
Sign In
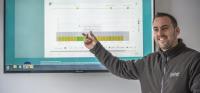
The brief answer is, it depends …
There are two main types of industrial rotary screw compressors available on the market.
• Fixed Speed
• Variable Speed (VSD)
The fixed speed compressor uses conventional starter gear to start the electric motor and run it at full speed. The compressor adapts to demand for compressed air by either producing 100% of it’s capacity, or none. When air is required it runs at full capacity, when demand for compressed air drops, it stops making compressed air altogether although the motor keeps on running.
This means that it is either using maximum energy to create compressed air, or slightly less than half of the energy to keep the motor running when it is not making compressed air. For instance, an 11 kW compressor will use 11 kW of energy when running at full capacity (known as ‘on load’) and 4.4 kW of energy when running at no capacity (known as ‘off load’).
Therefore a fixed speed compressor is energy efficient when it is supplying compressed air for a demand that is relatively static and matched closely to the maximum capacity of the compressor. Running this kind of compressor when demand is low results in wasted energy because the motor is using energy but there is no compressed air being made.
The variable speed air compressor uses an inverter to sense the variation in demand for compressed air and speed up or slow down the motor in response. This means that broadly speaking, the amount of energy used matches the demand for compressed air.
This means that a variable speed air compressor is energy efficient when it is supplying compressed air for a demand that fluctuates.
How do I know whether my compressed air demand fluctuates, or is relatively static? And would a VSD compressor save me money?
If you own a fixed speed rotary screw air compressor, it is possible to gain a general understanding of how much time it is running ‘on load’ (making compressed air) and ‘off load’ (running but not making air).
Some air compressors have control panels that record on load and off load running hours. Alternatively, you can stand with the compressor and take some timings. When the needle on the pressure gauge is rising it is on load and when the tone of the compressor changes and the needle falls, it is off load. If you record the time the compressor is on load and off load you can gain a rough understanding of the demand for compressed air at that time. For instance, if the compressor runs on load for 30 seconds and off load for 30 seconds, the compressed air demand is 50% of the maximum capacity of the compressor.
A calculation can then be applied to understand how much energy is being wasted in off load running time. This in turn can inform a decision about whether a VSD compressor would save money in the long run.
For instance:
• Total run hours per year 4,000
• Motor power on load 22 kW
• Motor power off load 8 kW
• Cost per kW/hr 12p
• Percentage time off load 50%
• Wasted energy costs = 4000 hours x 8 kW x 50% = £1,920 per year
A more detailed analysis can be carried out by installation of a data logger on the compressor. This monitors and records the energy used by the compressor over a longer period, for instance a week. The information is downloaded and presented in a report which provides a compressed air demand profile detailing the energy costs. Most compressed air companies are able to provide this service and some will offer it free of charge.
Other important factors to consider before upgrading your compressor:
Ensure the compressor you are considering is adequately sized – not too small but not too big either. You will want to consider the possibility of future growth so sometimes considering a compressor slightly bigger is a good idea.
Ensure you have minimum compressed air leakage in your pipework. Leaks are the single most costly issue in a compressed air system. Money is literally disappearing into thin air in wasted energy, compressor running costs, service costs and wear and tear.
Don’t run the compressed air system at a higher than necessary pressure. For every 0.5 bar increase in pressure, running costs increase by 5.25%.
There are Energy Efficiency grants available where funding can be claimed to offset some of the capital cost of energy efficient compressed air solutions.
There are many makes of compressors on the market, however it’s worth investing into a quality product so that you only buy once. An extended warranty is normally a good indication of quality. Aftercare support is also vitally important so if possible work with a company that manufactures the compressor in the country in which you are located. You can benefit from local aftercare and technical support.
Contact our team on 01359 272828 for further details on energy efficiency.
For more information on Will a variable speed air compressor save me money? talk to Avelair Compressed Air Solutions
Enquire Now
List your company on FindTheNeedle.