
Sign In
The case for Gravity Die Casting
16-07-2018
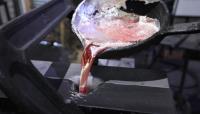
There are many different casting processes and each has its place. The inherent characteristics of each make them ideal for a particular component geometry, performance requirement, alloy choice, production run or tolerance within specification.
Gravity die or permanent mould castings use a Cast Iron or Steel mould consisting of at least two parts. The most common variant uses gravity to fill the mould and, depending on the types of alloy cast and their pouring temperature, the moulds can be re-used many thousands of times. The process is used primarily for casting low melting point non-ferrous alloys of Aluminium, Magnesium and Copper. Component weights generally range between 0.5kg and 50kg.
The choice of casting process will largely be dictated by the characteristics of the process compared to the specification of the component and its production run. Gravity die castings, for example, cool faster than sand castings, giving them a much finer, more uniform microstructure. This boosts mechanical properties by up to 20% and the near-net-shape parts reduce final machining requirements dramatically.
It is also possible to cast complex geometries. Under-cuts and voids of all shapes and sizes can easily be moulded directly into gravity die castings. Brass thread inserts, for example, are more durable than machined aluminium thread. Likewise, Steel and Stainless-Steel inserts can provide extra-hard surfaces only where needed, keeping the rest of the component as lightweight Aluminium.
Mould production costs and resiliance fall somewhere in the middle compared to other processes. Tooling for gravity moulds is generally more expensive to produce than those for sand casting but considerably cheaper than those used in investment and pressure die casting. The result is that gravity die casting is generally uneconomical for very low production runs. For longer runs, however, the speed of the process, the dimensional accuracy and surface finish make it a good choice.
NovaCast’s foundry in Melksham specialises in non-ferrous castings using both sand and gravity die casting while our Far Eastern facilities focus on investment and ferrous castings. We are, therefore, able to advise on the most appropriate casting process and alloy to suit performace requirements. There have been many instances where we have lowered production costs and improved performance simply by changing the process or converting complex fabrications to castings.
If you are investigating the best option for a cast or machined component and need to call on our experience and expertise we would be delighted to hear from you. Call our team on +44 (0)1225 707466 or email sales@novacast.co.uk.
For more information on The case for Gravity Die Casting talk to Novacast Limited
Enquire Now
List your company on FindTheNeedle.