
What Is SLS 3D Printing & How Does It Work?
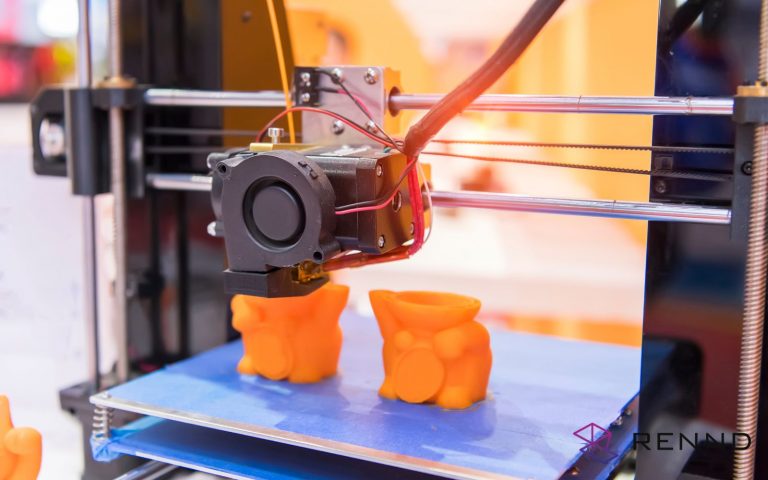
3D printing technology has come a long way since its inception, and one of the latest developments is Selective Laser Sintering (SLS) 3D printing. This advanced process brings with it unique opportunities to create complex, intricate parts as well as other advantages.
In this article, we will explore what SLS 3D printing is, how it works and why it’s becoming more popular in recent years.
How SLS 3D Printing Works
SLS is a 3D printing method that uses a strong laser to join small particles of material to make a solid object. Unlike other 3D printing methods, SLS doesn’t need support structures because the unused powder around the printed object supports it.
The process starts by spreading a thin layer of powdered material over the build area. Then, a laser beam melts and joins the particles together according to the digital design. This process repeats until the object is complete.
After printing, the object needs to cool down before removing it from the smooth surface of the printer bed. Finally, any extra powder can be brushed off or cleaned with compressed air.
Explanation of the SLS 3D printing process
The process starts by spreading a thin layer of powder on a platform. The laser then fuses the powder together in specific areas based on a design. The platform is lowered, and another layer of powder is added. The laser fuses the new layer with the previous one until the final object is created.
SLS printing can use different materials like nylon, polyamide, and polystyrene. It’s great for making prototypes and parts for industries like aerospace and automotive engineering. SLS printing is faster than traditional manufacturing and allows for more design freedom because it can create complex shapes.
Overview of the SLS 3D printer components
One of the key components of an SLS 3D printer is the powder bed. This component acts as both the build platform and the reservoir for the powdered material used in printing. The polymer powder bed must be heated to a temperature just below its melting point to ensure proper bonding during printing.
Another crucial component of an SLS 3D printer is the laser system. This laser system includes a high-powered CO2 laser that is directed by galvanometers to melt and fuse small areas of powder at a time according to design specifications from computer-aided design (CAD) software. In addition, there are several mirrors and lenses that help focus and direct the laser beam accurately.
The third significant component of an SLS 3D printer is the control software which manages all aspects of printing including temperature regulation, movement control, layer height adjustment, and more. The software plays a crucial role in ensuring that each print job progresses smoothly without errors or imperfections while controlling different parameters such as speed, power output, and scan length.
Overall these components work together seamlessly to produce top quality, highly accurate parts with excellent surface finish using SLS technology.
Explanation of how the SLS 3D printer builds an object
The process starts with the preparation of a CAD file, which contains all the necessary information about the object to be printed.
The first step in building an object using an SLS 3D printer involves spreading a thin layer of powdered material over a build platform. A high-powered laser then melts specific areas of this powder according to the design specifications contained in the CAD file. As each layer is melted, another layer of powder is spread on top until the entire object has been built up.
Once complete, any excess powder can be removed by brushing or blowing it away from the final product. This results in an incredibly precise and accurate creation that can be used for everything from prototyping new designs to manufacturing finished products ready for sale.
Comparison of SLS 3D printing with other 3D printing technologies
Compared to other 3D printing technologies, such as FDM or SLA, SLS offers a higher level of detail and precision.
Fused Deposition Modeling (FDM) is another popular 3D printing method that uses a filament of thermoplastic material to create objects. Unlike SLS, FDM requires support structures during the printing process which can be time-consuming and difficult to remove once the object is finished. However, FDM printers are significantly cheaper than SLS machines and are better suited for producing larger objects.
Stereolithography (SLA) is another form of 3D printing that uses UV light to cure liquid photopolymer resin into solid objects. Like SLS, SLA produces high-quality prints with intricate details but lacks the ability to print multiple colours or materials at once. Additionally, SLA parts are more brittle than those produced through SLS due to the use of resin instead of plastic powder.
Advantages Of SLS 3D Printing
One major advantage of SLS 3D Printing is its ability to produce parts with excellent mechanical properties. The final products are strong and durable which makes them ideal for use in various industries such as the automotive industry, aerospace and medical. Additionally, this printing method provides users with the freedom to design complex geometries that would be impossible with traditional additive manufacturing methods.
Another significant benefit of SLS 3D Printing is its cost-effectiveness when compared to other forms of manufacturing techniques such as injection moulding or CNC machining. The reduced setup times associated with SLS production ensure fast turnaround times while the absence of expensive tooling costs ensures affordable pricing for low-volume production runs.
