspectors will consider whether:
risks to health from exposure to dust such as silica are being controlled
workers are aware of where they may find asbestos, and what to do if they find it
other health risks, such as exposure to noise and vibration, manual handling, hazardous substances are being properly managed
jobs that involve working at height have been identified and properly planned to ensure that appropriate precautions, such as proper support of structures, are in place
equipment is correctly installed / assembled, inspected and maintained and used properly
sites are well organised, to avoid trips and falls, walkways and stairs are free from obstructions and welfare facilities are adequate
HSE uses the inspection initiatives to reinforce its message to the construction industry that poor standards are unacceptable and liable to result in HSE taking enforcement action.
To have a look at the 2013 Inspectors visits photo gallery CLICK HERE
Reasons why you'll never achieve ZERO HARM or eliminate ACCIDENTS from the workplace
Zero harm strategies are arguably a commitment to protecting your employees but it is only an effort towards improving attitudes towards a more positive safety culture and nothing more....
The slogan Zero harm has become more of a corporate brand than a meaningful vision for a culture. Put simply, zero harm is the right thing to say and little more. It has become a message conveniently plastered everywhere for short-term commercial gain, either to win more work or to say: “look – we’re focused on the right things” to shareholders.
Hopefully your organisation is focused on the correct intention behind zero, but more often than not, when safety vision becomes zero, performance comes nowhere near.
Here are five reasons why that might be the case:
Zero harm works for senior managers, but not the workforce: The intention is there but isn't necessarily effectively communicated further down the employment chain. Employees see changes as an additional burden on top of the existing pressures of productivity levels subsequently meaning that more stress is added potentially therefore increasing risks of accident and injury.
Zero harm doesn’t take account of the group/individual attitudes: Often any change in working practices can cause indignation, individuals and groups within employment enjoy the existing familiar structure and do not like change regardless of how beneficial that it may ultimately be ... How many times have you heard the statement 'I've done this for 20 years this way and not had an accident .. health & safety gone mad!' or 'It’s a paperwork exercise' Changing attitudes is not so easy!
Zero harm is practically impossible: Incidents and accident happen, to achieve zero harm it would have to be measured over a long period of time and then something might happen to spoil the record so is it ever really Zero Harm?
Zero harm is an outcome, not a vision: You can always set your aspirations for your employees, but it is a statement of what you want to achieve as the ultimate aim ... it would be important to communicate that to employees but at what point do you measure that you have achieved it and do you have to have accidents and incidents before you achieve it to demonstrate that you have worked towards it and if an accident occurs after you have achieved it ... did you achieve it at all?
Zero harm is a cliché: If you must use zero in your safety campaigns then bring it to life, that means thinking creatively about how you sell your vision to your workforce and make zero mean something relevant in their everyday lives. There are so many different ways to engage your workforce, especially in the process of creating that vision in the first place. Talk about what really matters to them – that way you’ll make it resonate with them personally.
For Training courses to help you and your employees raise awareness of how they can work towards a safer working environment have a look at our wide selection of Training Courses from Safe Manual Handling, Driving Safely to Lone Working CLICK HERE
NEW BUSY BUILDER LEAFLETS
HSE Construction Division has created four new Busy Builder leaflets - containing simple, straightforward guidance for those who run small construction sites. The leaflets also show real examples of good and unacceptable practice on site.
Fragile Roofs - What You Need to Know
Keep Your Site Tidy - What You Need to Know
Protecting the Public - What You Need to Know
Special Offer Price FROM only £14.00 plus VAT per person
Asbestos Awareness Training course is a must for anyone working in the Building; Maintenance and Construction Industries, and as well as providing full awareness training, our online asbestos awareness training course is also suitable for use as Asbestos Awareness Refresher Training as recommended by the HSE.
IN COURT
Disqualified director jailed over worker death
A businessman has been jailed for serious fraud and safety offences following the death of a worker who was crushed and killed by a two-tonne metal sand-moulding box.
The court was told that Paul O’Boyle had been disqualified from acting as a company director for 12 years in 2006 but continued to act in that capacity at a number of foundry companies, including Aztech(BA) Ltd, which operated from premises in Hampshire.
In running Aztech, Mr O’Boyle was aided by Russell Lee, who agreed to be the registered director of the company. Lee was given a suspended sentence for similar offences.
