
Sign In
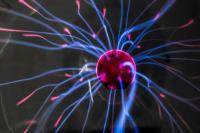
What is Plasma Surface Treatment?
Plasma itself is a gas that's been ionised with both negative and positive, freely moving electrons. When Plasma bonds with a material it enhances the material energy or wettability, enabling it to bond easier as part of the Plasma Surface Treatment process. When the plasma bonds with a material, the transferred energy allows chemical reactions to take place on the material surface and therefore changes the material’s properties – but what does all of this mean in regards to elastomer seals and components?
When it comes to surface treatment at Novotema, we use this process to produce a thin film upon the surface of the rubber components that delivers a range of benefits to the initial product. All grades of elastomer can be coated with this treatment.
Novotema recently developed a new generation of plasma following the increasing demand for alternatives to standards coatings such as PTFE or Chlorination treatment.
Benefits of Plasma Surface Treatment
If we consider that the process changes the properties of a material, it’s important to understand how it changes them and why this might be necessary or desired.
For rubber components, Plasma Surface Treatment is used to reduce the physiological sticking effect and reduce friction. As a result of this, the surface treatment process can drastically improve the performance of moulded components and their operating characteristics in a multitude of ways;
With reduced friction and sticking, the coating acts like a lubricant and makes installation and assembling of equipment easier – resulting in improved performance of dynamic sealing components.
It extends the lifespan of components due to protection from chemical attack and corrosion.
The process is extremely versatile, used in a wide range of industries and it’s difficult to overtreat components, unlike alternative methods.
As Plasma Surface Treatment arose out of demand for an alternative to PTFE and Chlorination coating techniques, the benefits of this include;
Plasma is more robust than PTFE and is more sustainable as it doesn’t consume or waste any materials.
The process of Plasma Surface Treatments is much more sanitary than PTFE coatings. PTFE is an adhesion of Teflon powder which, if not well processed, can release residue and impact the sterility of equipment and machinery.
From an environmental perspective, the use of Plasma Treatment on surfaces reduces the use or necessity of alternative harsh chemical techniques (such as Chlorine) to generate a similar outcome.
Plasma Surface Treatment is also inexpensive when compared to PTFE, and provides more consistency in terms of performance than that of Chlorination.
Applications of Plasma Surface Treatment
The process has been adopted by a range of industries, including Pharmaceuticals, Food and more – but in what context? To help you understand the application of Plasma Surface Treatment and its versatility we’ve gathered some examples of Plasma Surface Treatment uses in industrial applications:
Shutters
Rubber shutters (plugs) used in Control Valves, benefit from increased anti-sticking effect after Plasma Surface Treatment, preventing them from sticking to the valve seat.
Lip Seals
Often required in dynamic applications, lip seals need to demonstrate a low friction force and, in some applications, a reduced stick-slip effect which can be achieved through Plasma Surface Treatment.
O-rings
O-rings often require reduced sticking and friction in order to avoid the seals sticking to the housing – a problem which can make real-life applications incredibly difficult.
Get in touch
Are you looking to improve the performance and lifespan of your components with Plasma Surface Treatment? Novotema offer assistance and consultancy for a range of Surface Treatments.
For more information on Plasma Surface Treatments: Everything You Need to Know talk to Novotema SpA
Enquire Now
List your company on FindTheNeedle.