
Sign In
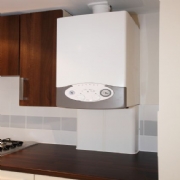
The initial indications from our ongoing study into social housing refurbishment, have already shown that savings of up to £¼ million could be made simply by using pre-formed plywood casings to conceal boiler pipe work rather than making them on site.
On average, when the costs of labour, materials, paint and fixings are combined, it costs £38 to box in gas and central heating pipe work below a boiler using plywood or MDF site made casings, compared to just £18 when using an Encasement pre-formed solution.
While a £20 cost reduction on its own is still a decent saving, when this is multiplied by the tens of thousands of properties included within a significant proportion of local authority and housing association programmes, it only requires work on 12,500 homes to achieve a saving of £¼ million. If boxing is required above the boiler to conceal flue pipe work, for example, then the saving quickly reaches £½ million.
These are surprising figures, perhaps for such a simple and straightforward task, but even this only tells part of the story. Our study also showed that the whole life costs for site made casings escalate significantly, when routine maintenance visits are factored in to the equation.
In the majority of cases, site made casings are damaged or destroyed during their removal, as the screw heads are filled and painted over, making them impossible or extremely time consuming to dismantle. Also, as each is individually made the quality in each property is likely to be inconsistent and detract from the overall finish of kitchens where boilers are located.
Pre-formed casings are self-supporting, have no screws to hold them together and due to their construction, can be secured using mastic adhesives or even Velcro pads. This makes them easy to remove and replace, while dramatically reducing the time that maintenance engineers need to be on site. Prior to adopting pre-formed casings, one housing association had a particularly complex and costly maintenance procedure in place, as a direct consequence of using site made boiler pipe casings.
When they needed to carry out routine boiler maintenance, a joiner visited each property and removed the casings in advance of a maintenance engineer calling. Once the work was complete, the joiner then returned to the properties to either refit or fabricate a new casing.
Apart from the disruption for the tenant and the extended time period to complete a simple process, the costs associated with transport and the labour costs for three site visits by skilled operators are considerable. Alongside this, the task of scheduling and co-ordinating such an operation on multiple properties is extremely difficult.
Although this could be an isolated case, the impact on housing association budgets can be significant, yet it is clear that considerable whole life cost savings can be made purely by installing pre-formed and pre-finished casings.
As a result it's a no-contest when assessing pre-formed boiler pipe casings against site made alternatives. The comparative fitting costs alone should make the decision to use pre-formed casings an easy one to make, yet when the maintenance aspects are factored in too, it becomes a no-brainer.
If any further weight is needed to this argument, then as Encasement boiler pipe casings are available using FSC Chain of Custody certified timbers from sustainable sources, it enables specifiers and installers to readily comply with legislative guidelines and sustainable procurement policies.
Case closed!
For more information on Making The Case For…Preformed Boiler Pipe Casing talk to Encasement Ltd
Enquire Now
List your company on FindTheNeedle.