The offences came to light following the death of Ian Middlemiss, 40, from Thornhill, Southampton, who was crushed beneath a heavy sandbox on 30 September 2010. Colleagues scrambled to free him, but he was pronounced dead at the scene by paramedics.
HSE investigated the death and identified serious concerns with the systems of work in place at the time and with the lifting equipment. HSE became aware of the Companies Act offences and a joint investigation with the Department for Business, Innovation and Skills (BIS).
HSE found that the crane at the centre of the incident had not been checked and tested as the law requires, and there were inadequate provisions in place covering competency, supervision or training. The court heard the incident could have been prevented had the system of work been reviewed and properly assessed.
Inspectors also identified problems with lead exposure. Substances containing lead were used elsewhere at the site as part of a separate bronze moulding process, but the control and health surveillance measures were insufficient - meaning workers were being exposed to potentially harmful levels of lead without realising it.
The court heart that at the time of Mr Middlemiss’s death, the foundry was the subject of three improvement notices served by HSE following earlier visits in September 2009 and June 2010. A number of important safety improvements were required but few had been satisfactorily implemented, largely, claimed the management team, because of financial constraints.
HSE argued that the fatal incident could have been avoided had the necessary changes in the relevant enforcement notices taken place.
Aztech BA Ltd was sentenced for a breach of Section 2(1) of the Health and Safety at Work etc act 1974, after a guilty plea was submitted on behalf of the insolvent firm by its administrators. The court imposed a fine of £100,000.
Paul O’Boyle, 56, from Andover, was jailed for a total of 26 months: 16 months for a breach of the Health and Safety at Work etc act 1974; ten months for a breach of the Fraud Act 2006; and a total of eight months concurrent for four breaches of Section 13 of the Company Directors Disqualification Act 1986. He was also disqualified from being a company director for the maximum of 15 years.
Russell Lee, 67, of Southampton, was given a 12-month prison sentence suspended for two years after admitting the same breach of the Health and Safety at Work etc act 1974 and a concurrent six months, also suspended, after pleading guilty to aiding and abetting O’Boyle in his disqualification.
Lee was also disqualified as a director, for seven years, ordered to pay £8,000 toward prosecution costs and given 150 hours’ community service.
In terms of other offences, the judge heard that between 2006 and 2011 Paul O’Boyle contravened two orders disqualifying him as a director by acting in that capacity in no fewer than four separate companies, including Aztech.
He was also responsible for the cross-firing of cheques, which were written from the bank account of one of the companies, which was no longer trading, to provide funds for Aztech.
BIS investigators established that Aztech drew almost £92,500 in this way, taking advantage of a short window after the cheques were presented but before they bounced.
The investigators also established that Russell Lee aided and abetted Paul O’Boyle as the registered director of Aztech, performing tasks such as writing blank cheques for Mr O’Boyle to run, but not fulfilling the responsibilities of being the director of the company, allowing O’Boyle to run the business.
In his sentencing comments, the Recorder of Salisbury, His Honour Judge A H Barnett, said Paul O’Boyle had behaved in a “disgraceful” way and had been culpable of “extremely shoddy business practice”.
After reading a statement for Mr Middlemiss’s father, the judge said the impact of the incident had been devastating: “It was harrowing, and underlines the personal tragedy that could have been avoided.”
After sentencing, Tim Galloway, HSE director of operations, southern division, said: “The safety standards at Aztech BA Ltd fell well short of those required, as Paul O’Boyle and Russell Lee were only too aware. They knew improvements were needed to protect workers like Ian Middlemiss and they had clear responsibilities as senior management to ensure the necessary changes were implemented.
“Sadly one of the many areas that was seemingly overlooked was the system of work surrounding the overhead crane. Had this been properly assessed then Ian’s tragic death could have been prevented.”
Resident’s burn related death leads to nursing home fine
A nursing home in Deeside has been fined £5,000 after an 88-year-old resident suffered burns in a bath of scalding water.
Beatrice Morgan, a resident at Greencroft Nursing Home in Aston, Queensferry, died of complications caused by her injuries a month after the incident.
HSE investigated and prosecuted the home’s owner, Greencroft Care Ltd, which is now in liquidation, at Mold Magistrates’ Court on 25 September.
