
Sign In
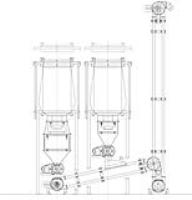
Concrete Evidence that Spiroflow are up to the job!
Our US sister company, Spiroflow Systems Inc., were able to provide a Phoenix, Arizona, based company with a reliable replacement for an existing mixing machine/packaging line feeding system that did not meet expectations. The customer supplies a comprehensive range of private label, dry package grouting, cement and concrete product mixtures specifically designed to perform under the climatic conditions on the West Coast of the United States. The company also exports some of these products to European and Asian countries.
At their 4,500 square metres facility, additives are processed, mixed with different grades of sand and then packaged in 25 lb or 50 lb bags for consumer sale. The bulk density of the additives can be up to 1.5 tonnes/cubic metre. Additives arrive at the plant in large sealed bulk bags, some as heavy as 1.8 tonnes, or in smaller 25 kg sacks.
To replace the current system, the customer at first considered bucket elevators but found that poor flowing materials, such as moist sand, did not flow efficiently and could affect productivity and, ultimately, sales. What the customer was seeking was a system in which all products flowed freely and consistently, that contained the dust during processing and which was economic and efficient to operate, using minimum manpower.
Our solution comprised two Universal Model Type 2 Bulk Bag Dischargers (BBD’s) and two Model PC3 Aero Mechanical Conveyors (AMC’s). These were installed by our sister company using with two heavy-duty rotary feeders to control the rate of flow from the BBD’s into the AMC’s. The equipment was custom designed by Spiroflow Systems Inc to fit the available space and handle material at the required rate of 5,800 to 6,800 kg per hour to meet the customer’s production targets.
Both Type 2 dischargers are used to discharge additives from bulk bags, but one of them has an optional, integral Bag Dump Station to accommodate minor ingredients from 25kg bags.
Universal Type 2 Bulk Bag Dischargers were specifically designed to handle poor flowing materials such as moist sand and to provide this customer with a controlled discharge capability by volume. Both dischargers can operate simultaneously, either discharging from 2 bulk bags or from a single bulk bag plus additives from sacks.
Materials dispensed from the bulk bags and/or sacks fall into a collection hopper which is an integral part of each discharger. Heavy duty rotary valves meter the contents from these collection hoppers into a single Aero Mechanical Conveyor operating at an angle of 10 degrees to the horizontal This conveyor has two inlets and feeds material from both dischargers to a second Aero Mechanical Conveyor that operates vertically to transfer materials into a mixer. Aero Mechanical Conveyors are designed to operate at any angle between 0o and 90o without loss of capacity. A near horizontal unit feeding directly into a vertical unit of the same cross-section size is proof enough of this.
The 'Spiroflow' bulk handling system was installed in 2005 and has been operating trouble free since then with virtually no maintenance problems or downtime other than cleaning and rope tensioning of the Aero Mechanical Conveyors. Only one operator is required to operate the system instead of three or four with previous system.
The bulk bags and 25kg bags arrive at the facility sealed and are transported by forklift truck to the dischargers. The contents of the 25kg bags are manually introduced into the system via the Bag Dump Station integral to one of the dischargers. Material is dumped through an access door with a 35mm grid across the opening for safety. Special lifting frames with forking channels are used to raise the full bags into the discharger and to support the bulk bags whilst they are in the dischargers. The bag support frames sit on the spring loaded vertical support arms. These raise the bags as they empty. This greatly assists the discharge the bag’s contents and, at the same time, prevents the bag spout and the liner from sagging into the rotary feeders below.
Pinch bars keep the bags tightly closed until dumping begins. Access to untie the neck of the bulk bags is through the access doors in the dust cabinets above the material collection hoppers. Untying takes place after the pinch bars have been closed around the neck of the bags. Closing and opening of the pinch bars is only possibly once the interlocked cabinet door has been closed. The bag spout pinch bars control the flow and allow easy retying of partially discharged bags, if necessary.
An adjustable pneumatically controlled massager aids the flow from compacted or otherwise difficult bulk bags.
The near horizontal Aero-Mechanical Conveyor into which the 2 dischargers feed is 3m long and the conveyor that lifts the material up to the mixer is 5.5m tall. Both have 80mm diameter conveying tubes that assure a dust-free environment and clean handling properties. The high throughputs and total batch transfers of the conveyors make them well suited for this application.
An inter-locked access panel facilitates cleaning of the internal conveyor components and a vision panel in one of the conveying tubes enables operators to determine when cleaning is required.
Once materials reach the top of the 5.5m high vertical conveyor, they are discharged into a mixer. After mixing the finished products are gravity fed into a packing machine, where 10kg and 25 kg bags are filled and labelled.
For more information on Concrete Evidence that Spiroflow are up to the job! talk to Spiroflow Ltd
Enquire Now
List your company on FindTheNeedle.