
Sign In
Colours without tears
02-12-2015
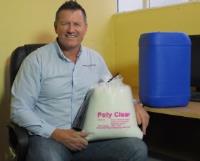
Leading purging compound developer
Aquapurge
reports that plastics processor versatility and ambition with
colour is driving an increased need for vigilance and precision when changing over tools and colour work.
Technical Director John Steadman says that ‘colourants and additives simply don’t always stay inside the polymer
carrier: This can be due to a multitude of issues, including; pigment and/or additive type; quantity of each; peak shear
rates, residence time and temperatures of processing.’
Since masterbatch suppliers are often reluctant to divulge their exact material formulations, ‘processors seek a
universal purging solution that can be guaranteed to shift a multitude of problems; chemical and physical. Our
customers want a one-shot deal that frees up their capital equipment in minimum time.’
Aquapurge
compounds are therefore designed to succeed in cleaning the production equipment from both
the coloured polymer; the plate out (concentrated colourant) and also the carbon residue (degraded plate-out or
polymer).
Barrel Blitz
and
Scrubber Freeze
are the two primary
Aquapurge
products for plastics processors in this
regard. They have been joined this month by the new formulation for blow moulders –
Poly Clear HMEX
.
The ‘hands on’
Aquapurge
approach to client work means that the company often gets to witness colour change
work from beside the moulding machine. According to Steadman, some ‘black arts’ are still sometimes necessary
and advised in order to guarantee successful results.
‘Moulders can do themselves a number of favours in the way they set up their materials handling and equipment
before the purging process begins. For example, it’s often a good idea to completely empty and clear one silo feed
on a machine, and then start another before then stopping that process in order to clean out the hopper loader
before the next colour run.’
Typically, many colours and formulations are not equal to others, notes Steadman. Many blues and red colourants
are bad for plate out, he says. Acetal materials often struggle not to have plate out and some yellows can also
degrade easily in processing. Pearlescents and metallics often pose difficulties in clearing and purging. Some
so-called universal carriers won’t work with certain polymers – Nylon and PET to name but two. In general, high
temperature polymers don’t like low temperature carriers as they can melt too early in the feed section of the screw,
causing cleaning issues.
Liquid colours also need special care in that the colour is an issue from the very start of the process; ie from the feed
section. For this reason,
Aquapurge Poly Clear
or
Carbon Clear
is best used to wash the liquid colour away
from the hopper throat. ‘Masterbatch,’ says Steadman, ‘normally only becomes an issue when it really starts to melt
– ie from the start of the compression zone.
Steadman also notes that understanding the role of varied pressure within moulding is essential to understanding
how purging works. ‘Screws and barrels are typically purged under low-pressure conditions. When you start up
moulding parts, however, the speed, pressure and the back pressure are greatly increased. It is for this reason that
many moulders often confuse hot runner colour/carbon issues with screw and barrel colour/carbon issues.’
Although where the issue is the hot runner
Aquapurge
have products which have also been developed for this
purpose.
According to
Aquapurge
, incorrect screw and barrel cleaning is responsible for 95% of carbon residue issues.
And if the moulded part has a tinge of the previous colour, or there are colour streaks on the part not originating from
the gate, then the screw and barrel have not been cleaned properly.
Although the disbenefits from not purging are obvious – faulty parts; arrested and problematic production –
Aquapurge
believes that moulders are now taking a more proactive stance and are seeing purging as part of
profitability and good practice.
PRESS RELEASE
Colours without tears
All further details from the company.
Unit 7, Craufurd Business Park, Silverdale Road, Hayes, Middlesex UB3 3BN. UK.
T: +44 (0) 20 8813 7990 F: +44 (0) 20 8848 8404 e: enquiries@aquapurge.com
www.aquapurge.com
‘In the past, colour scheduling was set in stone and many moulders could only organize orders around it. Waiting in
line became the norm for customers. Not so now,’ says Steadman.
‘A moulder that regularly purges its equipment is now able to reduce costs per part, increase turnover and reduce scrap.
It also indicates a business that is commercially flexible and able to supply new business as soon as it comes along.’
PRESS RELEASE
Colours without tears
All further details from the company.
Unit 7, Craufurd Business Park, Silverdale Road, Hayes, Middlesex UB3 3BN. UK.
T: +44 (0) 20 8813 7990 F: +44 (0) 20 8848 8404 e: enquiries@aquapurge.com
www.aquapurge.com
Now that’s how you bring out the blue
Clearing colour out of hot runner tool using
Poly Clear HR
Clear colour out of screw and barrel using
Barrel Blitz Universal
PRESS RELEASE
Colours without tears
Aquapurge
has been creating purging compounds for the global plastics processing industry for the past
nineteen years. Over 140 compounds have been developed to date.
Aquapurge
available capacity currently
stands at 15,000 tonnes of compound per year.
Aquapurge
produces three world-beating purging compound brands and in February 2013 also introduced
Poly
Clear HMEX
to the blow moulding sector. The new
Aquapurge
material looks like being the company’s most
versatile yet.
Aquapurge
is well known for its ‘hands on’ work with customers; and for its problem-solving abilities in plastics
processing.
Aquapurge
views its purging compounds as development partners for its customers in their aims for increasing
productivity across plastics processing; Injection moulding, Blow Moulding and Extrusion equipment. Purging with
Aquapurge
helps its customers to reduce colour changes, and to remove carbon and colour plate-out on plastics
processing machinery.
Purging with
Aquapurge
allows manufacturing customers in plastics processing to become more responsive to
their clients; reduce stock and inventory and raise margin and profitability.
All further details from
www.aquapurge.com
All further details from the company.
Unit 7, Craufurd Business Park, Silverdale Road, Hayes, Middlesex UB3 3BN. UK.
T: +44 (0) 20 8813 7990 F: +44 (0) 20 8848 8404 e: enquiries@aquapurge.com
www.aquapurge.com
Aquapurge
technical director John Steadman
with company’s new compound for blow moulders
,
Poly Clear HMEX
.
Sales start shipping
from this month, February 2013.
For more information on Colours without tears talk to Aquapurge Ltd
Enquire Now
List your company on FindTheNeedle.