Ability to create complex shapes
One of the major advantages of SLS 3D printing is its ability to produce functional prototypes and end-use parts with complex internal structures. With traditional manufacturing methods, such as injection moulding or CNC machining, it can be difficult or impossible to create these types of shapes without additional assembly steps or tooling modifications.
In addition, SLS 3D printing can also enable greater design freedom when compared to other additive manufacturing techniques like FDM (fused deposition modelling) or SLA (stereolithography). Because there are no support structures required during the printing process, designers can create more complex geometries without worrying about limitations imposed by support removal.
Flexibility in materials used
One of the advantages of SLS 3D printing is its flexibility in materials used. It allows for the use of various thermoplastic powders, including nylon, polystyrene, TPU, PEEK and many other polymers with different properties.
The possibility to choose from a wide range of materials makes SLS 3D printing suitable for different applications such as functional and rapid prototyping, jigs and fixtures manufacturing or producing end-use products. Each material has specific characteristics that affect its strength, durability, flexibility or heat resistance. Therefore, choosing the correct material for each application is critical to ensure high-quality parts.
Moreover, SLS 3D printing reduces waste by only using the required amount of powder needed to create a part. Any unused powder can be recycled and reused in future prints which contributes to reducing costs and environmental impact. This further shows how flexibility in materials used through SLS 3D Printing can benefit not only product quality but also sustainability efforts.
No need for support structures
One major factor benefit SLS has over its rival technologies is that support structures are not added. This has downstream benefits –
In FDM printing overhanging sections which require support can often have a poor surface finish, this is partly due to the fact that there has to be a gap between the support and the part (required to prevent fusion) which means the new plastic isn’t been laid onto a perfectly flat surface. Cooling overhanging sections can also be tricky, especially if the part cooling fan only blows from one side. FDM parts which require a show finish but have overhangs will often need filling and sanding to achieve perfect geometry.
SLA prints require individual support nubs to be removed often through filling and sanding. If the part has a lot of hard-to-reach areas or there are hundreds or thousands of parts to prep the post-processing can be a time-consuming and laborious task.
The lack of required support makes SLS ideal for creating intricate designs, functional parts with moving components, and multiple assemblies in one print job. Additionally, since there is no need to manually remove supports from finished prints, SLS allows for faster post-processing times and reduces overall production costs.
Scalability
Scalability is a critical factor to consider when it comes to SLS 3D printing. As businesses grow, they may require larger and more complex 3D-printed parts, which can put a strain on production capabilities. However, with scalable SLS 3D printing technology, manufacturers can easily increase build volume or decrease the size of their products without sacrificing quality or accuracy.
One way to achieve scalability in SLS 3D printing is through the use of modular machines that can be expanded as needed. These machines have interchangeable components and modules that allow manufacturers to add new features and increase capacity without having to purchase an entirely new system. Another approach is to utilise software-driven automation tools that enable faster processing times while reducing the risk of errors.
Ultimately, leveraging scalable SLS 3D printing technology provides businesses with greater flexibility and agility in meeting their evolving needs. By investing in this approach early on, companies can position themselves for long-term growth while minimising disruptions and costs associated with major equipment upgrades down the line.
What Materials Are Used For SLS Printing?
The materials used for SLS printing are generally thermoplastics or other heat-resistant materials that can withstand the high temperatures required for laser sintering. Nylon is one of the most durable and popular materials used for SLS printing due to its durability and flexibility.
Apart from nylon, other commonly used materials include polycarbonate, TPU (thermoplastic polyurethane), and PEEK (polyether ether ketone). Each material has its unique properties and advantages depending on the intended use of the material properties in the final product. For instance, PEEK is known for its excellent mechanical strength and resistance to chemicals and high temperatures, making it a material ideal for aerospace applications.
In addition to these key benefits over traditional thermoplastics, new developments in SLS printing have led to the use of biodegradable materials such as polylactic acid (PLA) and polyhydroxyalkanoates (PHA). These eco-friendly options offer a sustainable alternative in industries such as packaging or medical devices where single-use products are common.
Applications of SLS 3D Printing
One of the most significant applications of SLS 3D printing is rapid prototyping and manufacturing. With this technique, it’s possible to create complex geometries and intricate designs that would be challenging or impossible using traditional methods such as injection moulding. From aerospace components to automotive parts, product designers can use SLS to produce actual parts quickly and cost-effectively.
Another area where SLS 3D printing has shown great potential is medical implants and prosthetics. The ability to customise designs based on an individual’s unique anatomy has made it possible for orthopaedic surgeons and dentists to create personalised solutions for their patients.
This approach reduces lead times significantly while improving patient outcomes by reducing recovery time, minimising postoperative complications, and providing better functionality than traditional prosthetics.
Conclusion
In conclusion, SLS 3D printing is a highly versatile and cost-effective, technology that is used to create complex shapes using SLS materials and designs with great accuracy. The process involves melting a fine layer of powder using heat from a laser, which fuses the particles together to form solid objects. The technology has numerous applications across various industries including aerospace, automotive, healthcare, and consumer products.
Overall, as this selective laser sintering technology continues to evolve and improve over time, we can expect to see even more innovative uses for SLS 3D printing in the future. Its ability to produce complex geometries with high precision will undoubtedly make it an invaluable tool for designers and engineers looking to create new products that were previously impossible or too expensive to manufacture using traditional methods.
For more information on What Is SLS 3D Printing & How Does It Work? talk to RENND Ltd