
Sign In
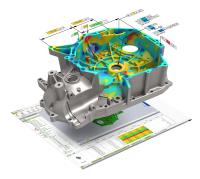
Reverse engineering is an important step in design, manufacturing and engineering processes. It is the means by which existing parts and systems are measured and analysed so they can be reproduced or improved.
Reverse engineering is an important step in design, manufacturing and engineering processes. It is the means by which existing parts and systems are measured and analysed so they can be reproduced or improved.
This blog looks at some of the benefits that 3D scans and other elements of additive manufacturing can bring to reverse engineering projects.
How can industry benefit from reverse engineering with 3D scans?
Reverse engineering with 3D scans is a process with applications in a wide variety of industries.
For heavy industries like oil and gas, reverse engineering provides designers and engineers with an opportunity to put parts and components into computer software, even if they were manufactured before CAD technology was available. This means that the oil and gas industry – and any other industry that relies on heavy, ruggedised machinery, such as shipping, construction and mining – can continually improve its machine systems without having to redesign the entire system.
The aerospace and automotive industries can both benefit from reverse engineering with 3D scans. In these industries, bringing new innovations to market is important to retaining a competitive edge. Equally important is quickly understanding competitor products, and if needed amending pipeline products to meet the new market opened up by the competitor. Reverse engineering with 3D scans provides a way of doing this quickly and with minimal resources.
As well as speed and efficiency, a major benefit of reverse engineering with 3D scans is the extremely high resolution that 3D scans can now produce. This means that even complex, organic shapes and surfaces can be accurately scanned and translated into a CAD model. As such, reverse engineering with 3D scans also sees medical applications. For example, prosthetic shells can now be designed as close as possible to the wearer’s existing leg, creating a better fit and experience for the patient.
Reverse engineering and 3D scans
Reverse engineering was – until the advent of 3D scan technology – a very labour- and resource-intensive endeavour. Traditionally, engineers would have to make extensive and complicated series of measurements. These left a lot of room for error.
Destructive testing – where parts or components are placed under controlled amounts of stress until they break, revealing information about the part or component. Of course, this is resource intensive.
3D scanning technology has enabled reverse engineering to become a straightforward and relatively cheap design process. Engineers can now simply scan the part or component they are working with, and use that scan to create a high resolution CAD model.
This model can be further improved to remove imperfections, add features, or create prototypes to better understand the part or component.
For more information on The Benefits of Reverse Engineering with 3D Scans talk to Evo3D
Enquire Now
More Case Studies / Blogs
List your company on FindTheNeedle.