
Sign In
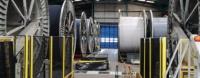
Machine guarding refers to the use of barriers, shields, and other devices to protect workers from potential hazards associated with the use of machinery. These hazards can include moving parts that can cause injuries from entanglement, cutting, and crushing, as well as flying debris and other hazards.
Properly installed and maintained machine guards can help to significantly reduce the risk of injury from these hazards. They can also help to improve productivity by reducing downtime caused by accidents, and can help companies to comply with OSHA regulations and other safety standards.
Regular inspections of machine guards are crucial in ensuring that they are functioning properly and effectively protecting workers from potential hazards. These inspections serve as a check for wear and tear on the machinery and guards over time, as well as for changes in the workplace or machinery that may affect the effectiveness of the guards.
In addition to compliance and safety, regular inspections can also help to improve productivity by reducing downtime caused by accidents. By identifying and addressing potential hazards before they cause an incident, regular inspections can help to keep the machinery running smoothly and prevent costly downtime.
Why Regular Inspections are Necessary
Wear and Tear on Machinery and Guards Over Time
As machinery and guards are constantly used in the workplace, they are subject to wear and tear over time. This can include physical damage to the guards, such as dents, scratches, or cracks, as well as wear on the moving parts of the machinery. These issues can compromise the effectiveness of the guards, increasing the risk of injury to workers.
One of the main reasons for regular inspections is to identify and address any wear and tear on the machinery and guards, before it becomes a serious issue. For example, a small crack in a guard may not seem like a big problem, but if left unaddressed, it could eventually lead to the guard breaking off completely, leaving workers exposed to potential hazards.
Similarly, wear on the moving parts of the machinery can affect the guards’ performance. For example, if a machine’s moving parts are worn, the guard may no longer be able to protect the workers properly, because the guard is not located close enough to the moving parts.
Changes in the workplace or machinery that may affect guard effectiveness
Changes in the workplace or machinery can also affect the effectiveness of guards, making regular inspections even more important. These changes can include modifications to the machinery, changes in the layout of the workplace, or the addition of new machinery.
For example, if machinery is modified or upgraded, the guards may no longer be properly positioned or may not provide adequate protection for the new moving parts. Similarly, changes in the layout of the workplace can affect the guards’ effectiveness, such as when new machinery is added to the area, and the guards need to be adjusted to accommodate the new equipment.
Regular inspections allow employers to identify these changes and make the necessary adjustments to the guards to ensure that they are still providing adequate protection. This can include repositioning or replacing guards, or making other adjustments to the guards or the machinery to ensure that they are functioning properly.
What to Look for During Inspections
Proper installation and function of guards
Proper installation and function of guards is a critical aspect of machine guarding and is a key focus of regular inspections. The installation and function of guards can affect the guards’ effectiveness and safety.
During regular inspections, employers should check for proper installation of guards, including that they are securely attached to the machinery and are not loose or missing. They should also check that guards are positioned correctly, and that they provide adequate coverage of the moving parts.
Proper function of guards is also important, and regular inspections should check that guards are functioning as intended. This can include checking that guards are properly adjusted and aligned with the machinery, that they are not impeding the movement of the machinery, and that they are not creating new hazards.
Identification and correction of potential hazards
Regular inspections are also important for identifying and correcting potential hazards associated with the use of machinery. These hazards can include not only those associated with the moving parts of the machinery but also with the environment around the machinery, such as inadequate lighting, poor ventilation, or poor housekeeping.
During regular inspections, employers should look for potential hazards such as missing or damaged guards, improper use of machinery, and unsafe work practices. They should also look for environmental hazards such as poor lighting, slippery floors, and cluttered work areas.
Once identified, these hazards should be corrected as soon as possible. This can include repairing or replacing damaged or missing guards, providing additional training for employees on the proper use of machinery, and implementing corrective actions such as improved lighting, ventilation or housekeeping.
Conclusion
In conclusion, regular inspections of machine guards are essential for ensuring the safety of workers. These inspections allow employers to identify and address issues such as wear and tear on machinery and guards over time, changes in the workplace or machinery that may affect guard effectiveness, and potential hazards.
By regularly inspecting machine guards, employers can improve productivity by reducing downtime caused by accidents, ensure compliance with safety regulations, and most importantly, protect workers from injuries. Regular inspections should be part of a comprehensive safety program and should be conducted by trained personnel and documented.
Employers should also keep in mind that safety should be a constant effort, not a one-time task, thus, regular inspections should be part of an ongoing process of ensuring a safe work environment for all.
For more information on The Importance of Regular Machine Guarding Inspections talk to Billington Safety Systems Ltd
Enquire Now
List your company on FindTheNeedle.