
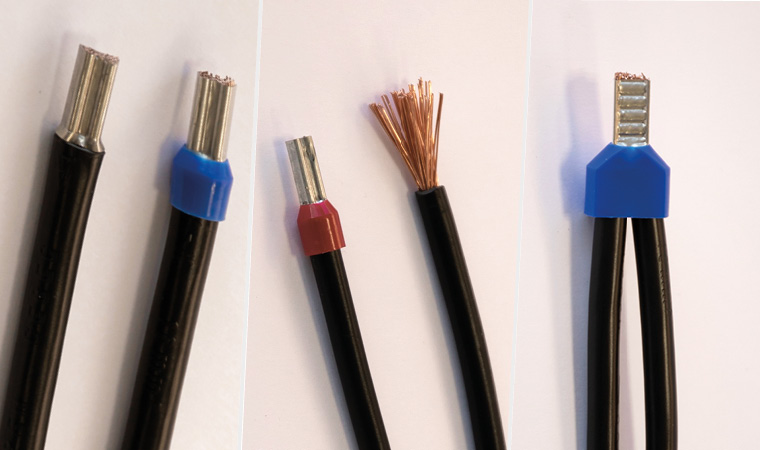
Correctly processing cable end-sleeves: Here's how to do it!
Even if the specifications of the clamp manufacturers do not always require the use of cable end-sleeves: We recommend that you always use them in general! Because they not only prevent the cable from splaying, but also help to avoid many mistakes. What's more: at the end of the day, time and money are saved during assembly.
Tip No. 1: It's all about the right tool
Cable end-sleeves between 0.5 and 50 mm² are defined in the DIN 46228 standard. The substandard DIN 46228-4 applies to insulated cable end-sleeves, DIN 46228-1 to uninsulated cable end-sleeves, while -2 and -3 apply to special shapes. For products for export to the USA, the UL 486F standard is also relevant. However, there are no regulated requirements for all other cross-sections. Due to the resulting variety of available cable end-sleeves, it is particularly important to pay attention to the choice of the right tool.
For large cross-sections, the use of a battery-powered hydraulic tool such as the EKWF120ML from Klauke quickly pays off. For small cross-sections, on the other hand, it is recommended to use lighter electromechanical crimping pliers such as the EK50ML or hand tools such as the K507 WF. To ensure the quality of the crimping results, it is generally beneficial if the cable end-sleeves come from the same manufacturer as the tool. This guarantees optimal compatibility. At the same time, this is also a condition for tests to be valid.
Tip No. 2: Knowing and understanding crimping shapes
Indent, trapezoidal, square and hexagonal crimping have become generally accepted. Indent and trapezoidal crimping is mostly used for tools with predefined crimp inserts. The square and hexagonal crimping, on the other hand, is often used with force-dependent and stroke-dependent tools. These offer the great benefit of automatically avoiding the wrong nest die being used by mistake. It also makes it easier to compensate for severely thinned cables.
Good to know: what is tested and how?
Two different tests are defined: the tensile test and the dimension test. In the case of the tensile test proof of the mechanical connection between conductor and cable end-sleeve is tested. The following applies: a cable end-sleeve must withstand the same tensile forces as the bare conductors of a terminal. The tensile forces for cross-sections up to 50 mm² range between 10 and 190 Newton and must be held for one minute at a time. During the dimension test, it is ensured that the crimped cable end-sleeve also fits into the connection terminals provided.
For more information on Tips for correctly processing cable end-sleeves talk to Klauke UK Limited