
Sign In
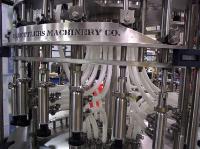
Here are some of the advantages provided by this design:
#1 – Reduced spares – When compared to a P/G filler the wear list for valve parts alone can be reduced at least 50% annually. The reason for this is two–fold. The valve does not require mechanically activated stroking and thus there are simply fewer parts – no spring, no bushing, no bushing seals, no tip o-ring, and only one dynamic seal. Secondly the valve is so much stronger that valves won’t bend or leak very easily. With this design the slide rod would probably bend before the valve. There is no shoe to wear and thus no shoe rod or shoe rod seal. Also the hoses could potentially be changed to Teflon lined, and never have to be replaced again.
#2 – Fewer leaks – Because the valve is closed using an actuator – there is a positive seal against the product with much more sealing power, meaning that the valve is not being held closed by gravity alone against product pressure…therefore the valve tip should not leak due to some pulp resistance or a damaged tip or seal. There is no bushing seal that must be loose enough to prevent sticking valves, which may wear quickly and leak. There is no possibility for the valve to stick or stay open due to sugar buildup or plastic bushing swelling. There is no way the valve can hang open from hose overlap. This valve should work as well a year from now, as when it is new, with just minor seal lubrication and care, versus major valve overhauls.
#3 – Less downtime – For all of the reasons above and more – this machine should not experience major downtime from valve damage, valve failure, or valve upkeep. Fewer and stronger parts mean fewer headaches.
#4 – Less Overflow - P/G fillers send product through the overflow leg anytime the pump is on, the bottle is full and the shoe is not engaged. It is even worse when no bottle is present. Many customers calculate overflow only when the filler is running bottles through the system and they overlook the surge when the machine starts/stops or runs out of containers. Further waste is incurred with bottle size changes that create early fills and with much of the rotation simply overflowing. With electronic fill shut-off, the overflow can be programmed to compensate for these conditions. The savings in product reheating, return, product quality, and waste, can alone justify the conversion.
#5 – Adjustment – With electronic control of flow angle – there is no need to stop the machine, climb on the roof, and adjust the mechanical shoe position. It can now be done on the fly, at any time; and saved through recipe menu screens.
#6 – CIP – Never before in P/G filling could valves be flushed at a given angle individually, whether rotating or not. This means no more CIP cups, as well as the option for higher velocities at the same previous pressures into a CIP tray; if desired for collection and return. With no more shoe, the system is simply cleaner from manifold to manifold. And the valves can actually be automatically pulsed and stroked to promote full milking and flushing conditions.
#7 – Pulpy products – The P/G filler has never been promoted as a filler of pulpy products, but many customers do include certain products that fit this market. The new EL-G filler is by far more agreeable to this family of products due to a different inner tube design, larger clearances between telescoping tubes, and a fully open supply manifold pathway. There is even a functionality to open the valve in a non-contact start condition, if that would help initiate flow normally restricted from pulp settling.
#8 – Variable fill logic – What if you could alter the valve opening and closing sequence during the filling cycle? Now that ability exists with programmable versatility – never before available in any contact style filler. Stop the fill when you want. Restart the fill when you want. Open the valve fully – relieve pressure, close later – close earlier – all at the touch of a keypad. Total flexibility.
#9 – Future adaptability – The EL-G filler is basically one step away from becoming an electronic meter filler; all that is missing is a meter upgrade. The El-G filler allows for future bottle neck support whereas the P/G filler does not. These two capabilities allow for maximum flexibility and future potential, without adding those costs until they are needed. An EL-G filler is a step towards a non-contact meter filler, but at about half the cost; without requiring any steps backwards if the full meter conversion is on the horizon.
The filler has a spacing between valves of 7.06", therefore would be also suitable for running larger diameter bottles. The machine is rated at 200BPM on 20oz bottles with 38mm neck finish.
Should you be interested in receiving a proposal for the purchase of this machine, please let us know.
EL-G Filler Brochure
US Bottlers filler Press release
Telephone: +44 (0)1933 673677
Facsimile: +44(0)1933 676728
Mobile: 07836 323510
Email: info@glenvale-pkg.co.uk
For more information on EL-G-24-54" Electronic Gravity Filler is available for expedited delivery talk to Glenvale Packaging
Enquire Now
List your company on FindTheNeedle.