The court heard that, on 29 August 2012, Miss Morgan, who was unable to walk, was lowered into the bath using a hoist and immediately cried out when she touched the water. Although she was quickly raised from the bath, she suffered nine per cent burns and was taken to Whiston Burns Unit where she later died.
HSE’s investigations found that the temperature of the hot water was not properly controlled to prevent it exceeding 44˚C. Although mixing valves had been fitted to control the temperature they had not been maintained and were not of the right standard required in nursing homes.
Staff had been instructed to check water temperature with a thermometer before baths, but no checks were made by management to ensure this was happening. There had been a failure by the company to fully assess risks involving use of hot water and to provide sufficient training, instruction and supervision to staff.
Greencroft Care Ltd of Larch Avenue, Aston, pleaded guilty to a breach of the Health and Safety at Work etc. Act 1974 and was fined £5,000. The judge at the hearing said if the firm had not been in liquidation he would have sent the case to crown court, where the fine would have been at least £100,000.
HSE inspector Katharine Walker, speaking after the hearing, said: “This tragic incident could easily have been avoided if Greencroft had observed the readily available guidance on bathing vulnerable people. The company fell well short of the desired standards.
“Miss Morgan suffered a great deal of unnecessary pain before her death. Nursing homes and other organisations caring for vulnerable people must make sure they fit and maintain the right kind of mixer on hot bath taps and properly supervise their staff.”
Saw milling firm in court over worker’s fall
Wigtown-based Penkiln Sawmill Company Ltd was handed a £10,000 fine on 23 September for safety failings, which led to a worker’s fall and resulted in multiple injuries.
Fifty-six-year-old employee Tony Heron was putting tin sheets on the roof of a lean-to shed at the firm’s Wigtown premises on 1 February 2013 when he fell eight feet through a fragile roof-light to the ground below.
Stranraer Sheriff Court was told that Mr Heron was on the roof of an old joiner’s shed, which adjoined the lean-to shed he was working on. He was putting sheets of tin onto the roof trusses of the lean-to and then fixing them in position by screwing them down.
The company had not carried out a risk assessment for the task and had failed to put any control measures in place to minimise the risk of a fall from height.
The pile of tin sheets Mr Heron was using had earlier been lifted up on to the roof of the old joiner’s shed by forklift. The employee had to take a sheet of tin from the pile, walk along the shed roof to fix it on to the lean-to roof, and then go back to get another sheet. The shed roof incorporated fragile PVC roof-lights.
On one of these trips, Mr Heron fell through one of the roof-lights to the ground below, suffering multiple fractures to his vertebrae and ribs and a cut to his head, which needed 14 stitches. His injuries meant that he had to wear a back brace for up to 24 hours a day for several weeks and, despite taking painkillers, he remained in constant pain.
He was unable to return to his job and now suffers impaired mobility in his spine. His back injury is not expected to improve.
An HSE investigation found the Penkiln Sawmill Company Ltd had failed to carry out any risk assessment or to come up with a safe system of work for the task that Mr Heron was engaged in at the time of the incident.
Suitable control measures would have included the provision of platforms, coverings, guardrails or similar means of support or protection on or around the fragile roof-lights or around the open edges of the roof to prevent a fall from height. The firm also failed to provide adequate information, instruction, training and supervision for the task.
The firm was fined £10,000 after pleading guilty to breaching section 2(1) of the Health and Safety at Work etc. Act 1974.
HSE inspector Lesley Hammond, said: “This was an entirely avoidable incident. Falling from height is one of the most common reasons for injury and even fatalities at work, and it is fortunate that Mr Heron survived such a fall, albeit with significant injuries.”
The HSE inspector added that the firm should have been aware of the risks and precautions that needed to be taken, before starting the work.
“The dangers of fragile roofs are well-known and consideration should have been given to using barriers to prevent access to the roof-lights, or taking steps to cover them over with suitable material.”
Falling through fragile roofs and roof lights accounts for almost a fifth of all fatal incidents, which result from a fall from height. On average, seven people are killed every year after falling through a fragile roof or roof-light. Many others suffer permanent disabling injuries.
For more information on SAFETY MATTERS October 2014 Newsletter talk to Safety Services Direct Ltd
Enquire Now
List your company on FindTheNeedle.