
Sign In
WHAT CAN BE MADE WITH EXTRUDED PLASTICS?
26-09-2019
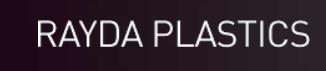
Different plastics are best suited to different applications; this is due to the way in which they’re formed. It gives them specific properties that suit certain environments or strength requirements.
Extruding plastics is an efficient way to produce a number of shapes and products for both industrial and home use. Although there are hundreds of uses for plastic, there are a few products that you will see more commonly that you might not be aware are extruded.
Insulated Wire
In the process of creating the insulated tubing for electrical wire, the wire is pulled through a die, and the insulation is extruded around it to create a snug fit.
For the wire to be able to perform at its optimal capacity, the insulation must protect the wire yet be supple and have an amount of abrasive resistance. The plastic coating also prevents the wire from reacting negatively with water and gasses.
The non-corrosive and non-reactive properties of plastic means that this material works well for insulating any type of wire – electrical or not.
Piping and Tubing
Pipes and tubes are one of the most common products created through the plastic extrusion process, and factors such as material used, size and strength vary depending on the application of the product.
PVC can be extruded to create pipes for water and sewerage, for example. PVC is one of the most commonly used plastic materials for pipes and tubing; but there are a whole host of other types of plastic materials that can be extruded to produce pipes or tubes for different uses.
These plastic tubes can vary in size and application, from something as simple and delicate as a drinking straw to medical piping or large and robust sewer pipes.
Using PVC for this product allows for the flexibility needed to create pipes for multiple completely different industries while still upholding the level of quality and the properties that all of the applications need.
Blow Moulded Items
Even plastic bottles start with extruded plastics. A piece of plastic will be extruded and fed through the mould to reach a certain length. Once the optimum length has been reached it will be pinched off and closed at one end, then injected with pressurised air to expand the plastic into the shape of the mould. This creates the signature ‘bottle shape’ that we’re all used to seeing on our shelves.
Film and Sheeting
Plastics can be extruded to make film and sheeting which have a whole range of applications and are used across domestic and commercial sectors. Whether it’s cling film that you’re using to wrap your food or huge sheets of plastic being used to replace the glass in your window frames, it starts with plastic extrusion.
Polycarbonate sheeting is used in window glazing and is impact-resistant, making it a great material for this. It can be extruded at different thicknesses to suit the specific application you’re catering for.
Clear plastic films like cling film, or similar, are extruded to a very fine thickness and are often used in the short-term protection of foods.
The original material used to create many blister packs, for example, such as the types used in medicine and pill packs, also start with extruded plastics – this plastic is extruded initially as a thin film that can be stored in rolls and then later be softened and moulded into the required shape.
Solid Shapes/Construction Materials
Extruded plastics can be formed into a variety of shapes and sizes, making them perfect for use in the construction industry.
Common examples of extruded plastics being used in this industry include decking planks and park benches. Extruded plastics work well for both of these applications because they’re a lot more lightweight and cost-effective than solid wood but still allow you the flexibility to cut the planks to the length you need.
These factors work well for a lot of applications in the industry, especially where wood may have previously been used before – plastic decking and boards are more weatherproof and splinter proof and will often outlast wooden competitors. They will age much more slowly and of course they are not at risk of rotting.
This is only a small snippet of the most common ways extruded plastics are used; it is by no means a comprehensive list.
If you’re interested in finding out more about the plastic extrusion process that we follow take a look at our blog. To help us help you in finding the ideal extruded plastic for what you need, get in touch with us at Rayda today.
For more information on WHAT CAN BE MADE WITH EXTRUDED PLASTICS? talk to Rayda Plastics Ltd
Enquire Now
List your company on FindTheNeedle.