
Sign In
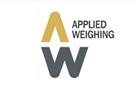
Approved weighing systems provide cost savings in hazardous areas
Applied Weighing, the UK’s leading manufacturer of weighing systems, is able to provide an extensive range of cost effective category 3D and 3G approved load cells for placement in hazardous areas.
Whilst little more than a nuisance to the average homeowner, dust in the workplace can have disastrous consequences. Aside from the more apparent problems that one might associate with dust emissions within industrial work areas, such as respiratory disease and impaired visibility, the risk of an explosion or fire is another all too real possibility. It is no wonder, then, that the task of evaluating explosive hazards has been afforded great importance, as in doing so can yield useful information regarding the dangers of particular dusts, and provide a means for determining how an explosion can be prevented.
A broad range of industrial materials are known to produce dust explosions, including pharmaceuticals, plastics, agricultural products and many foodstuffs. Within the food industry in particular, those dusts that are classed as explosive by the Health and Safety Executive, the UK’s independent watchdog for work related health and safety, include flour, instant coffee, dried milk and soup powder. Though seemingly innocuous, given the right conditions and a source of ignition, combustible dust particles can generate the same explosive results as those more commonly associated with gases.
ATEX stipulates that equipment be divided into categories in order to accurately define the zones in which the equipment may be used. For instance, zone 2 and 22 are defined as areas in which an explosive atmosphere does not usually occur during normal operation but, if it does occur, will only do so for a short period of time; the former being applicable to an area of gas and the latter to an area of dust. Given the prevalence of powdered products within the food industry, many work areas are designated as zone 22. Within zone 2 and 22, category 3G and 3D equipment may be used respectively, as such equipment does not represent a source of ignition during normal operation.
One of the advantages of using category 3G and 3D approved equipment is that it removes the need for zener barriers or galvanic isolators to be incorporated into the installation of weighing systems and other capital equipment within an area designated as zone 2 and 22. Ordinarily, a zener barrier would be included to divert potentially dangerous energy before it could reach the hazardous area. A galvanic isolator, on the other hand, would be used to isolate hazardous and non-hazardous area circuits. However, galvanic isolators can be an expensive outlay for manufacturers and, whilst zener barriers are initially less costly than galvanic isolators, the complex ground loop problems that can be associated with zener barriers may ultimately lead to higher maintenance costs being incurred.
Applied Weighing recognises the significant reduction in operational costs that avoiding the need for these barriers and isolators can bring to manufacturers. Conscious of the financial pressures placed on manufacturers to understand and comply with ATEX regulations, Applied Weighing offer a cost effective solution for the application of weighing systems in hazardous areas through the use of their category 3D and 3G approved load cells. Their experience and dedication in producing safe and innovative weighing systems also enables them to provide expert safety advice during the installation process and their maintenance service.
For more information on Approved weighing systems provide cost savings in hazardous areas talk to Applied Weighing International Ltd
Enquire Now
List your company on FindTheNeedle.