
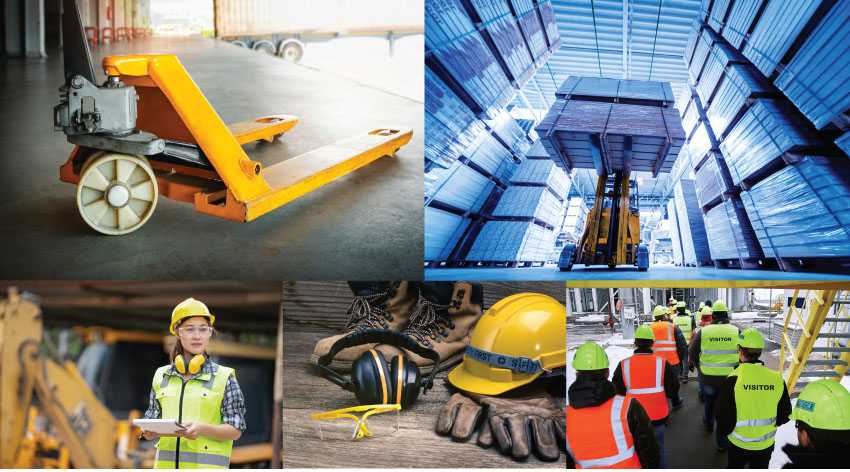
If you’re an employer or employee in a warehouse, you need to ensure you and your employees/colleagues are properly protected at all times from any potential risks. This includes being aware of any hazards on site, and always having access to, and wearing, the correct PPE.
In this blog post, we’ll look at some PPE examples that may be necessary in a warehouse environment, when they’re likely to be needed, and how else to prioritise health and safety in a warehouse environment.
When Should PPE Be Used in the Workplace?
In the interest of your health and safety, you should always wear PPE if it’s suggested you do so . If you work in a warehouse, you’ll likely find that you need to wear PPE more often than other types of employment.
This is because warehouse work often involves the use of heavy machinery, potentially dangerous tools, and interaction with dust. Working with these day-to-day puts you at higher risk of injury, so it’s important to always wear the appropriate protective clothing.
Warehouse PPE Requirements
Some of the most common warehouse PPE includes the following:
- Beanies/caps (protecting from dust and the cold)
- Ear protection
- Glasses and/or goggles
- Gloves
- Helmets
- High visibility clothing
- Respiratory protection, such as face masks
- Steel-toe boots
Your employer should supply you with a PPE warehouse checklist and have a warehouse PPE policy to help you stay as safe as possible in your workplace.
What Warehouse Tasks Require PPE?
There are lots of tasks within a warehouse that require PPE to be put on before getting started. Some of these might include:
- Using heavy machinery, such as a forklift – helmet and high-visibility clothing
- Encountering chemicals – eye, respiratory, and full-body protection
- Carrying heavy objects – steel-toe boots and gloves
- Using loud machinery – ear protection
With so many potential hazards at all times, however, PPE like steel-toe boots, helmets, and high-visibility jackets may need to be worn at all times.
What Else Can be Done to Minimise Warehouse Dangers?
Provide Training
Your employer should train you to properly use any potentially dangerous items or machinery in the workplace to keep you as safe as possible.
For example, you should always receive appropriate training on fire safety, lifting heavy boxes, using ladders, and any other day-to-day activities at work that pose a potential risk.
Staying Organised
Warehouses can easily become messy, and with mess come the risks of falling objects and tripping over items on the floor.
Stack items with a system of largest to smallest, ensure stacks aren’t piled too high, and store items on shelves wherever possible. You should avoid leaving items around the edges or in the middle of the floor wherever possible as these pose a hazard where people may need to step or drive.
Using the Correct Signage
Whether it’s to signify a need to use PPE or warn employees of any other hazards in the warehouse, purchasing and laying out labels and signage can be the difference that saves a life.
Label Source Can Help
At Label Source, we supply signage for warehouses, including PPE signs. We also provide labels for stock identification, shipping labels and tapes, and other warehouse safety products that are essential for the health and safety of employees in a warehouse.
Start browsing our products or get in touch with us at Label Source today to find out exactly how we can help you.
For more information on A Guide to Personal Protective Equipment (PPE) for Warehouse Workers talk to Label Source