
Sign In
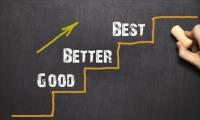
Having got the building design right for your pharmaceutical manufacturing needs, whether that is a single story manufacturing floor or multiple floors, it is important to choose the right container-based materials transfer system that will ensure that your pharmaceutical equipment is functioning well and factory production flow is optimised. As you start to investigate which IBC is the best, don't be driven by price alone. What initially looks like a cheaper option may not give you the performance you ultimately need. It is worth doing your research and understanding the benefits and limitations of the different types of IBC on the market today. We have created a handy checklist of the types of questions to ask when making that selection.
The type of IBC you choose depends on many different factors which we will explore in a series of blogs over the coming weeks. This blog looks at what to consider if you have a product that is prone to segregation as it transfers between the pharmaceutical equipment.
How Segregation Can Occur:
Segregation occurs when particles separate due to differences in their size, shape, or density. It can be caused by the way in which a powder blend is handled throughout the production process.
If dry granulation using roll compaction is a process step in your pharmaceutical manufacture, again it is important to prevent material from segregating as the quality of the granules produced are dependent upon the quality of the in-feed from the IBC.
It is well known in the industry that butterfly valve and slide valve IBCs can cause material segregation as they create core or funnel-flow during the discharge process. Flow of material only occurs in a narrow vertical channel from the open area of the outlet to the top surface of the material in the container, creating a hole within the vessel, also known as ‘rat-holing’. As the material on the top always prefers to flow towards the central core it results in material being held along the sides of the vessel, as the powder moves to the central core it enables particles to roll and separate creating segregation.
The Implications of Segregation Are Critical.
If the material de-mixes or segregates as it is being fed into the tablet press it will result in the incorrect proportions of active ingredient in each tablet – and result in batches having to be scrapped. If you can’t guarantee production quality it will lead to issues with the regulatory authorities.
Solutions to Powder Blend Segregation
To prevent the problem of powder blend segregation you need to look for IBCs that promote mass-flow discharge. Upon discharge, all the material in the container moves at the same rate across the whole container, creating uniform flow – no stagnant material, no rat-holing and a first in-first out sequence of material movement.
For more information on QUALITY ISSUES OF SEGREGATION AND THE PHARMACEUTICAL EQUIPMENT TO USE? talk to Matcon Ltd
Enquire Now
More News
List your company on FindTheNeedle.