
Sign In
Sawing-Ahead
30-09-2021
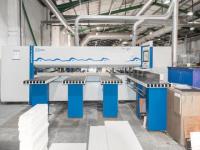
Sawing-Ahead
Atlas Leisure Homes are one of the UK’s leading caravan manufacturers, producing upwards of 44 caravans a week from their manufacturing facilities in Hull. But, when faced with an ageing beam saw that was breaking down three or four times a day and increasingly challenging turnaround times, the company needed to source a replacement or run the risk of falling short on their weekly orders. The solution was a Holzma Profiline HPL 510 beam saw from reconditioned machinery specialist, Ferwood.
“In our line of work, we can’t afford for breakdowns to impact our production lines,” begins Michael Mason, Machine Shop Manager at Atlas Leisure Homes. “We pride ourselves on offering our customers the very best service and a high-quality product. We can’t have our lead times dictated by unreliable machinery and continual breakdowns. When our production showed signs of slowing down due to our beam saw, we chose to work with Ferwood to find an alternative.”
Atlas Leisure Homes are no strangers to purchasing used machinery and have found it an economical way of purchasing high-specification machinery for their factory. “We’ve found that buying used machinery can be a really good value for money and if, like us, you have a good idea of the kind of machine you want, it’s often a really straightforward way of doing business. We were running our old Holzma beam saw for 18 years and were keen to continue using a brand that, until recently, had served us well. In addition to the build quality, the new model needed to work quickly and efficiently on batch orders and cut 400 panels over the course of two 10 hour shifts per day. It also needed to work with 12 and 25mm MFC, 11 and 25mm Sterling board, chipboard and plywood so both a main sawing unit and scoring unit were needed. The option of remote programming and integrated optimisation software that could help us reduce material waste and man-hours was also desirable.”
Following an online search, Michael got in touch with Ferwood, who stock a wide range of beam saw brands including Holzma. “We knew of Ferwood and came across several Holzma beam saws on their website that looked like they could work for us. Unlike other suppliers who often just service the machine before selling them on, Ferwood offered us a ‘Ferwood Approved’ beam saw that had been fully reconditioned from top to bottom and a six-month warranty to boot. Not only was this machine considerably cheaper than a new machine of the same specification, but we were also getting a reconditioned, fully serviced machine delivered to us at a time that suited us. It was a major selling point.”
Once fully tested by Ferwood’s specialist engineers, Michael flew to Italy to see the beam saw in action and, following an in-depth demonstration using their own materials, agreed for the machine to be stored until their summer shutdown.
“Our manufacturing facilities close for three weeks during the summer. It’s the only time we can afford to not have the beam saw up and running. The installation of the new saw had to take place during this timeframe and be ready to work as soon as we re-opened.” True to their word, the new Holzma Profiline HPL 510 beam saw was delivered and fitted within the agreed timeframe. The engineers even worked around a new extraction system that was being installed at the same time. “It went like clockwork.”
With its new beam saw in place, Atlas is poised to increase productivity. The new machine not only has rear rollers designed to speed up lateral preloading of the machine, but once loaded, it can also cut up to seven panels at a time, cutting the overall running time when putting time-sensitive, batch orders through the saw. Its software has also de-skilled the job of the operator and has reduced the risk of errors thanks to its clear and precise cutting patterns. The machine gives a clear indication of what needs to be done to optimise each job and directs the operator if re-cuts are needed. It even highlights what needs to be completed and when. “These functions are already proving valuable to production and have led to faster cutting, more effective use of labour and reduced material wastage.”
Michael adds, “Now we have good quality machinery in place, our next step it to look at more ways to automate our manufacturing processes and streamline our production. We’re already looking to incorporate rainbow stacking alongside the new beam saw to increase efficiencies further – something we would not have been able to consider without the installation of a fast and reliable beam saw. The Holzma beam saw has certainly impacted our business positively and we’re excited to see where our relationship with Ferwood will take us.”
For more information on Sawing-Ahead talk to Ferwood Machinery Limited
Enquire Now
List your company on FindTheNeedle.