
Sign In
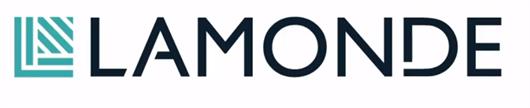
We talked to Nick Oldfield about how he’s used a CLICK® PLC and Weintek in application for a pharmaceutical client. It was really important that the PLC had high speed input capacity for this project. Nick Oldfield Ltd is based in Liverpool but work with clients all over the world. Tell us about yourself: I left school at 16 and did an apprenticeship. I got my HND on day release and moved into project engineering. I worked for a company which made systems for pharmaceutical packaging security for 6 years, then I set up my own business in 1995 and have been doing that ever since. We specialise in supply, installation and integration of a system from PCE (now part of Mettler-Toledo). What do you like to do when you’re not at work? I’m a fan of motorcycle racing – I don’t ride on the road anymore but I love the TT races. I support Dave Molyneux, who is a sidecar driver, and have also helped Ryan Kneen in the Classic TT. I also do the occasional track day. Tell us about a recent application that Lamonde has helped with: I was asked to install and integrate a print and inspect system on to a lid-sealing machine for a pharmaceutical company client who produces devices which deliver self-injections. The packaging is a moulded plastic tray with a foil seal. The industry has strict regulatory standards about the information which must be printed onto the seal, and the quality of the print. In the past the customer has coded or printed the sealing lids on to the plastic packaging tray after they’d been sealed and they felt it was slowing them down. They want to speed up the process by printing the lids before they are sealed in place. I designed the installation and integration of a printer and a camera to go on the machine that puts the lids onto the trays. The industry has strict regulatory standards about the information which must be printed onto the seal, and the quality of the print. What equipment/software were you using? Lamonde supplied me with a Weintek MT8051iP HMI and a CLICK® C0-10-DD2 PLC. It was really important that the PLC had high-speed input capacity for this project. I’ve used the PLC to control the system and the Weintek to act as an operator interface, with an engineering menu to setup and alter parameters if needed. The PLC monitors the digital output from the cameras (which inspects the lid printing quality) – which has the capacity to fail the seal and reject an item if the standard isn’t met. How did you become a Lamonde customer? I did some work for a company in Harwich, they were using a Weintek HMI, and their engineer recommended Lamonde to me. That was in 2012, and I’ve never bought a small HMI from anyone else since then. I’ve used the PLC to control the system and the Weintek to act as an operator interface… What did we do to support you on this project? For this project in particular, Duncan specified a PLC with highspeed input capacity and gave me 121 support on the PLC and HMI programming, often at unsociable hours! Thanks for taking the time to talk to us Nick. Get in touch with us on +44 20 3026 2670
or email sales@lamonde.com to discuss how our solutions will work for you.
For more information on Case Study: Print and Inspection in Pharma Application talk to Lamonde Automation Ltd
Enquire Now
More News
List your company on FindTheNeedle.