
Sign In
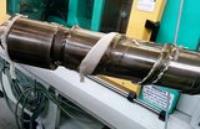
We spoke to Donatella about our latest case study which involved cleaning the screw of an injection moulding machine, a 250T Arburg – which produces parts for conveyor belts – that had been running PA66 Nylon but had not been manually cleaned for 7 months.
The company using this machine had been ‘pulling the screw’ and carrying out a thorough manual clean, which could take them about 12 hours, and is a tough job. So they were interested in trialing our Barrel Blitz Universal and on the 250T Arburg, because historically it needed the most attention.
We’re completely upfront in this case study as it demonstrates that sometimes our products don’t work in the way we expect them to.
As Donatella explains: “In this case study it shows that there has been a procedural mistake, as pre-melted BBU was left in the feed section of the screw which really shouldn’t be there. But this can happen if BBU is left in the hopper at elevated temperatures and you don’t purge.
It’s possible you could forget about BBU, you may go to lunch, or break for a cup of coffee and leave it there at the processing temperature. But you should only put BBU in the hopper when you are ready to purge.
And that’s because BBU is designed to purge as fast as possible. There’s no need to leave it in the machine, even for a short time. It’s not a chemical product so you don’t need any ‘soaking time’ just get it in and get it out.”
HIGH COMPRESSION… CLEAN. LOW COMPRESSION… NOT-SO-CLEAN
As you can see in the picture above, there is black material at the beginning of the feed section, which shows the PA 66 hasn’t been removed. But as you look further down the screw (from right to left) you can see how the nylon has degraded and is brown. This would indicate that an improper shut down or start up procedure was used, leaving the compression section with air and at elevated temperatures.
Neither of these areas are cleaned effectively with BBU because they are low compression areas. But if a correct stoppage procedure with heat reduction or a clearing out with a commodity polymer is used, this residue will reduce dramatically.
What we’re saying is that BBU has its limits, and it doesn’t work in parts of the machinery where there is no compression. Whereas in this image (below), you cannot see any degraded material on the metering section of the screw. This shows that BBU is working far more effectively.
What you can see though, is that BBU is ‘self-emptying’ below 240 degrees Celsius, so there is only BBU left at the screw tip and the first flight as seen at the left of the picture, UNLESS your screw and barrel are worn.
In this case BBU is left across the three flights, as you can see. The ‘take away’ from this image is that it shows the increase of temperature as a polymer material is squeezed over a worn flight.
Typically, the gap between the screw flights and the barrel wall is about 0.2mm, which is small enough to ensure no polymer flows over the flights.
As you can see on the right of the photo BBU has heated up quickly as it flowed over the screw flight, in fact the carrier has gone through a phase change from molten to liquid. As the filler in BBU is between 0.5mm and 1mm, on at least one of those three flights there is a gap of at least 0.5mm.
The downside of this screw wear is you may have to use more BBU to clean, more often and it may take more ‘Starve – Feeds’ to clear BBU when you have finished.
BBU CAN BE A BAROMETER FOR YOUR MACHINE
BBU can be used to strip the equipment and as a check on your screw and barrel. If you find deposits on certain areas it can help you to identify issues with the shutdown procedure, and if you find worn sections it can provide answers about moulding issues or determine when equipment needs to be replaced.
In a nutshell this case study highlights the limitations and effectiveness of BBU.
We believe Aquapurge is the only company that says you can purge with our products and don’t need to ‘pull the screw’ to give the equipment a thorough clean. But if you do use BBU to help ‘pull the screw’ it can give you so much more.
The key thing is that you must remove BBU while it is still warm, if it is left to cool then it could be very hard (in both senses of the word!) to remove.
TIMESCALES
Here’s a breakdown of how we purged the 250T Arburg:
We purge 40kg over 40 minutes at PA66 temperature (290 degrees Celsius)
We emptied the barrel and waited 20 minutes to go from 290 degrees Celsius to 240 degrees Celsius)
At 240 degrees Celsius we purged 1 kg to remove the ‘sticky’ (liquid phase) BBU
Then we ‘pulled the screw’
FIND OUT HOW BBU CAN HELP YOU PURGE OR ‘PULL THE SCREW’!
If you’d like to find out how Aquapurge products could assist a thorough and regular clean of your injection moulding machine please get in touch.
If you’re not sure about the benefits we’re only a phone or an email away.
For more information on WE 'PULLED THE SCREW' - EVEN WE'RE NOT PERFECT! talk to Aquapurge Ltd
Enquire Now
List your company on FindTheNeedle.