
Sign In
ELECTRIC Articulating Roller Forming Machine
Product Code: EA30M
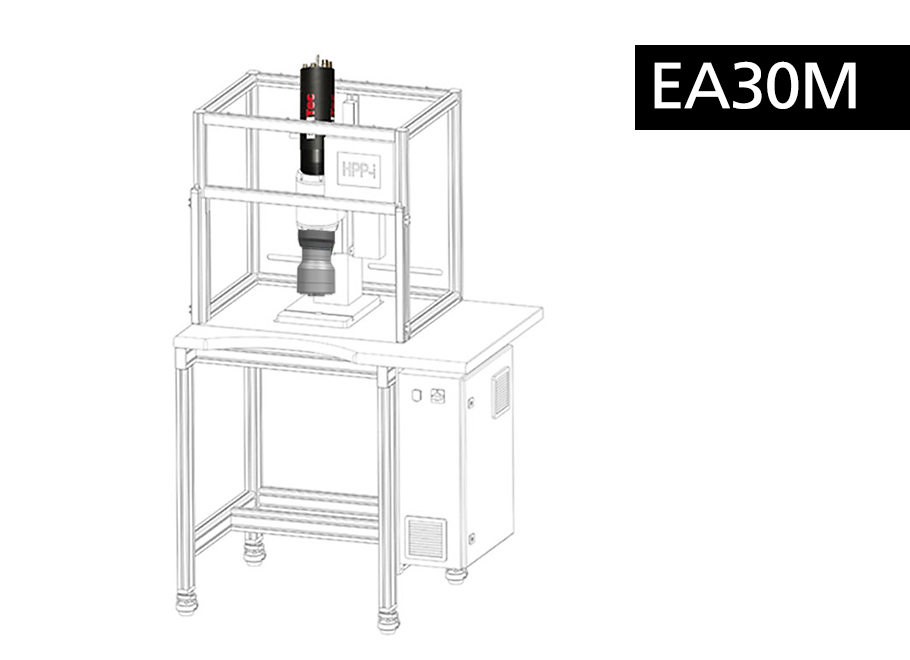
Description
Main Features
▪ Workcell with Roller Forming unit, incl. roller forming head: Net weight 450 Kg - Width 1200 mm – Depth: 1000 mm, Height: 2400 mm
▪ Control cabinet mounted on the side
▪ Enclosure with lift door at front including safety interlock
▪ Manual control box mounted on the frame
▪ HMI-Monitor (PC) with HPPi-Software installed
▪ C-Frame with integrated table, made from steel
▪ Floor standing table, steel structure with lockable swivel castors
▪ EK0-360, adjustable task light, LED
▪Process Module: Articulating roller forming
▪ Three axis servo controlled; Stroke Z, Rotation M, Radial movement
▪ Process data archiving of all axis
▪ Power supply: 3x380 to 480 VAC (45-65 Hz), 16A overload protection
Standard Version:
▪ Power unit with all sensors
▪ Process module with three-roller roller forming head
▪ Cable set between power unit and control cabinet
▪ Automatic spindle lubrication
▪ Two threaded rings
▪ HPPi PC-Software, based on Windows 10
▪ UDP communication module for process data upon request. No charge
▪ Safety standard PLe/SIL 3
▪ EC Declaration of conformity for machinery 2006/42/EC
▪ Assembly instruction and manufacturer’s verification certificate (force and path) at first delivery enclosed as hard copy – in English
▪ Operating Manuals and Software enclosed on electronic media (USB) in English
Technical Specification
Power Unit
▪ Force axial axis: 3.0 to 30 kN
▪ Linear Stroke: max. 200 mm, servo controlled
▪ Linear feed rate: max. 180 mm/sec, servo controlled
▪ Rotation Speed: max. 800 min-1, servo controlled
▪ Integrated mechanical overload protection
▪ Coaxial load cell (DMS) with amplifier allows true axial force measurement
▪ Axial path measurement via two independent measuring systems, monitored against each other
▪ Integrated motor temperature monitoring via servo drives
▪ Standard lubrication of the spindle, software monitored and controlled
Control Cabinet, complete and including
▪ Integrated fans for cooling
▪ Servo drives for three axis, power distribution, 24V power supply, integrated safety PLC, IP/Ethernet & USB port
▪ Main Switch in side wall
▪ CE Standard, IP50 – rating
▪ Optional – not included in this proposal
▪ Control Cabinet according to UL-Standard
▪ Main Switch through the door
Connectivity
▪ Ethernet/IP and USB 3.0 Connection
▪ Cable set between power unit and control cabinet 3.0 m
▪ Existing connections on the control cabinet:
▪ X111: Socket for Working light, Reserve
▪ X121: Socket for Lubrication of spindle and riveting head
▪ X131; Socket for Safety (light curtain, lift door interlock, other safety interlock)
▪ X141: Socket for external safety, reset, cycle permissive
Alternative a; > Delivery default / b; > Configurable by customer
▪ X151: Socket for Externa emergency Stop, start signal, permissive for work piece handling
▪ X161: Socket for PLC interface, cycle start, program selection, HPPi OK/Ready, Cycle evaluation OK/NOK
▪ X171: Socket for Manual Control Box
Optional – not included in this proposal
▪ X161; PLC-Interface, Plug with cable 5.0 m
Software HPPi
▪ Based on Windows 10 (64 bit) with integrated TeamViewer for remote access
▪ Program- and process data management with process curve visualisation
▪ Process data evaluation with feedback of OK/NOK status
▪ Work piece detection, various types of process start detection (RA)
▪ Password protection for different access levels
▪ Process parameter for axial & radial movement: Forming time, Forming path, Forming force, Spindle path, Linear- and Rotational speed
▪ Display of machine status information for diagnostics and alarm display/acknowledgement
▪ HPPi SW can also be used for offline diagnostics
▪ Predefined master programs available, can be copied and customized
▪ Manual operation in ‘jog-mode’ on separate screen
▪ Logging of all process data on internal PLC, on USB stick or on the customer network
▪ Graphical display of process curves and data, customizable
▪ Download of programs, data and curves for storage or diagnosis
▪ Ethernet IP interface as standard, UDP Protocol for process data available
▪ Software only works with BalTec ELECTRIC Products. No experience of servo drive programming required.
▪ OPC/UA Communication available (On request and with clear definition of the requirement)
Process module & Roller Forming Head for Articulating Roller Forming
▪ Roller forming head with 3 rollers. One set of application specific rollers included
▪ Force radial axis: up to 30kN, total of all three rollers
▪ Radial stroke (radius): 10 mm
▪ Radial feed rate: max. 10mm/sec, servo controlled
▪ Coaxial load cell (DMS) with amplifier allows true radial force measurement
▪ Radial path measurement via resolver integrated in roller forming head
▪ Work piece size & limitations – refer to dimensional sheet
Optional – not included in this proposal
▪ Down holder integrated in roller forming head
Subject to changes.
For more information on ELECTRIC Articulating Roller Forming Machine talk to BalTec (UK) Ltd
Enquire Now
List your company on FindTheNeedle.