
Sign In
CFD Case Study of Archimedean screw reactor
05-12-2023
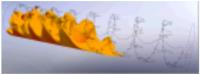
DC White were commissioned to provide analytical support for an extreme temperature Archimedean screw reactor vessel. A horizontal drum admits a solid discrete product which is pushed along the drum axis via an Archimedean screw with mixing paddles. The vessel sits within a furnace to heat the solid and gaseous products.
A major area of concern for the process is the limitations of heat transfer into the reactor. There are many heat transfer mechanisms both within the furnace and the reactor, including several heat paths for convection, conduction and radiation. Given the extreme temperatures, the radiation was predicted to be the largest but not dominant.
A MathCAD model was created to describe the complex network of heat transfers along with some basic chemistry using a one-dimensional treatment. This identified several key parameters which could not be well characterised by hand calculations alone.
In particular, the process of the solids tumbling within the drum is difficult to reconcile with 1-dimensional treatment. A major unknown is the quantity of product touching the drum and hence the typical thickness of the layer formed.
Analysis
CFD analysis was identified as a means of better understanding this process, although it would have to incorporate a rotating reference frame, heat transfer and a mixture of discrete solids and gases. The CFD analysis used Midas NFX 2015, using many of its advanced features together, so can be classified as a 'multi-physics' application.
There are several approaches for modelling the discrete solids. Modelling discrete elements is a cutting edge technology. However, it is computationally expensive and does not dove-tail in with other simulation options. Modelling the solids as a pseudo-liquid was seen as a more appropriate starting point.
No directly applicable advice was available in the literature for doing this. Heuristic investigation showed that modelling a pseudo-liquid with a low viscosity gave the most realistic representation of a discrete solid flow. This is counter-intuitive given that we think of sand for example, as having a high shear resistance compared with most liquids. The point is that discrete particles will rapidly tumble off a near-vertical surface since they are described by Coulomb friction which scales with the normal reaction pressure. Liquid viscosity at a surface interface however, resists velocity irrespective of surface pressure, gravity or orientation.
Findings
It was found that stratification alone proved incapable of keeping the tumbling phases distinct. The interface between pseudo-liquid and gas required the inclusion of surface tension to keep the phase boundaries non-diffusive. This is ironic given that surface tension does not in reality exist between discrete solids and gases. However, this proved to be a practical approach in lieu of a full discrete element simulation.
The option of a rotating mesh was not compatible with all of the boundary conditions, so a rotating reference frame was used instead. The Multiple Reference Frame (MRF) functionality requires the gravity vector, walls and mixture material to model rotation. Naturally, the screw action only works when all of these rotations are in the correct sense, which is by no means obvious. In this case, the screw remains stationary and the product trail moves circumferentially around the drum, as shown in
Mass fraction clipping (see the left hand side of figure 1 below), shows distinct phases whirling around the drum in the rotating frame, so in the stationary frame would pass along the bottom. The mixing of the paddles can be seen to introduce extra disturbance, exposing a greater surface area of product to radiation.
For more information on CFD Case Study of Archimedean screw reactor talk to DC White Engineering Consultants
Enquire Now
List your company on FindTheNeedle.